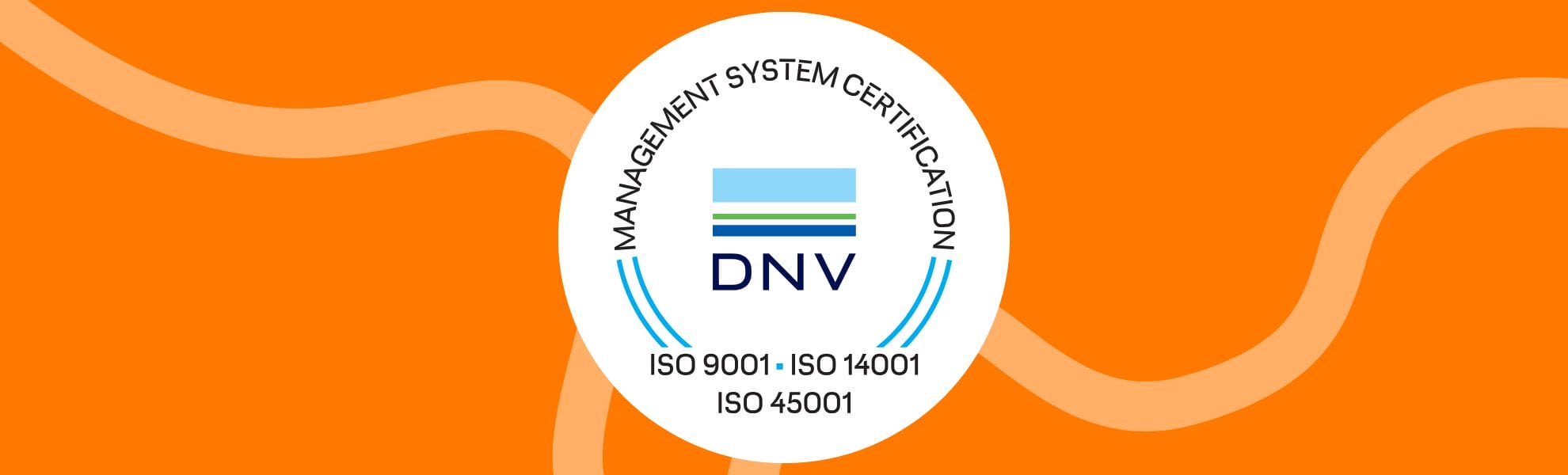
Ensuring quality with ISO 9001: An inside look
ISO 9001 is a globally recognised standard for quality management systems (QMS). The current version is ISO 9001:2015, and it specifies the requirements for a QMS, including:
- Processes for quality planning, control, and assurance
- Methods for monitoring and measuring performance
- Guidelines for documentation, internal auditing, and corrective & preventive action
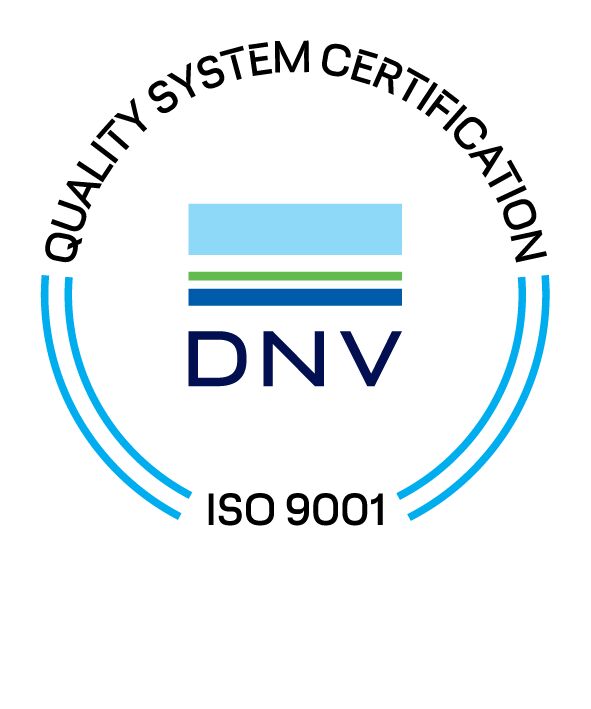
With ISO 9001 certification, we demonstrate that we consistently provide products and services that meet customer and regulatory requirements. This standard requires us to maintain a strong customer focus and continuously improve our processes to ensure an excellent customer experience.
To dive deeper into the principles of ISO 9001, we spoke with Harri Puputti, Director of Quality and Compliance at Lindström.
Our holistic approach to quality management
ISO 9001 applies to organisations of all sizes and sectors. In the 1990s, we were among the first companies to certify our quality management system according to ISO 9000 requirements, and we’ve been maintaining this certification ever since.
ISO 9001 is simply a guiding document—it’s up to our management team to make decisions related to the company strategy, vision, and direction. Harri explains: “ISO 9001 doesn’t give us anything more than guidelines. The organisation itself must make and document their decisions.”
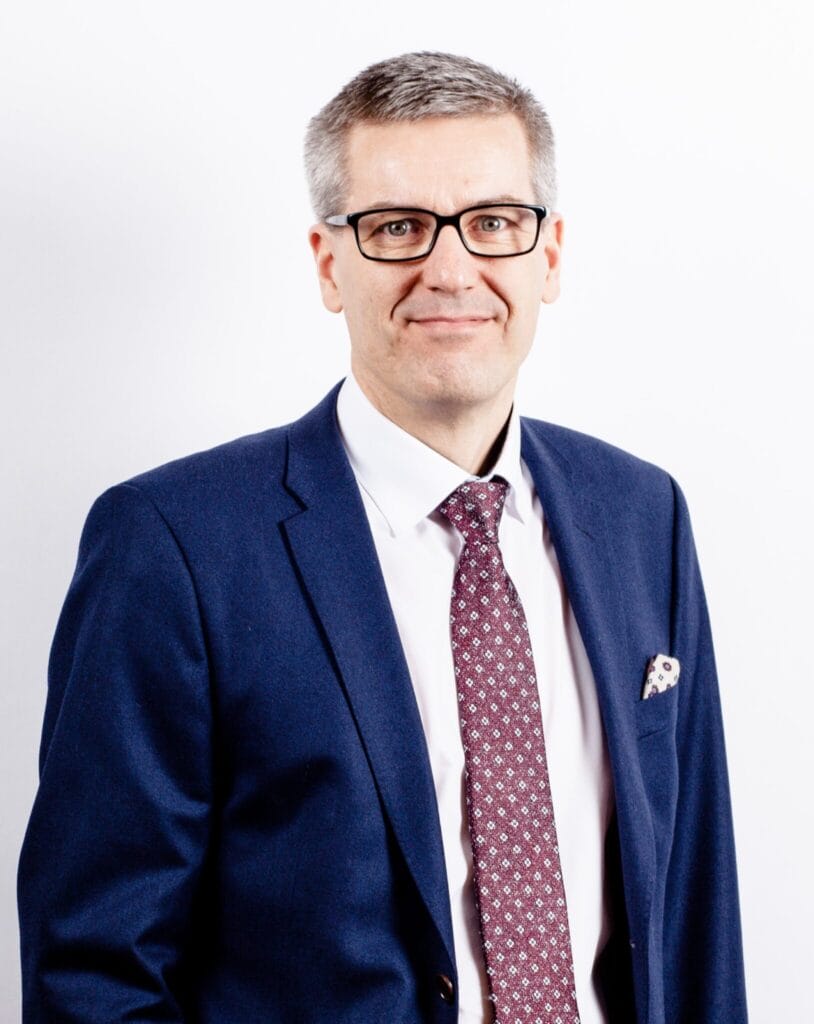
We take a holistic approach with our quality management system, as it supports our broader business strategy. Harri translates the standard’s definitions into business language so that our leaders understand how it helps us achieve our strategic goals.
Management system standards are built to support your business. They require you to document what you’re doing, building trust and awareness within the company. This enables you to work together for your goals.
Harri Puputti, Director of Quality and Compliance
The key principles of ISO 9001
ISO 9001 is based on seven quality management principles designed to help companies grow profitably, deliver value to customers, and ensure customer satisfaction.
Harri outlines these principles and their application at Lindström:
- Customer focus:
We understand our customers’ business needs and key requirements. We prioritise the customer experience, always listening to and considering their feedback. - Leadership:
Guided by our company values, our top management takes the lead in setting and implementing our quality management system. - Engagement of people:
With our communications department, we ensure every employee understands our policies, procedures, and guidelines and their connection to our business objectives. We involve everyone in strategy development. - Process approach:
We fully define our end-to-end processes in compliance with ISO 9001 requirements. - Improvement:
We identify threats to our strategic goals and recognize growth opportunities. - Evidence-based decision making:
We plan actions based on performance evaluations and other data sources. - Relationship management:
We manage relationships with all stakeholders, including suppliers, partners, customers, employees, legal authorities, and public organisations.
Harri explains: “When we operate according to our processes, we can deliver clean, well-prepared textiles to our customers on time and to the right place. Our long-term relationships with partners and customers are the best testimonies.”
Pharmaceutical spotlight:
Meeting even the most demanding industry requirements
We understand the critical concerns of our pharmaceutical clients, such as microbiological cross-contamination. That’s why we’ve developed specialised processes to ensure our workwear meets the highest standards of cleanliness.
Dressing healthcare professionals simply means meeting even the most demanding requirements […] Today, I am sure that our employees are as comfortable as possible.
David Mendl, Operations Director at Dr. Max pharmacies
Lindström has professionalism and in-depth understanding of pharmaceutical companies’ specific needs. Lindström has already helped us to pass several international audits, for example, for WHO and the EU GMP authority.
Mr Chen, Operation Manager at Beijing Institute of Biological Products
The role of auditing in achieving ISO 9001 certification
To achieve ISO 9001 certification, we undergo both external and internal audits. A third-party organisation evaluates our quality management system against the standard’s requirements. The external auditors report on positive outcomes, potential risks of non-compliance, and direct non-compliances. Their wide experience with other companies allows them to offer valuable feedback and recognise our performance level.
Auditing supports us to be a better organisation tomorrow than we are today. The auditing process is a development tool to ensure our continuous improvement. It’s important to have someone evaluate us, provide feedback, and suggest ideas for further improvement.
Harri Puputti, Director of Quality and Compliance
We track all audit observations, perform root cause analyses, and plan our next steps. And after setting the plan, we execute it and measure the impact of our actions.
Navigating the coming wave of regulations
Harri shares that compliance is now more important than ever. Meeting quality requirements helps us understand and integrate sustainability regulations into our business.
“We need to enhance our processes to ensure our compliance with the tsunami of new European regulations coming. And with climate change being a reality, we must be well prepared.
Climate change is of course a risk, but it also brings opportunities. For example, our circular economy business model is something that we see as an opportunity: we can support our customers to fight against the negative impacts of climate change.
Harri Puputti, Director of Quality and Compliance