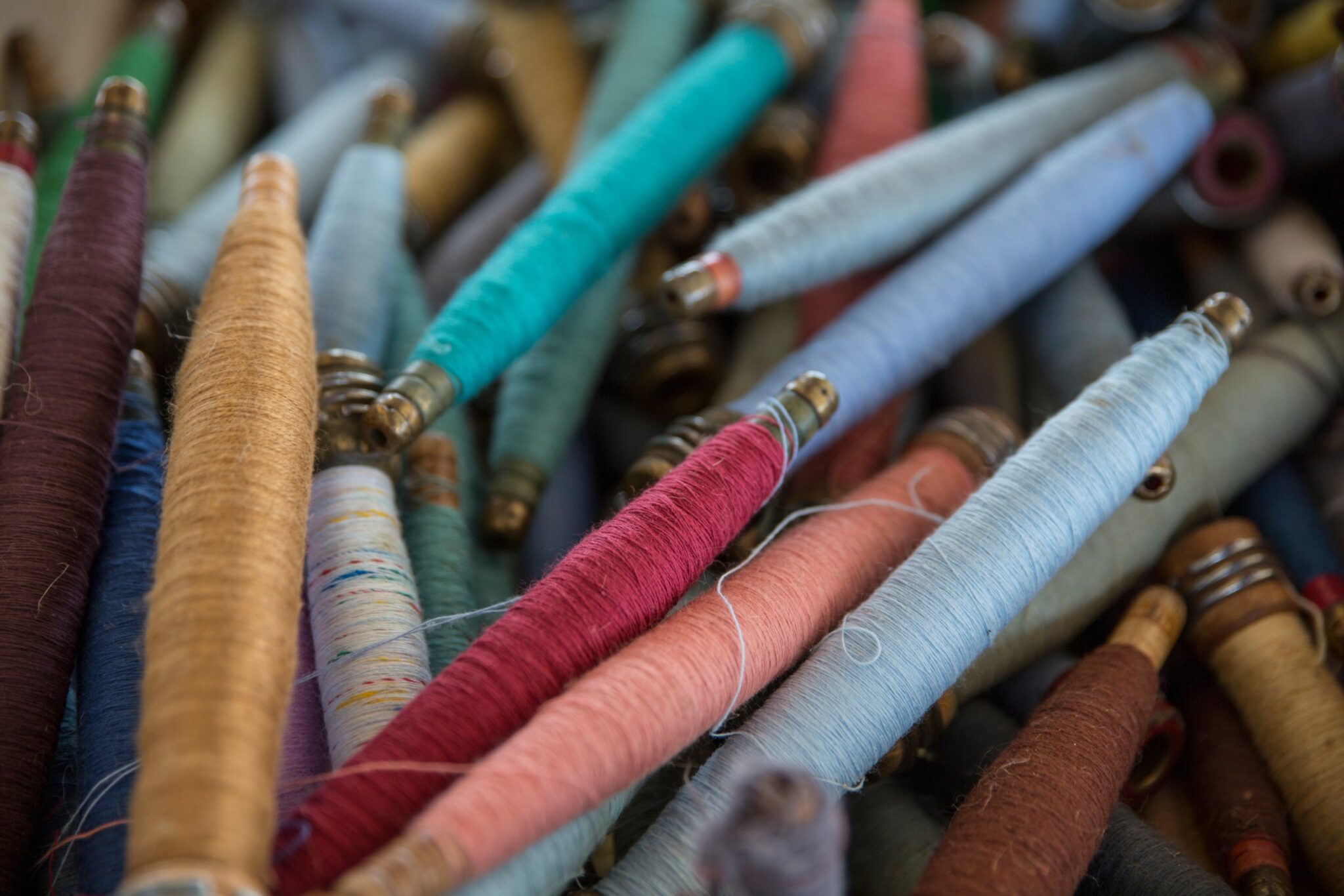
Sustainability and cost-efficiency go hand in hand
In our circular business model, sustainability will rarely conflict with cost-efficiency. In this article, our professionals share a couple of examples on how we make our service both sustainable and cost-efficient.
Reusable garments are an environmental choice
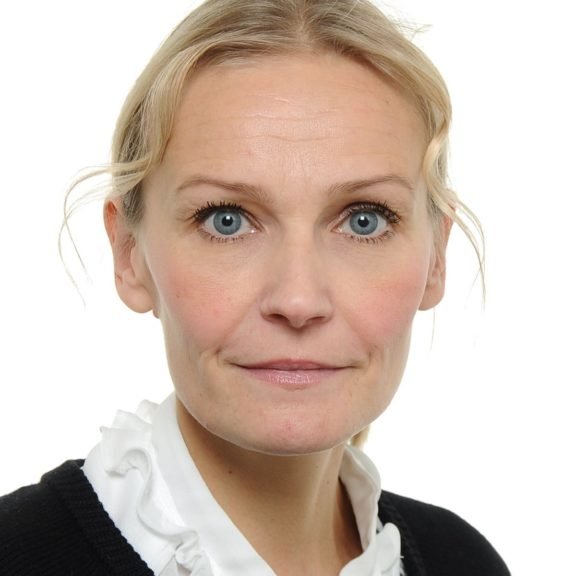
One of the best ways to reduce the environmental impact of a garment is to keep it in use for as long as possible. When clothes are used for longer, fewer natural resources are needed to manufacture new clothes and less textile waste is generated.
The reusability of our workwear is one of the cornerstones to extend the life of our clothing. By choosing their workwear collection or even parts of it from a reusable Lindström collection, our customers can do the environment a significant favour while saving on costs. According to our calculations, customer-specific workwear collection requires three times more textiles during its lifetime due to its limited reusability and has a 30% larger carbon footprint.
As the customisation also increases costs, the products of reusable Lindström collections are both more sustainable and cost-effective. We constantly plan different ways to effectively utilise reusable garments until the end of their life cycle. Before ordering new garments, we try to find garments that are in stock in other regions.
We have also considered the possibility to utilise used garments with new customers, instead of using them only in additional orders. Together with our Workwear Flex service that optimises the number of garments our customer needs, it would be resource efficiency at its best and would ensure that we order new garments only when necessary.
Producing new garments only when necessary
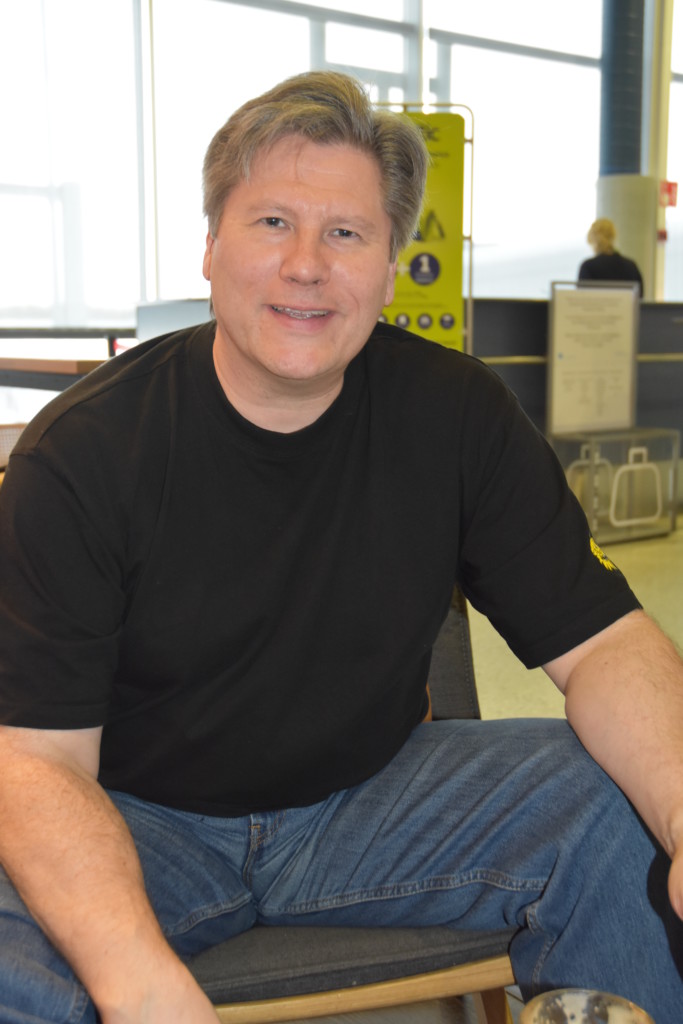
In today’s environmentally aware world, manufacturing goods without minimising the environmental footprint is no longer a ‘go’. Our PRODEM facilities (or PROduction on DEMand) use a dynamic customer-driven textile manufacturing practice developed by Lindström.
The main idea behind the practice is to be closer to our customers and react quickly to their needs. Our PRODEM facilities in Latvia, Hungary, and India provide our customers with garments from their nearest workwear manufacturing facility. The customer order acts as a signal to start the production.
Such manufacturing practices can meet even a small-scale need with the shortest lead time and simultaneously reduce overproduction and minimise textile waste. As workwear is produced on demand, there are no unused garments in customer stocks and no capital tied up in the inventory, making the practice both sustainable and cost-efficient.
Understanding and anticipating customer needs can shape win-win actions that are inherently sustainable and serve the customer in the best possible way. Our PRODEM facilities allow us to do exactly that. Being stationed close to our customer, not only can we respond quickly to customer needs, we can also avoid costs and carbon emissions from deliveries and excess stocks.
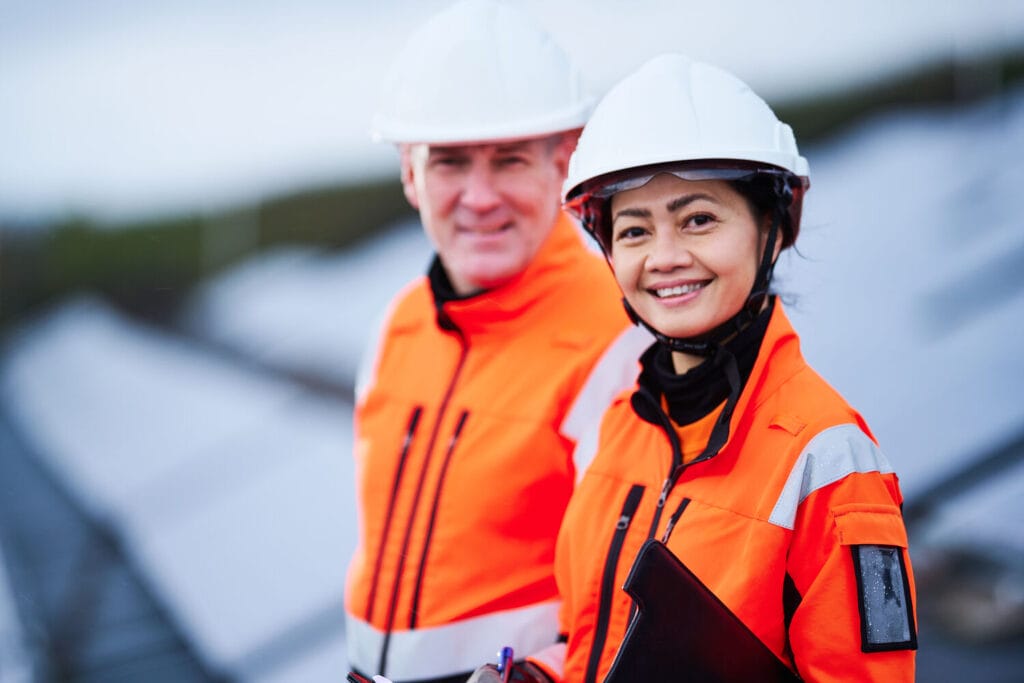