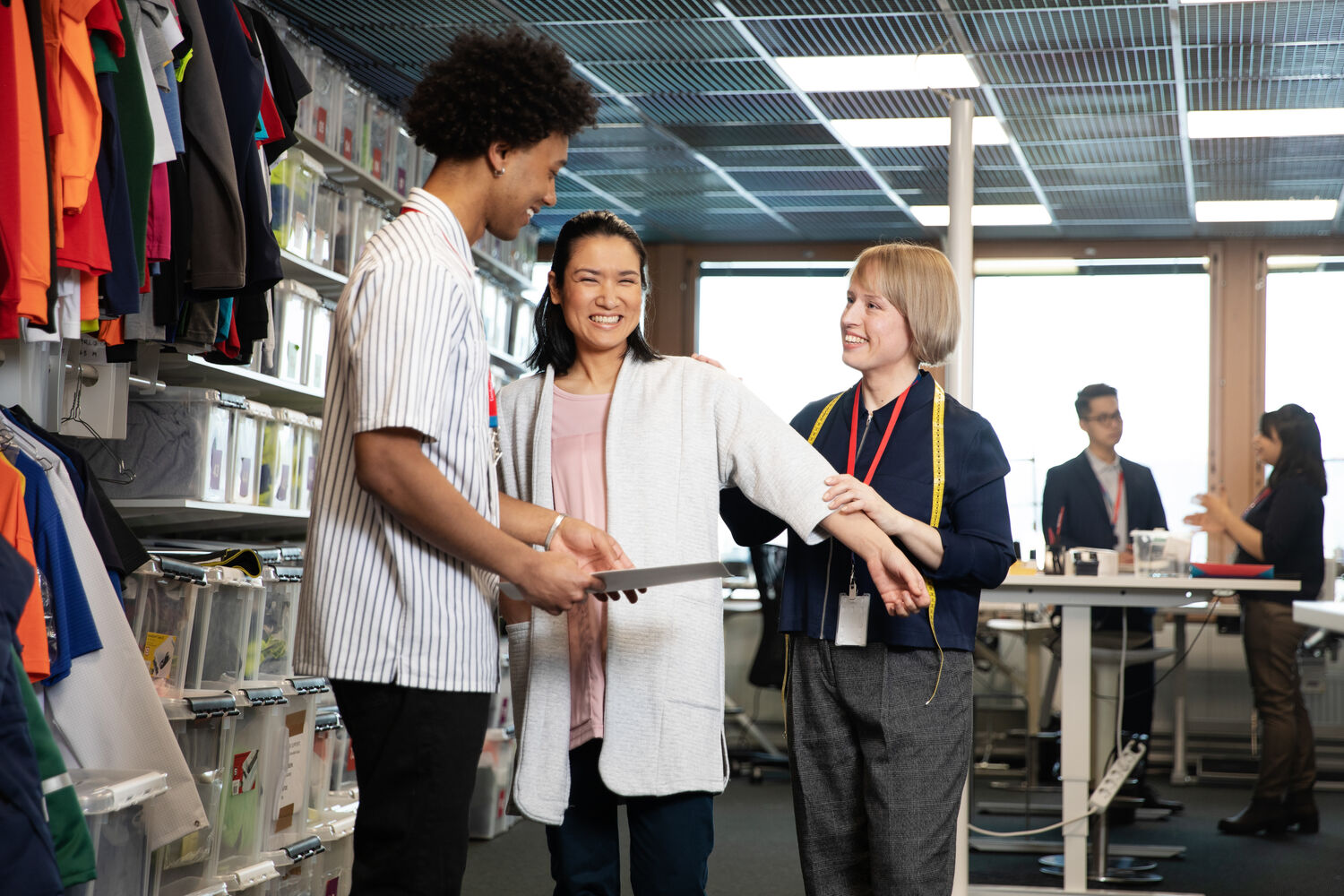
Developing a closed-loop textile recycling process
The textile industry is one of the major contributors to the environmental problems in achieving sustainability targets. This is due to the overall growth of textile fibre consumption in several industrial areas, overproduction and a very short lifespan. Our industry generates 6-10% of global carbon emissions.
One of the answers to the challenges that our industry is facing could be in a circular approach to the business with a closed-loop recycling process. This means that when the textile comes to the end of its lifetime, it could be recycled as a new fibre that is used as raw material to produce fabric.
Collaboration is the key to the change
Together with our customers, partners and suppliers, we are developing a closed-loop recycling process. “When working towards a more sustainable future, active collaboration with our partners and customers is crucial. No company can change the world alone,” our CEO Juha Laurio recognizes.
One of those partners is Rester, a key player in the end-of-life textile industry. It specialises in recycling business textiles and making them into a new textile fibre and quality raw material. As the founder, Outi Luukko, explains: “The change in the textile industry needs to be considered from a holistic point of view. It requires a lot of work and many parties, including the whole value chain.”
Klopman, a world-leading fabric manufacturer, is an important part of that value chain. They spin, weave and dye the fabrics made from recycled fibres. Once the materials are reproduced, they will be given to the garment makers to put them on the path to their new life.
Amaury Sartorius, managing director at Klopman, highlights the importance of the process as 80%-85% of clothes in Europe today are burned or dumped. “One of the most important undertakings for the future is to move from a linear model to a circular approach to business,” he summarises.
Effective way to reduce waste and use natural resources
Looking toward the future, this circular approach to business is the most efficient way to optimise production while using the least amount of resources. Anna-Kaisa Huttunen, former Senior Vice President at Lindström, explains, “When we recycle textile waste as new fibre and then use it for the production of new textiles, it significantly reduces the amount of waste. At the same time, it also impacts the very beginning of the process. The more recyclable fibres are used in textile production, the less demand there is for cotton, which could free up natural resources like land and water for future needs.”
Huttunen is very optimistic about the system of closed-loop-recycling, “I really think that the benefits of recycling textile fibres will pay off in the future.”
Check out the video on how we collaborate with our customers and partners for a more sustainable future:
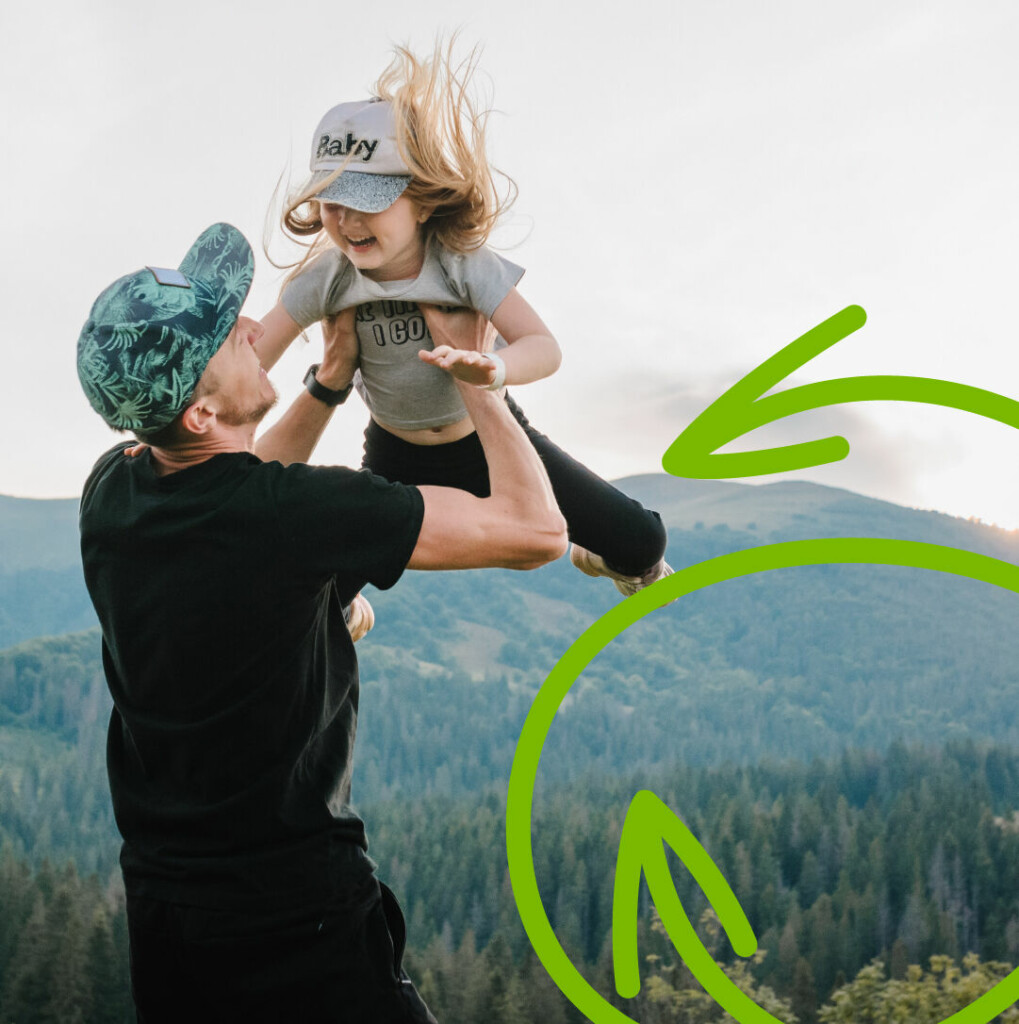