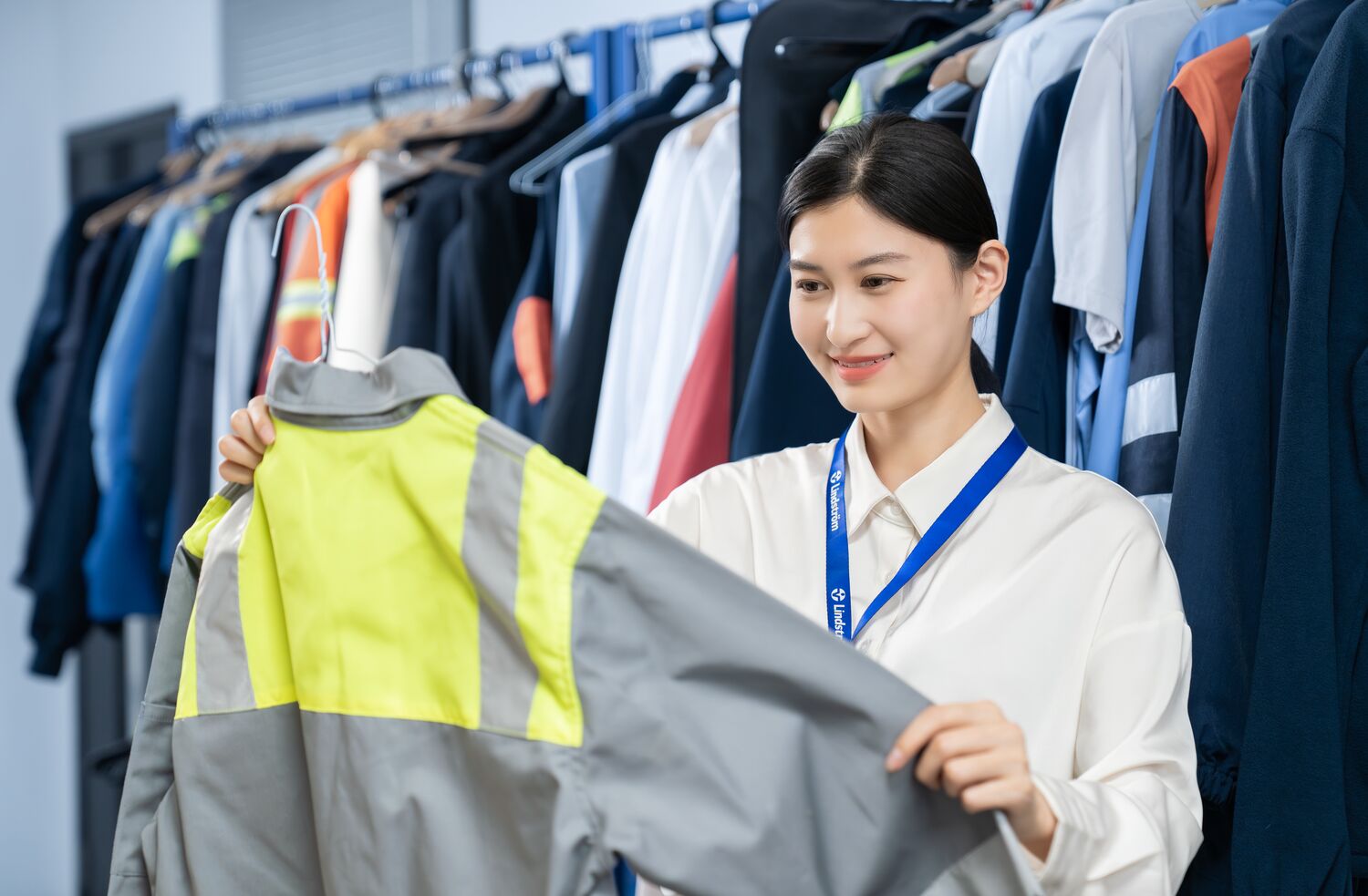
The benefits of inventory management in textiles
Optimising textile inventories is essential to the smooth running of your business. That is why choosing the best workwear management solution is a key priority for many organisations. As a procurement manager, production manager or other decision-maker, you are likely very familiar with the challenges of keeping track of uniforms and workwear in your company.
Every sector and company has its own unique textile situation. Hygiene standards, types of garments, and production processes differ from industry to industry. Furthermore, even companies within the same sector have different storage capacities and needs.
Despite these differences, the challenges of managing inventories are similar across all industries. And the benefits of inventory management, when done well, produce positive results for any business.
The challenges of managing workwear inventory
Here are some challenges that you might face if your organisation handles inventory management on its own:
Understocking and overstocking:
The number of employees at your organisation can vary throughout the year. This often results in too few or too many uniforms in stock. Overstocking leads to higher storage costs and takes up unnecessary storage space. Moreover, if unused garments are stored for too long, they risk getting damaged or lost.
Matching garments to your needs:
There are many different job types which require their own, unique workwear. If you work in a manufacturing facility, for example, production line workers will need one type of uniform, while cleaning staff will need another. Ensuring the right uniform size and type is available to everyone is a lot to manage.
The need for quality control:
Regularly checking your uniforms for dirt, tears or other damage is essential for maintaining quality and hygiene standards – as well as employee safety – but it also presents challenges to inventory management. Repairing garments and making sure there are replacements affects inventory levels and requires extra effort to manage.
Lack of storage space:
Many companies struggle to store their workwear due to limited space. This can lead to disorganisation, making it hard for employees to find clean, safe uniforms. Without proper storage, uniforms can get damaged, soiled or lost, affecting hygiene and increasing replacement costs.
Lost or misplaced garments:
It is normal for uniforms sometimes to go missing. Employees might forget to return them or accidentally take them home. Identifying and locating missing garments becomes a time-consuming task without proper tracking systems.
Inefficient use of resources:
Overstocking or understocking garments leads to a wasteful use of materials and resources. Moreover, there is a greater chance of garments becoming damaged, lost or obsolete, further contributing to waste.
If you find all these challenges to managing inventory overwhelming, then try not to worry! You are certainly not alone. It is the reason why we have developed smart ways to help you manage your inventory and tackle these challenges.
Renting workwear offers flexibility and precision
A rental textile partner can offer a comprehensive approach to textile inventory management solutions. Lindström takes care of everything from garment storage to lifecycle management. With local facilities, efficient processes, extensive expertise and digital tools, we streamline inventory management for your company.
We understand that the number of garments you need can fluctuate based on your staffing levels. That is why we offer flexibility in our service, allowing you to optimise the number of garments we provide. Instead of storing excess uniforms on your premises, we ensure that you only keep the garments you need for the week ahead.
Quality control is one of our top priorities. As part of our normal washing process, we perform thorough quality inspections. Through these inspections, we not only manage the lifecycle of your garments, but actively follow circular economy principles. This means we repair your garments for as long as they meet our high-quality benchmarks. When they no longer can, we replace them with fresh workwear that does. Furthermore, textiles that are no longer needed at one location can be used in another customer site, maximising their lifespan and reducing the need for new purchases.
With our digital tracking system, you will always know where your garments are. Whether they are being washed, repaired, or in transit, you can track their location in real time, giving you peace of mind and full visibility into your inventory.
We optimise inventory management, freeing your company to thrive without worrying about inventory challenges.
PRODEM, short for PROduction on DEMand, is a manufacturing practice pioneered by Lindström to meet customer needs while reducing environmental impact. Established in 2015-2016, PRODEM allows us to be closer to our customers and respond quickly to their demands by producing textiles only when ordered. This innovative approach operates in Latvia, Hungary, and India.
By ensuring garments are produced in response to customer orders, we avoid overproduction and minimise textile waste. This proactive approach prevents unused garments from piling up, enhances sustainability and streamlines inventory management for our customers. PRODEM ensures businesses get the garments they need without excess storage or waste.
The benefits of trusting your inventory management to us
By partnering with us, you can expect a range of benefits of inventory management, and beyond!
Freed-up capital:
When renting workwear, you can flexibly adjust the number of on-site garments according to your changing needs. Unlike when you buy workwear from a supplier in bulk, there is no large initial investment for your company. You flexibly pay as you use our services.
Assured garment availability:
With Lindström, you will never run out of essential workwear when you need it most. We help you ensure that your inventory levels are always optimal. Whether it is a sudden surge in staff or unexpected changes in workload, you can trust us to have you covered.
Space efficiency:
Limited space is a common challenge for businesses of all sizes. Renting textiles, you avoid having unnecessary garments that take up extra space. While making the most of available storage space, it still remains easy for employees to find the workwear they need.
Focus on core tasks:
Managing textile inventories is time-consuming, requiring employees to handle ordering, storage and maintenance. Partnering with us frees up your employees to concentrate on their essential duties.
Sustainability centricity:
With Lindström services, textile waste is minimised through garment reuse. Our quality inspections and maintenance extend the life of your textiles, supporting your sustainability goals. We also recycle your garments at the end of their lifecycle.
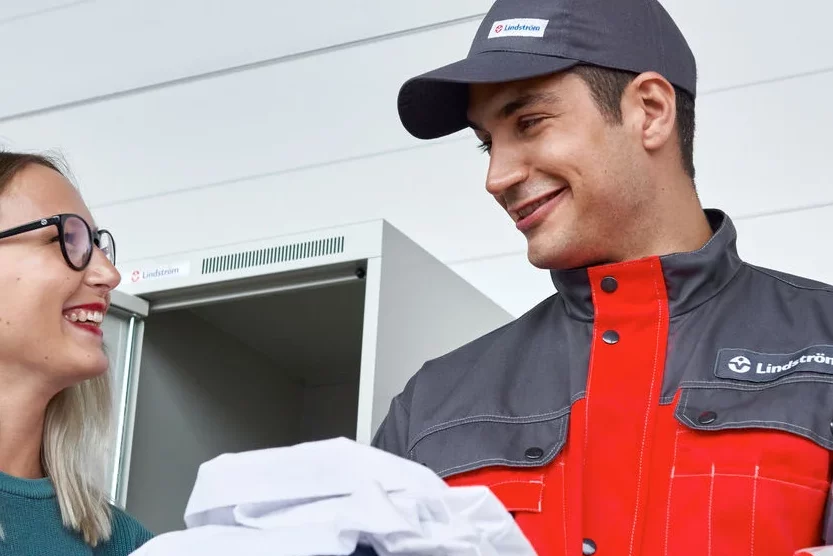