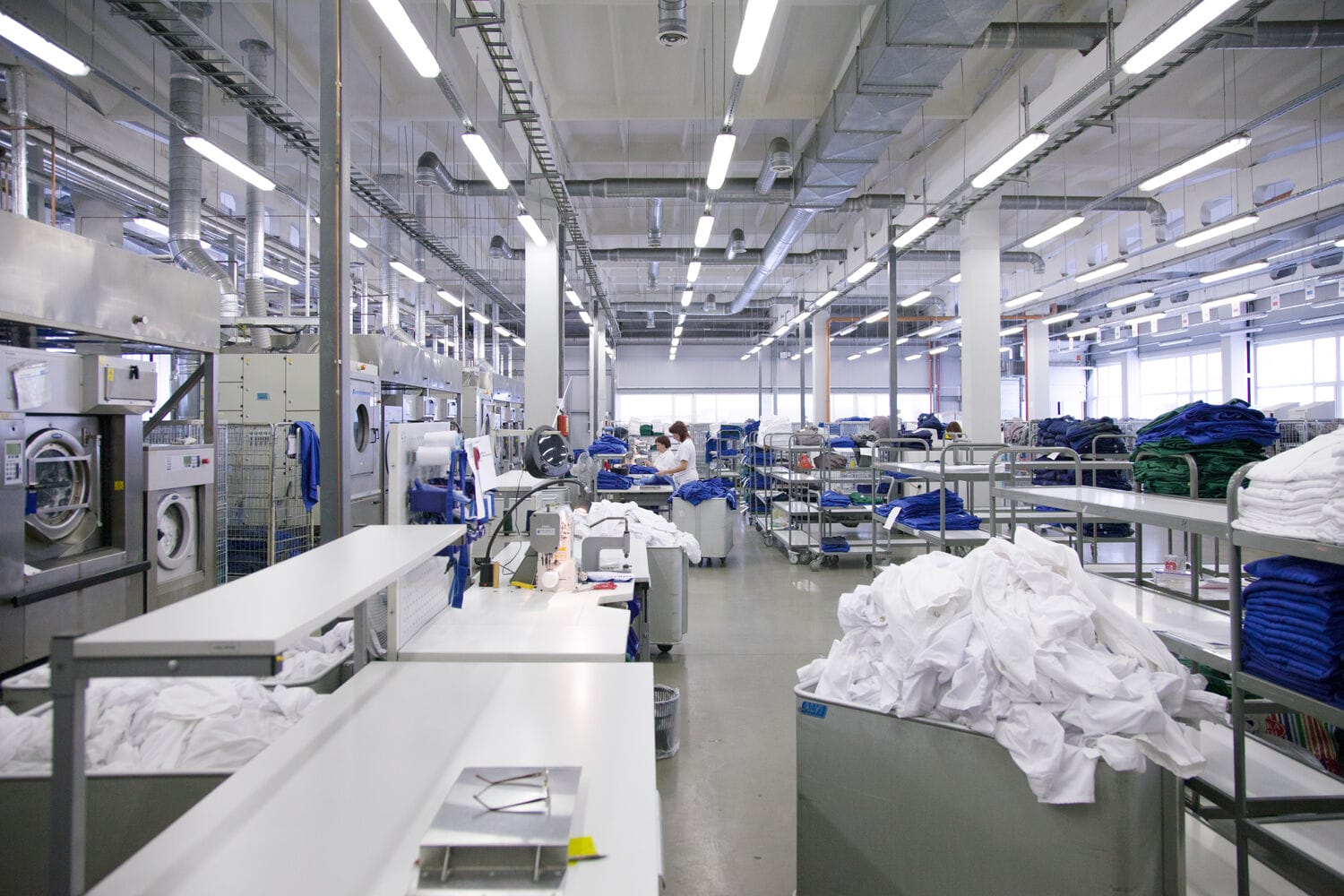
EN 14065: Ensuring microbiological safety in textile processing
Laundry Processed Textiles Biocontamination Control System EN 14065 applies to laundry-processed textiles that are used in the pharmaceutical, medical, healthcare, cosmetic, and food industries. It’s a quality control system that can be integrated into an existing quality system.
Like all standards, EN 14065 is revised every few years to stay relevant, and a new version of EN 14065 will be in place by the end of 2024.
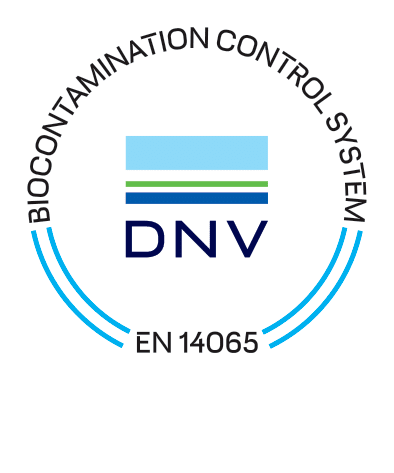
What do you need to know about EN 14065, and how can you ensure your organisation meets this industry standard?
In this article, Erika Szász, Head of Operational Excellence for Lindström Europe and an expert on hygiene topics, explains the essentials of the EN 14065 standard and what it means at Lindström.
EN 14065 in a nutshell
EN 14065 ensures that textiles meet specific microbiological quality standards suitable for their intended use, which is especially crucial for the previously mentioned industry sectors.
At Lindström, hygiene is our top priority. We incorporate EN 14065 into our operating system as our internal standard for hygienic quality. Our service centres follow the EN 14065 standard, which ensures the required hygiene level throughout the entire service process, from production to transport and delivery.
The value we offer with hygiene is safeguarding our customer’s business. By assuring hygienically clean textiles, we reduce the potential risks and contaminants and we protect the continuity of our customer’s processes and business.
Erika Szász, Head of Operational Excellence
Taking a step back, hygiene refers to conditions and practices that help maintain health and prevent the spread of diseases. In practice, this means we eliminate cross-contamination risks by using safe disinfection processes and maintaining hygiene rules throughout our operations.
Disinfection is the process designed to kill actively growing and vegetative forms of microorganisms. So when we disinfect, we eliminate most of the pathogenic microorganisms, meaning all the organisms that might cause diseases. This way, we ensure our customers always have clean and hygienic textiles.
The EN 14065 control system emphasises preventive actions over final product inspections. This standard doesn’t establish hygienic limits or address worker safety or the sterility of the final product.
Additionally, the EN 14065 standard itself doesn’t define hygienic limits. Rather, hygienic limits are defined company-wise or in national bodies of laundry hygiene. In our case at Lindström, the Laundry Hygiene working group part of the Finnish National Textile Service Association group sets the limits we follow.
Our laundry hygiene principles
We’ve established three core hygiene principles in our laundries:
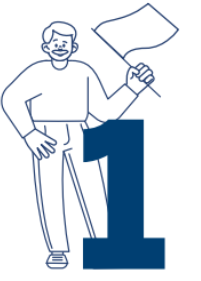
Ensure the disinfection of textiles in the washing process
This means we want to kill all the pathogenic bacteria or microorganisms at this early stage.
- We use adequate washing programs.
- We have internal quality measurements for temperature, time, washing circumstances, pH, alkalinity, and bleaching agents.
- After washing, we also monitor the total bacterial count on textiles and in the water by checking the textile surface and the soft water.
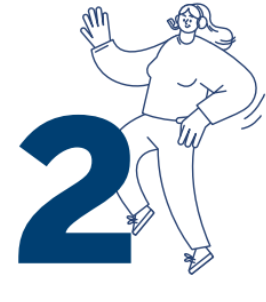
Prevent re-contamination after the washing process
- We rely on good manufacturing practices, which are regularly described, instructed, and monitored within the company.
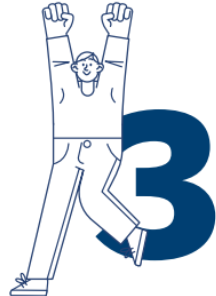
Keep personnel aware of their effect on hygiene
- Both personal and work hygiene are crucial.
- We regularly train employees on different hygiene principles. For example, we have a production manager’s handbook for new employees, and they also learn about hygiene as a separate chapter in their onboarding process.
By defining our own way of working and sticking to these principles, we ensure that our laundries operate the right way across the entire organisation.
EN 14065 is not only a certificate on the wall. To maintain these hygiene principles, we have to make sure that people understand their responsibilities. Every employee must be aware of the relevance and importance of their activities and how they contribute to the achievement of the microbiological objectives. This is ensured by training personnel and partners in co-operation,”
Erika Szász, Head of Operational Excellence
How we ensure microbiological safety during washing
Thanks to our risk analysis & biocontamination control (RABC) system, our laundries continuously assure the microbiological quality of the laundered textiles. During customer visits and audits, you can see how we implement our risk analysis & biocontamination control (RABC) system, and how we maintain hygiene principles in our operations.
As part of our RABC system, we’ve defined our critical control points in the laundry process. During the washing process, for example, we do weekly tests: we take random samples from the washing water to ensure washing conditions and parameters (like pH, temperature, alkalinity, and bleaching agents) are up to the planned technologies.
We also take samples from processed textiles every second month to check the total bacteria count. For these tests, we use Hygicult TPC testers, or in some cases RODAC plates or Petri dishes.
In addition to these internal tests, we also do third-party lab tests. “We want to ensure disinfection really happens in the washing. So once a year, we take third-party bioindicators to check the killing rate of the bacteria,” says Erika.
Staying ahead of evolving industry standards
To ensure our customers remain compliant with EN 14065, we closely monitor changes in requirements and adapt our actions accordingly.
“We are part of the European Textile Services Association (ETSA), where together with other stakeholders from the market, we closely follow and react as needed to any upcoming changes in requirements,” summarises Erika.