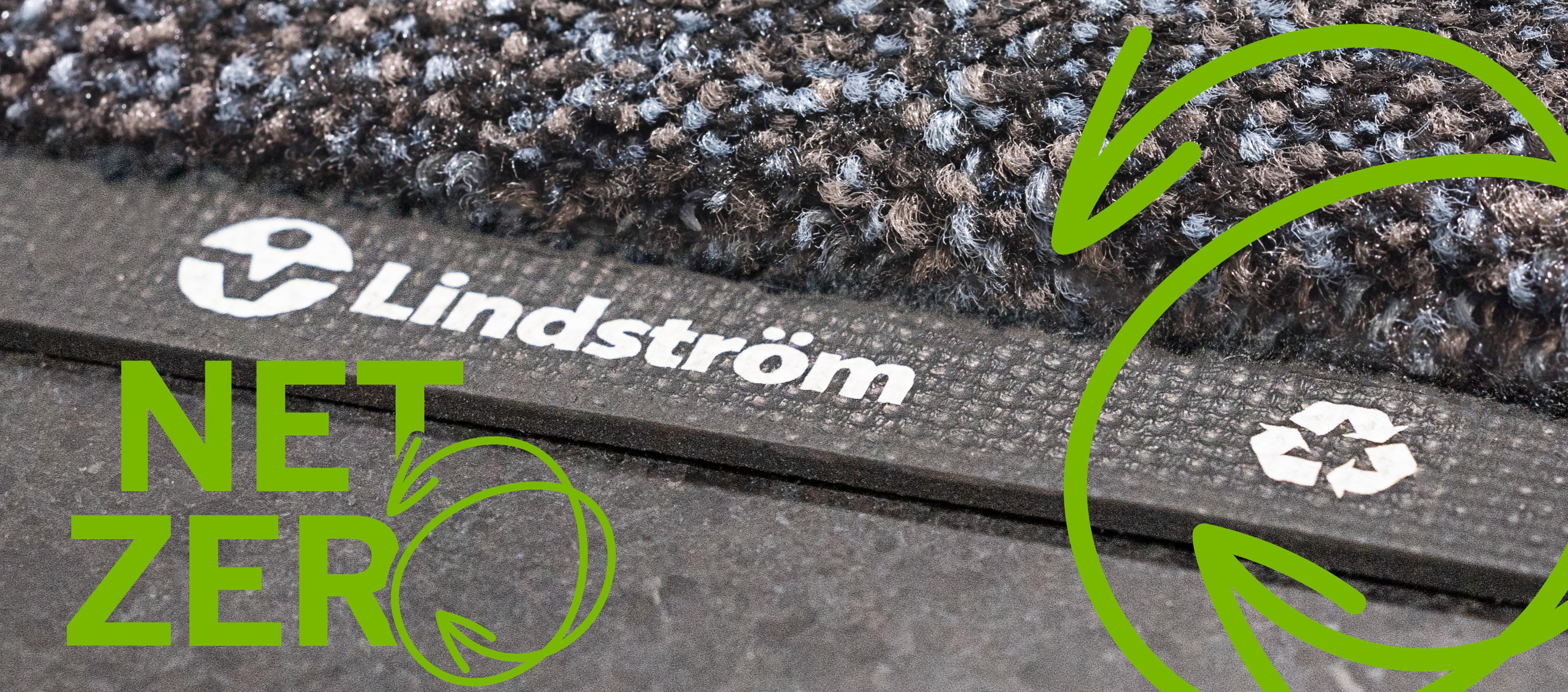
Our standard mats now include recycled fibres and rubber
Lindström’s standard mats collection takes a huge sustainability leap, as all mats will be made with 75% recycled fibre and phthalates-free rubber. The shift is big – and undetectable at the same time.
On the journey towards net-zero, scale matters most. About a quarter of Lindström’s greenhouse gas emissions come from purchased textiles, like the hundreds of thousands of mats on the floors of office buildings, shopping malls, and hotels across the world. Incorporating recycled material into production not only reduces our carbon footprint but also lowers our customers’ environmental impact.
Starting this autumn, all new mats in the standard mat collection will be made with 75% recycled fibres and phthalates-free rubber. The standard mat product quality will remain the same, and the roll-out will last until 2025.
The recycled standard mats collection will complement the design mat collection, which is already made with 100% recycled materials.
Customers will benefit from the more sustainable mat collection in many ways, says Taru Jokinen, Director, Concept Development and Sustainability at Lindström. Using recycled nylon and rubber contributes to waste reduction, resource conservation, and a lower carbon footprint, but that’s not all.
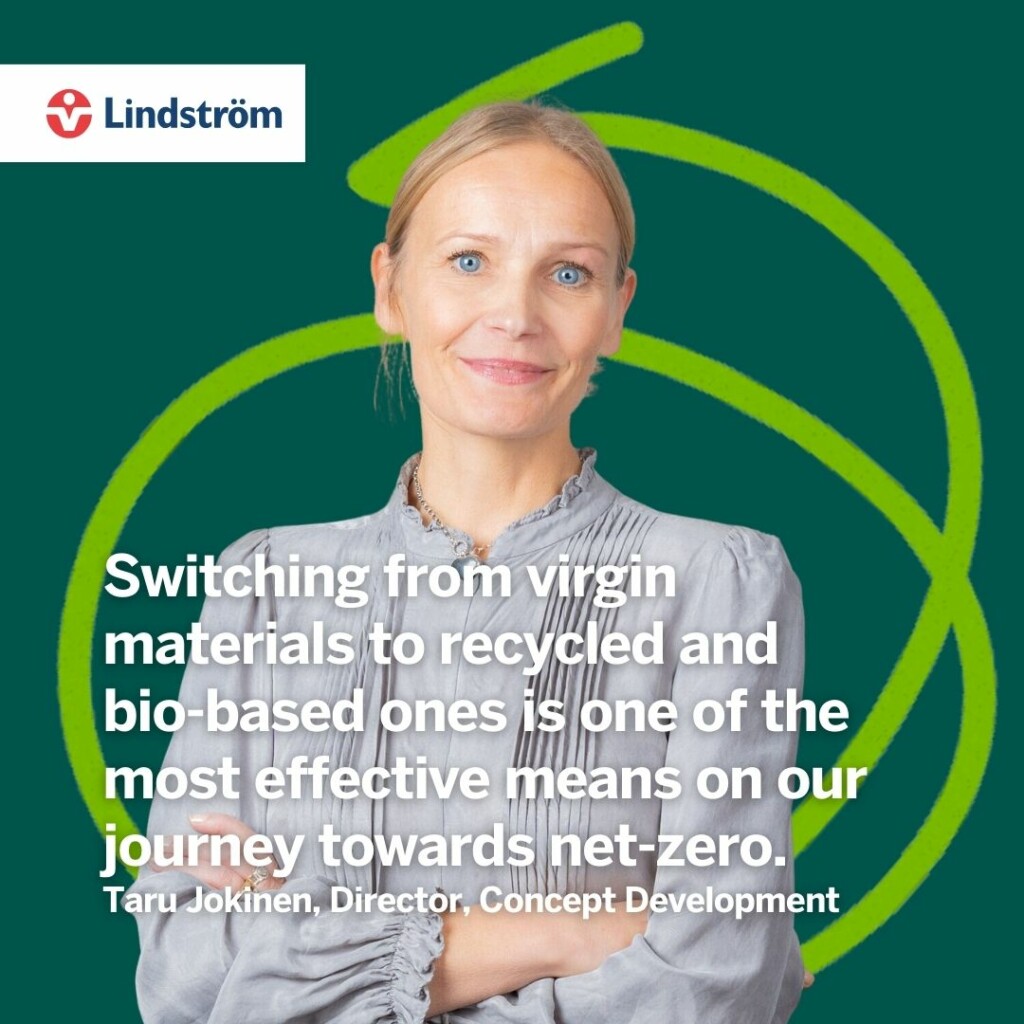
“Durability and hence the lifetime of the products made of recycled materials is often a challenge. But with our Renycle-based mats, including phthalates-free rubber, the durability and quality are the same as with mats made of virgin materials. And last but not least, the collection is still very cost-effective as well.”
Creating sustainable mats is a team effort
Switching to recycled materials has been a true collaborative effort. Our partners in the revamped standard mat collection are RadiciGroup, one of the world’s leading manufacturers of polyamides, synthetic fibres and engineering polymers, and Kleen-Tex, a global mat manufacturer and our long-time partner.
The goal was to find materials and production methods that ensure the products and their quality remain the same, explains Kaspars Grava, Service Owner at Lindström.
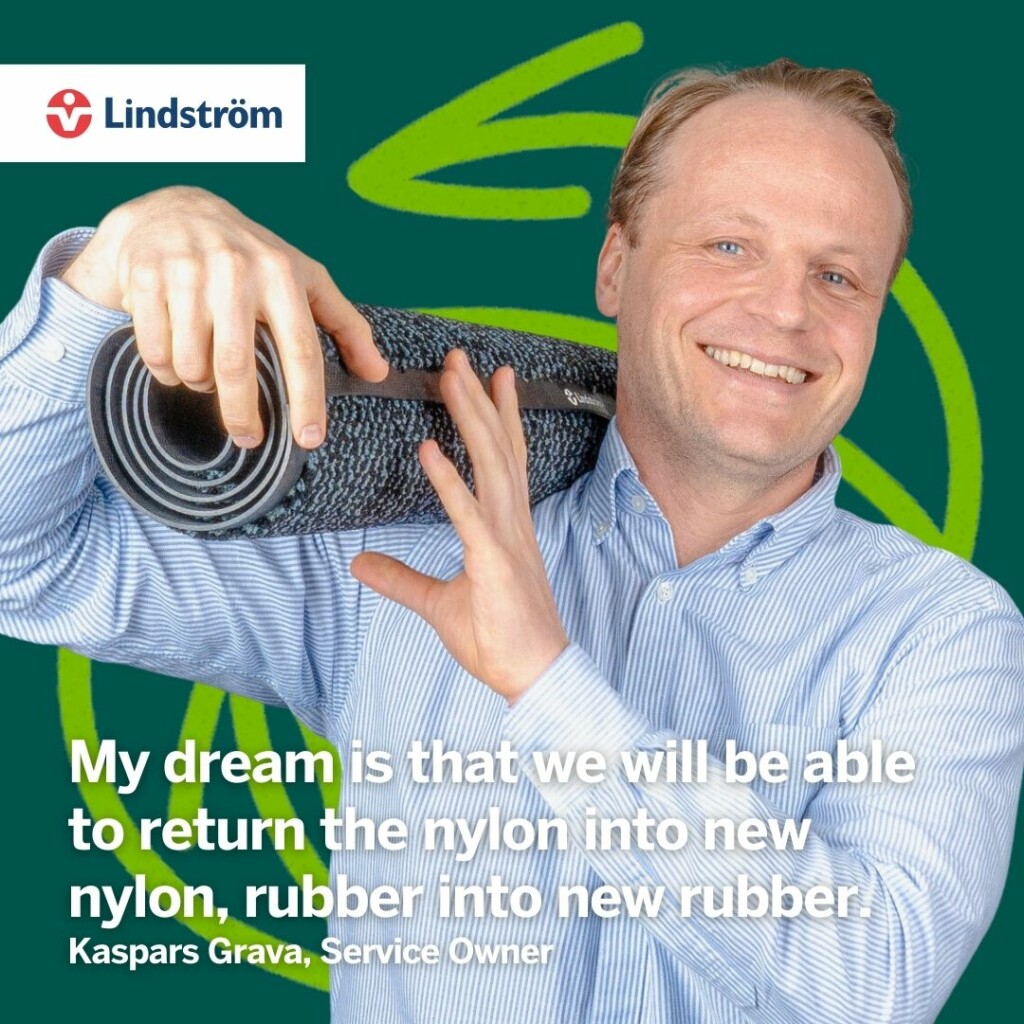
“We were able to change the materials without changing the product. We’re making this change without touching the manufacturing protocols or the service,” he says.
The new yarn is made with Renycle technology that transforms post-industrial nylon waste into high-quality yarn. Mechanical recycling uses less energy than traditional chemical recycling without sacrificing yarn quality, dyeability or durability. The yarn used in the mats is 75% recycled and 25% virgin nylon, which was found to be the most energy-efficient and suitable solution.
Collaboration is key in circular economy and an important driver in transforming the entire value chain, says Giada Angeli, Marketing Product Manager at RadiciGroup, manufacturer of Renycle yarn.
“Our partnership with Lindström and Kleen-Tex is based on knowledge exchange and is challenging innovations in both directions. Working together is a way to optimise supply chains, raise awareness about sustainability, and share common values. This partnership inspires and strengthens our commitment to a more sustainable future.”
Both the yarn and the mats are manufactured in Europe, further reducing the mats’ environmental footprint. The mats are manufactured by Kleen-Tex, who has been making our standard mats since 2003. Comprehensive testing ensured that introducing recycled fibre didn’t lead to changes in performance or appearance, says Elaine Smith, European Marketing Director at Kleen-Tex.
“By working together, and continually testing to ensure the product we bring to market are best in class, we continue to delight our customers. As a business and an industry, it is our duty to ensure that our business models are sustainable.”
Unseen big changes
Sustainability extends beyond the substitution of virgin materials with recycled alternatives. Equally significant are the quality of the new products and the way they are introduced to the market.
For example, opting for recycled materials but sacrificing the life cycle length would mean using more raw materials and energy in the long run, explains Ari Sosunov, Service Director at Lindström.
“We have washed the mats hundreds and hundreds of times, checking the colours and durability. The only place where you can spot the difference between the new and old mats is the little circular icon next to Lindström’s logo on the side of the mat.”
The undetectable change also enables a long roll-out period. The first Renycle mats are now out in the world, but it will take a couple of years until all standard mats are made with recycled materials. There are hundreds of thousands of virgin material mats in circulation, some of them only a couple of months old. Discarding all of them at once would be a terrible waste of resources. Introducing new mats indistinguishable from the old ones is the most sustainable way to make the switch.
“A mat at one customer’s premises today can be elsewhere the next day. It’s a massive benefit that our customers will always get mats that look and perform the same,” Sosunov explains.
Aiming for net-zero
Switching from virgin materials to recycled and bio-based ones is one of the most effective means on Lindström’s journey towards net-zero, says Taru Jokinen. The goal is to reduce greenhouse gas emissions by 50% across the value chain by 2030, ultimately achieving net-zero emissions by 2050.
“We want that by 2025, 30% of all our purchased textiles include recycled or biobased fibres. Introducing the Renycle-based standard mat collection brings us very close to this target.”
Naturally, sustainability efforts in the mats business line won’t stop with recycled fibre. In 2024, also the rubber in the mats will feature recycled content. The next big step will be to enhance end-of-life recycling. Currently, standard mats are reused as industrial mats, burned for energy, or sometimes ground into new materials.
We are currently exploring options that enable the use of the old mats as raw material for the recycled nylon yarn. There are still hurdles to cross, like ensuring that the transportation doesn’t add too much to the environmental load. Still, Kaspars Grava is hopeful that the process will be fully circular in the future.
“We should be working with our own material. My dream is that we will be able to return the nylon into new nylon, rubber into new rubber.”
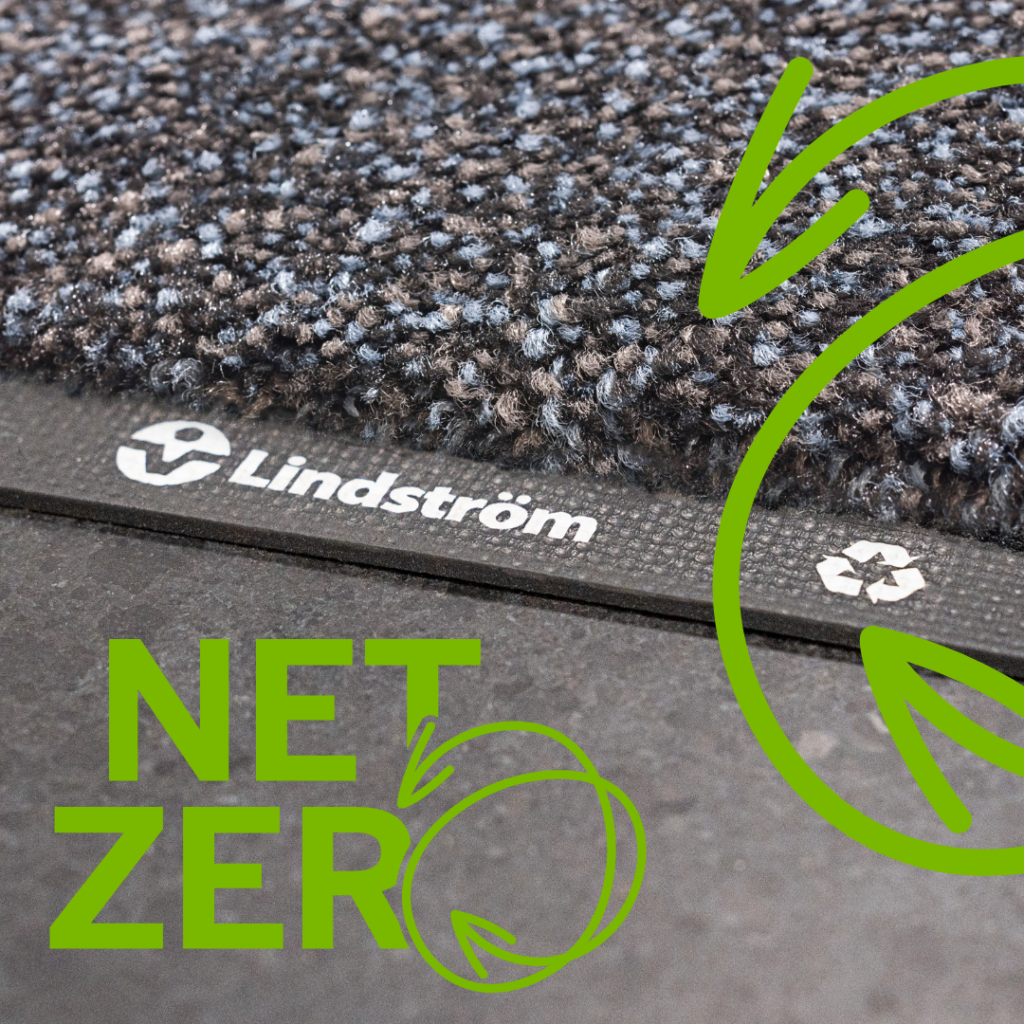