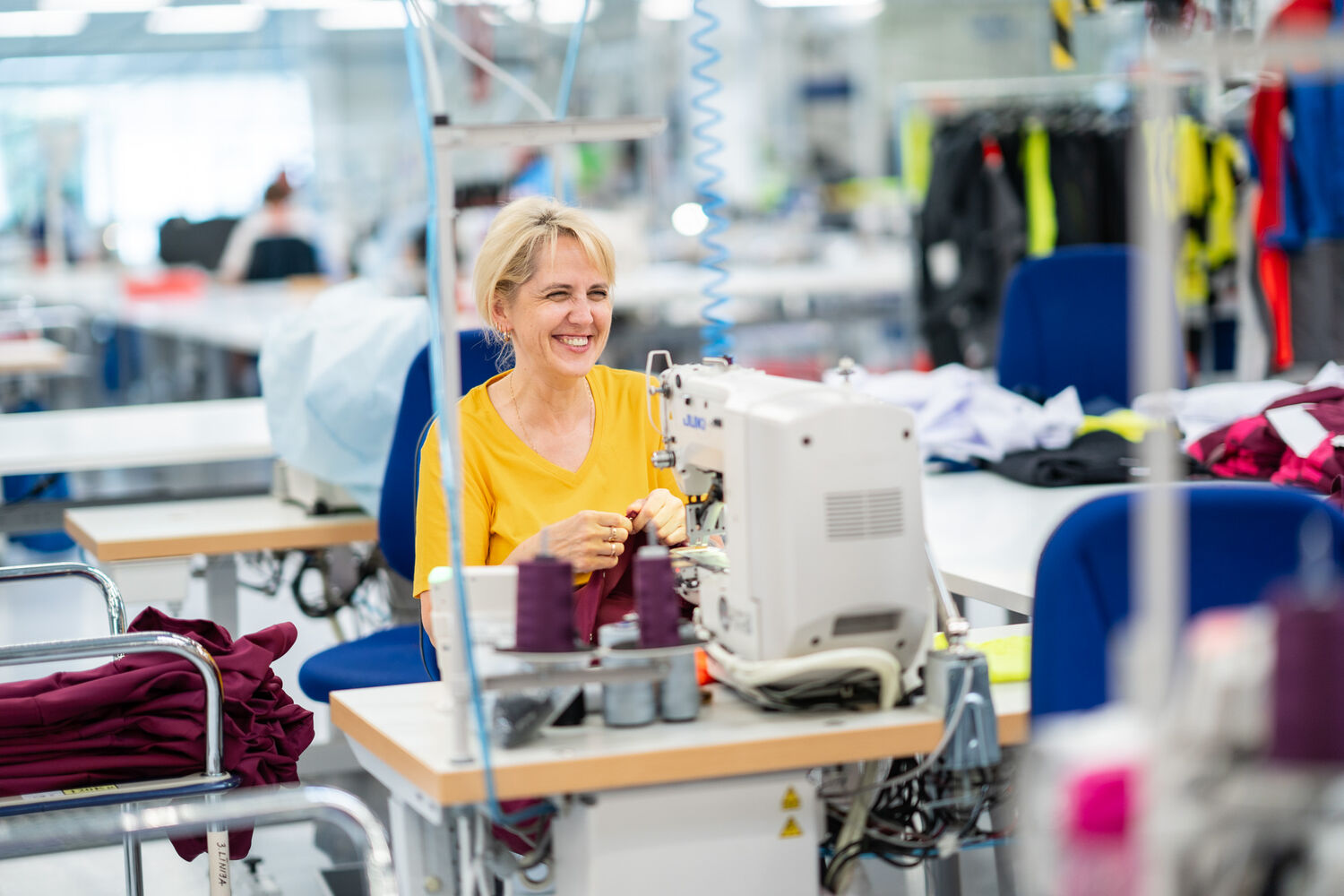
Towards net-zero workwear manufacturing
PRODEM Hungary is one of Lindström’s three production-on-demand factories. It is a shining example of how commitment to sustainability permeates all parts of the operation. The PRODEM model is an integral part of Lindström’s journey towards Net Zero by 2050. While juggling hundreds of materials, models and sizes requires diligent planning and a new way of thinking from the 160 employees, manufacturing workwear on demand is a giant leap in reducing emissions and waste.
“PRODEM is a unique workwear manufacturing concept. It means that we produce our workwear with extremely short lead times, based on customer orders.” explains Zsolt Keresztes, Managing Director for PRODEM Hungary.
In 2023, the average order size from the factory, located in Kazincbarcika in northeastern Hungary, was only 2.5 clothing items. The garments are made to order and shipped to Lindström’s customers in 14 countries. The process happens in just one to three business days.
“We have a responsibility to move garment manufacturing away from the ‘fast fashion’ mentality. We want to move to a place where we produce high-quality products that will be in circulation for a very long time,” Keresztes states.
Keresztes has been in the textile industry all his life: his family owned a garment factory in Romania. He has witnessed first-hand the massive shift in the industry’s attitude towards sustainability.
“The environment was not a focus area even five years ago. Now, our customers are demanding it. It’s not a decision if you want to be sustainable; it’s a must. We’re happy to see that more and more customers are asking about the sustainability of our supply chain.”
Panels and batteries cut emissions and costs
Lindström acquired the Hungarian factory in 2019, retrofitted the facility and trained the employees according to the PRODEM concept.
“After we used all the potential of designing our operation in an energy-efficient way and having the latest technology, such as machines that are only running when in use, we decided to take the next step. We investigated how we could further reduce our carbon footprint,” Keresztes explains.
While workwear manufacturing may use significantly less electricity than producing yarns or textiles, Keresztes stresses there is always room for improvement.
“We cannot just sit back and say, ‘OK, we’re not a very energy-intensive industry, we don’t need to improve anything´. That’s not the right mindset. We must work continuously to see what we can improve and how to improve further.”
In 2023, PRODEM Hungary signed a contract for 100% green electricity. We complement the power from the grid with in-house electricity production. Solar panels generated 22% of all power used in 2023. Another critical piece of the electricity puzzle is the battery solution. It ensures that the power generation during non-working hours is not wasted.
“I am very happy with the outcome. Combining solar panels with battery packs is a good match for our factory,” Keresztes says. In 2023, the renewed energy system reduced the factory’s carbon footprint by 29 tons of carbon dioxide. We saved a significant amount of money by doing this.
There were additional benefits to installing solar panels and battery packs, too. Some of the essential safety systems, like the fire security system, are now connecting directly to the batteries, increasing overall safety.
Smart systems ensure energy efficiency
The old factory building also had some outdated infrastructure that needed updating.
“We were not able to set different temperatures to different areas of the factory based on working times. We couldn’t lower the temperature inside the building over the weekends and holidays when the factory is not operating,” Keresztes says.
No suitable commercial solutions were available. So the factory collaborated with a local company to create a smart heating control system that allows setting different temperatures in six different areas. The overhaul has led to a significant 30% decrease in annual natural gas consumption. A similar system was recently set up in the new central warehouse.
Another energy efficiency milestone was replacing old hot water boilers and circulation pumps with modern solutions. At the same time, the boiler size was cut by 50%, which brings significant additional energy savings. The best part is that the employees, who use most of the hot water in the locker room, haven’t felt the difference.
“As part of Lindström’s We Care culture, we are focused on solutions which can bring savings. At the same time, we do not impact our employees negatively,” Keresztes says, smiling.
Awarded for innovation and sustainability
The factory’s efforts have not gone unnoticed. In 2023, PRODEM Hungary received two awards: Innovation in Manufacturing prize in the Hungarian Business Awards and Sustainable Manufacturing Grand Prix in the European Milestone Business Awards.
“Our business model is unique within the EU. The concept is not only considered an innovation but also the sustainability benefits have been recognized,” Keresztes explains. “Our PRODEM factories are proof that with a good concept and the right people, we can offer considerable operational, financial, and sustainable benefits to our customers.”
And the work does not stop here. Educating, training, and creating awareness – or cultivating a sustainable mindset shift, as Keresztes describes – is an ongoing project. In 2024, the factory will launch a program that rewards employees for their ideas on improving energy consumption or reducing emissions.
“Lindström has been very sustainable for a long time. I wanted to bring the same approach to our people and our operations. We want everyone to feel that they are part of this strategy.”
We will continue to develop
One of the focus areas in 2024 is recycling cutting waste. The factory has recycled all papers and foils used in the production process since 2022. The next step is to find a solution that allows the recycling of all textile materials.
“Even more environmentally friendly production is on top of our agenda as part of the PRODEM 2.0 project. There, the target is to review all our activities and develop our operation further.”
PRODEM HUNGARY
- Established in April 2019
- Located in Kazincbarcika, Hungary
- Supporting Service Centers in Central West Europe and South East Europe
- 160 employees
- Total produced pcs.: 217 885 pcs
- Average production time: 30 min / pcs
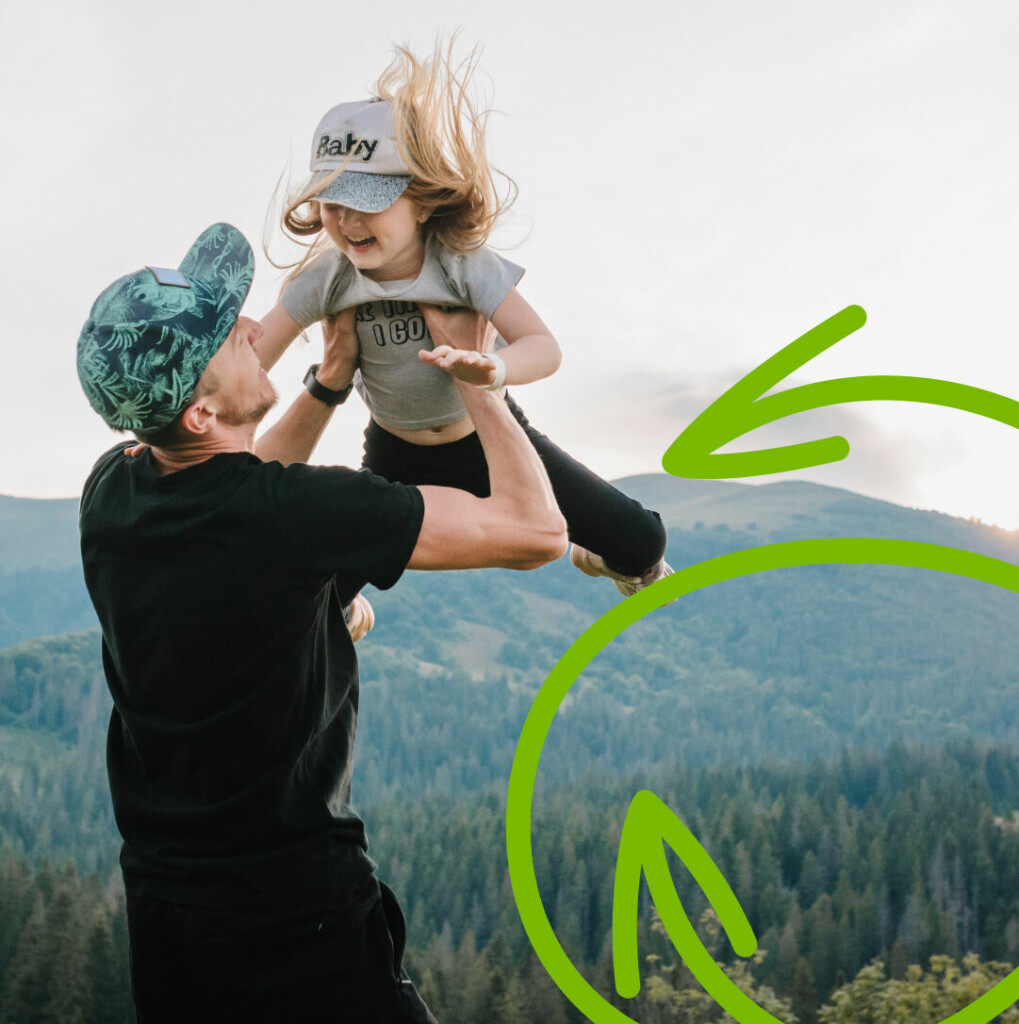