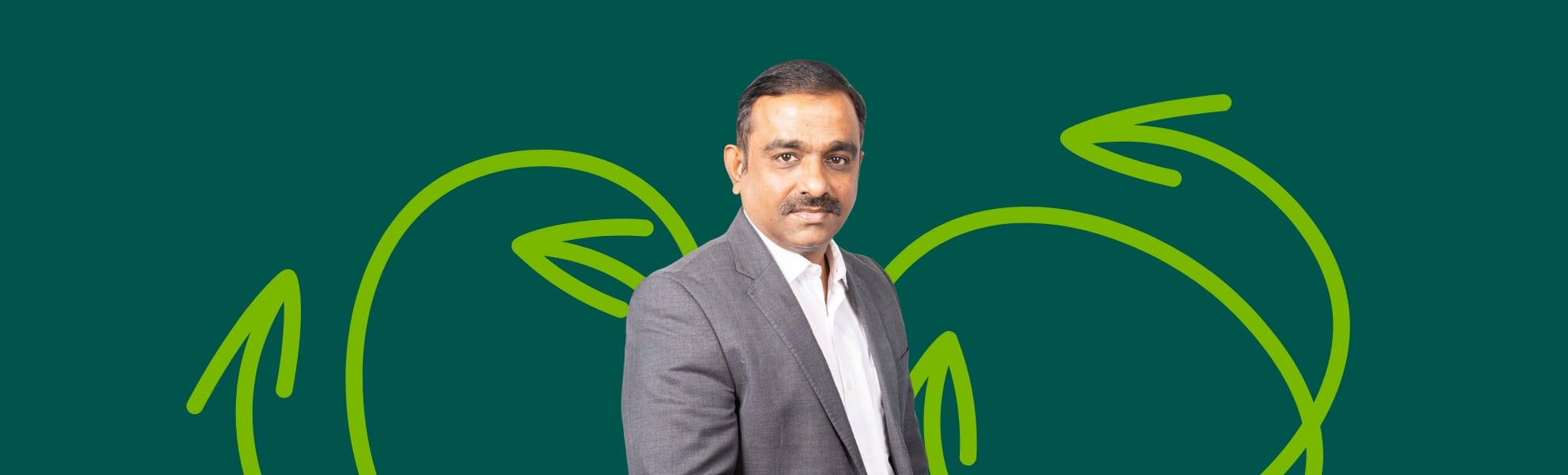
RFID revolutionizes cleanroom garment lifecycle management
Innovative technologies are making cleanroom garment management more efficient and reliable, and facilitating lifecycle tracking and compliance. Radio-Frequency Identification streamlines garment management, modernises the workflow, and eliminates the possibility of human error.
New Annex 1 guidelines call for robust systems for the lifecycle tracking of cleanroom garments. RFID technology provides a precise way to monitor garment usage. Each garment is fitted with an RFID chip programmed with a predefined lifecycle, such as a maximum number of wash and sterilisation cycles. An RFID reader will automatically verify whether a garment is within its lifecycle limits. If the limit is exceeded, the system identifies the garment for removal from circulation. Before RFID, tracking was done manually, increasing the likelihood of human error.
Clients, on the other hand, will be able to generate reports in line with Good Documentation Practices (GDP). They are stored locally or in a cloud, to demonstrate inspectors and auditors that every garment adheres to lifecycle limits. RFID technology therefore not only enhances tracking accuracy, but also ensures GDP compliance, generating reports in a format that cannot be altered and thus ensuring transparency and reliability.
“This is what cleanroom garment management is about: serving the client with a validated garment, which meets all the standards and is backed by a document”, says Manas Kumar, Global Director of Pharma at Lindström.
Addressing inventory challenges
Managing cleanroom garment inventory is another essential aspect of ensuring uninterrupted operation and production. Changes in schedules and the frequency of bio or coffee breaks can make it challenging to estimate daily garment needs. New garments are needed whenever someone exits and re-enters cleanroom environment.
Data produced by the RFID system helps optimize inventory by analysing and providing insights of usage patterns. This prevents overstocking or shortages, ensures that garments are always available, minimises excess waste, and prevents production delays due to lacking garments.
“Garments must not run out of stock”, Manas Kumar says. “If I come out of a cleanroom environment, I cannot re-enter if there are no garments. This will affect production.”
RFID technology also allows tracing the entire lifecycle of an individual garment – details of when it was washed, delivered, and used – at the touch of a button. This helps answer any questions an auditor or a regulator may have.
Future developments
There is still room for further developments in RFID technology.
“In the future, we need to look beyond this data. We are working together with the pharmaceutical industry to better understand how we can help them to be more compliant.
Manas Kumar, Global Director of Pharma
Future developments in RFID technology will focus on expanding traceability, making it possible to pinpoint contamination sources with greater precision. For example, if a garment is flagged during an investigation, RFID data can reveal when and where it was manufactured, which batch it belonged to, the departments it moved through, and how many times it was worn, washed, or sterilised. This allows companies to quickly isolate the root cause of contamination. Following that, they can take corrective action, and prevent similar incidents in the future.
As the industry evolves, clients are seeking more integrated solutions – such as utilizing RFID for access control to allow only authorized personnel enter cleanroom areas, or to monitor the number of people in a cleanroom environment at any given time, making sure the environmental conditions and occupancy limits have not been compromised.
Key takeaways
To meet the demands of the pharmaceutical industry, cleanroom garment management must prioritise compliance, reliability, and sustainability. As a thought leader in the business, Lindström wants to support clients in remaining competitive and compliant in a rapidly changing regulatory landscape.
Advanced technologies not only simplify garment lifecycle management. It also help pharmaceutical companies maintain precision, adherence to rigorous standards, and align with sustainable practices.
Comparision between Manual Process and RFID checking
Description of parameter | Manual system (In-house) | RFID (Lindström) |
Soil sorting or pre-inspection of the garments | Manual method and need to log the details. Having chances of missing entries and human errors. Chances of rejected materials mixing in with good ones. | Each garment is visually checked under lens and scanned using RFID. Challenged garments will be tagged and monitored. |
After washing and drying | No visual check of the garments. Separate logs will be maintained for washing and drying. Chances of human error and lost count. | No visual check of the garments. Separate logs will be maintained for washing and drying. Chances of human error and lost count. |
Packing of the garments | Packing of garments will be done under laminar airflow. Logbooks will be maintaining for packing of the garments may resulting in human errors. | Packing of garments will be done under laminar airflow. |
Sterilization of the garments | Sterilization of the garments processed as per the parameters and unloaded under laminar airflow. Separate logs will be maintained for Autoclave, garments sterilization tracking and unloading towards the sterile side which includes LAF pressure. | Tracked through RFID method which is digital and compliant. Online documents will be generated, meeting the regulatory requirements. |
Post sterilization of the garments | Garments will be visually checked for integrity and other parameters. Separate logbook is maintained to verify the pack may lead to human error. | After washing and drying, each garment will be scanned for RFID, and rejected garments will be tagged and sent for washing and drying. |
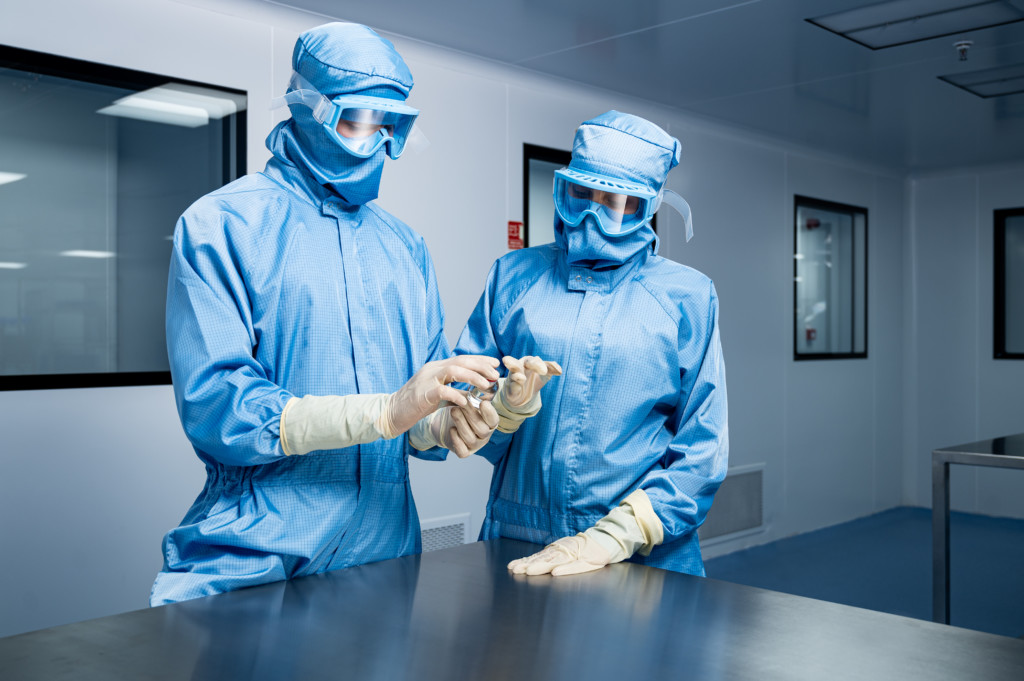