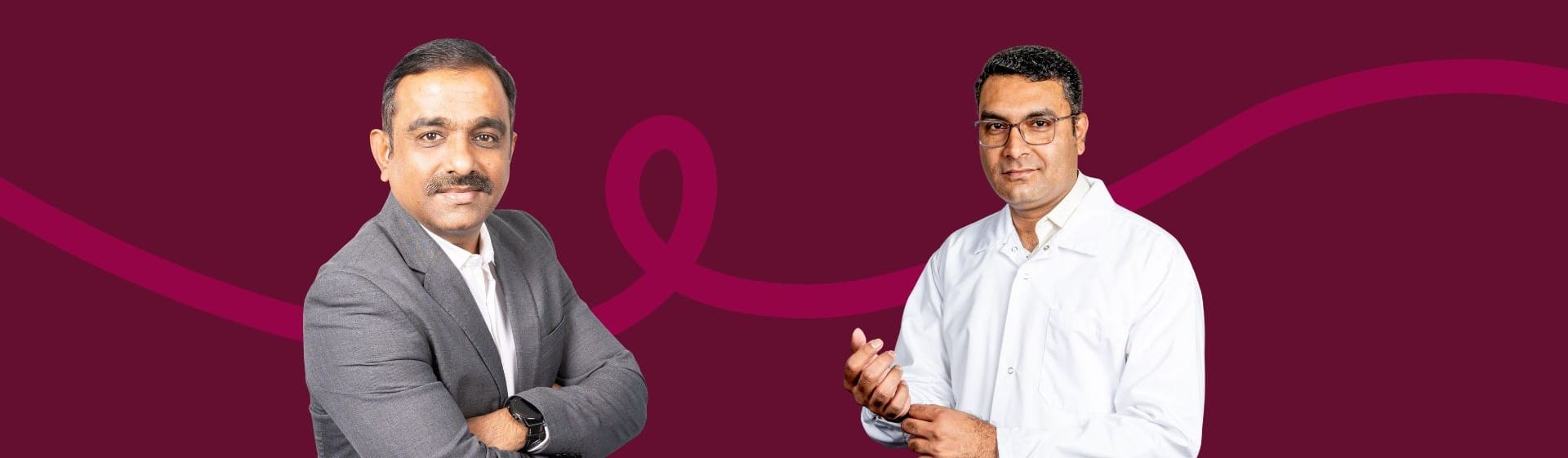
Cleanroom fabrics and design for enhanced protection
Ensuring contamination control in pharmaceutical cleanrooms requires more than just compliance with regulations – it demands a deep understanding of cleanroom fabrics, garment design, testing practices, and proper maintenance practices.
Companies may face challenges in navigating the complexities of cleanroom fabrics and design; their primary expertise lies in pharmaceutical manufacturing and biotechnology rather than fabric selection and regulatory specifics – especially since pharmaceutical cleanroom garment standards were borrowed from other industries, such as electronics.
Ensuring the right combination of fabric properties, filtration efficiency, testing procedures, and proper laundry practices require specialized knowledge. These factors, along with proper testing and laundry procedures, determine whether a garment will meet cleanroom standards while remaining practical for frequent use.
To help customers navigate these challenges and make informed choices, our experts – Service Owner Swapnil Pawar and Global Director of Pharma Manas Kumar – provide guidance in this article on selecting the right fabrics and garment systems for each manufacturing zone and industry standard. While guidelines may only mention the need for “appropriate” garments, Lindström helps define what appropriate means by aligning garment choices with ISO and GMP standards and cleanroom classifications, ensuring compliance and optimal performance.
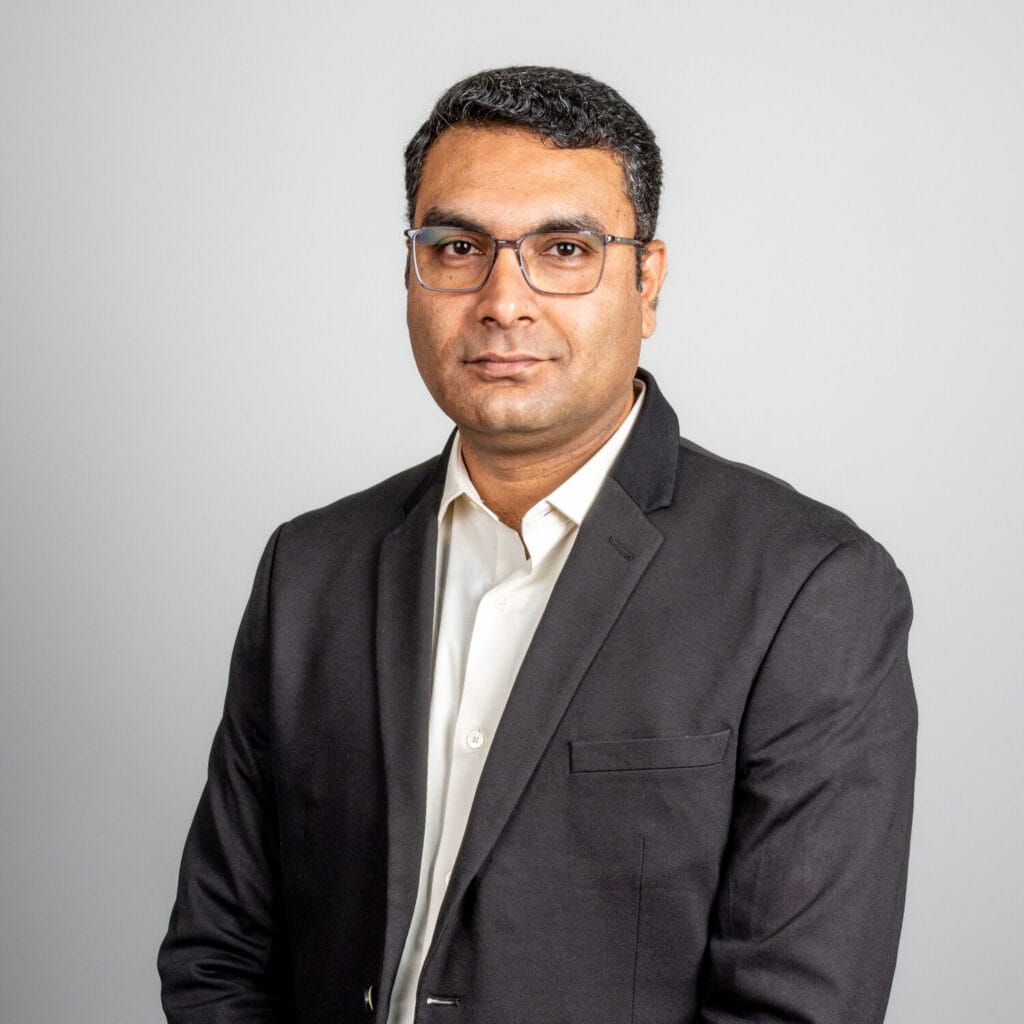
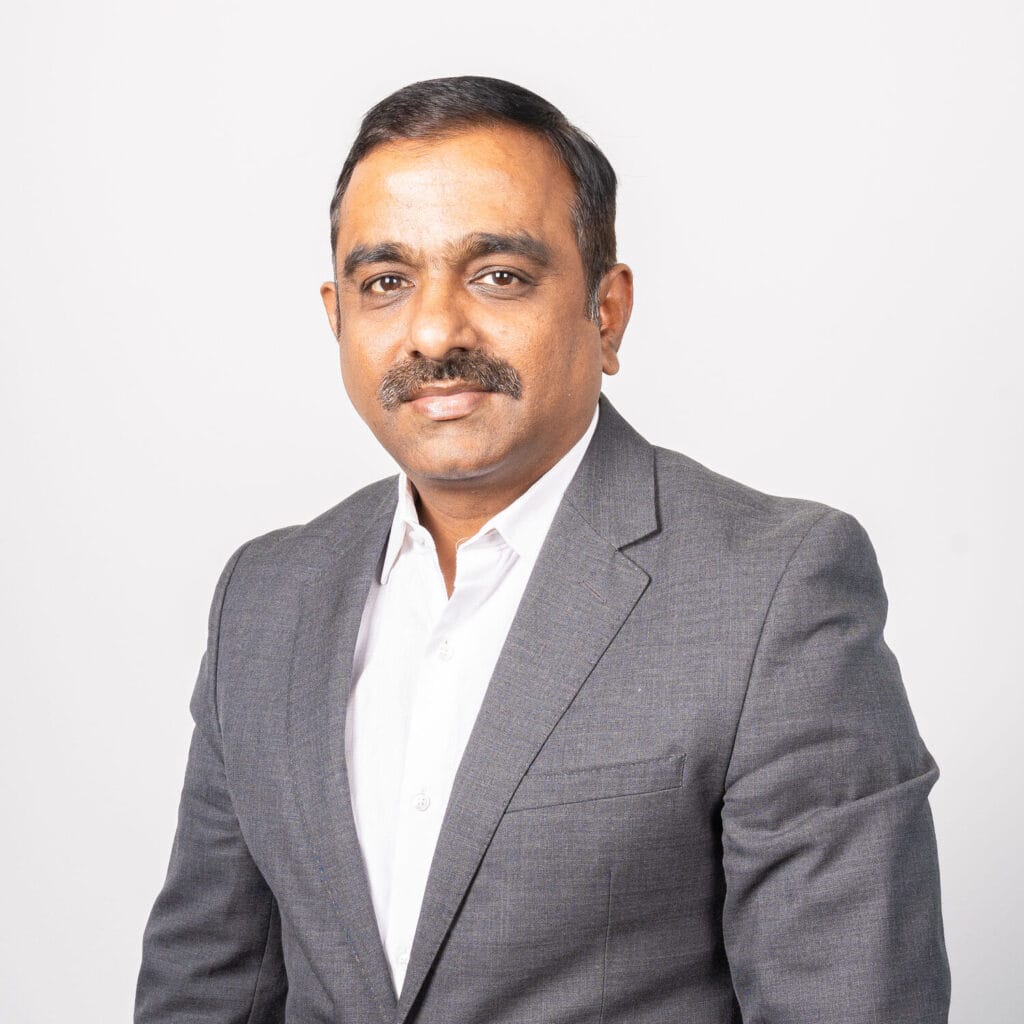
Different solutions for different areas
Different manufacturing areas pose varying contamination risks, and a ‘one-size-fits-all’ approach does not work in cleanrooms. Garments must align with the manufacturing areas’ classification, process risks, and industry standards, e.g., ISO 14644, EU GMP Annex 1, & IEST recommendations.
Swapnil Pawar, Service Owner at Lindström.
Choosing garments that are over-engineered or inadequate for a specific cleanroom environment or materials with inappropriate filtration efficiency can lead to poor comfort and durability, which can compromise both product quality and process efficiency. Ill-fitting or uncomfortable garments may also increase the risk of human error during critical operations.
The required fabric, garment designs and garment properties vary based on the cleanroom classification (GMP Grades A, B, C, and D, where Grade A represents the most critical environment and Grade D the least). In higher-grade zones (e.g., A/B), fabrics must withstand sterilization methods (e.g. autoclaving or gamma irradiation) as Annex 1 recommends that garments must be sterilized before use. Using non-compatible materials such as those prone to fiber shedding can introduce contaminants into sterile environments, leading to contamination risks. In less critical areas sterilization is typically unnecessary, but garments must retain durability through repeated cleaning and have low-linting properties.
Choosing the incompatible cleanroom garment can lead to non-compliance, production deviations, and failed audits – all of which carry significant costs. Lindström helps ensure that the cleanroom garments meet the standards and regulatory requirements, minimizing such risks while maintaining both compliance and operational efficiency.
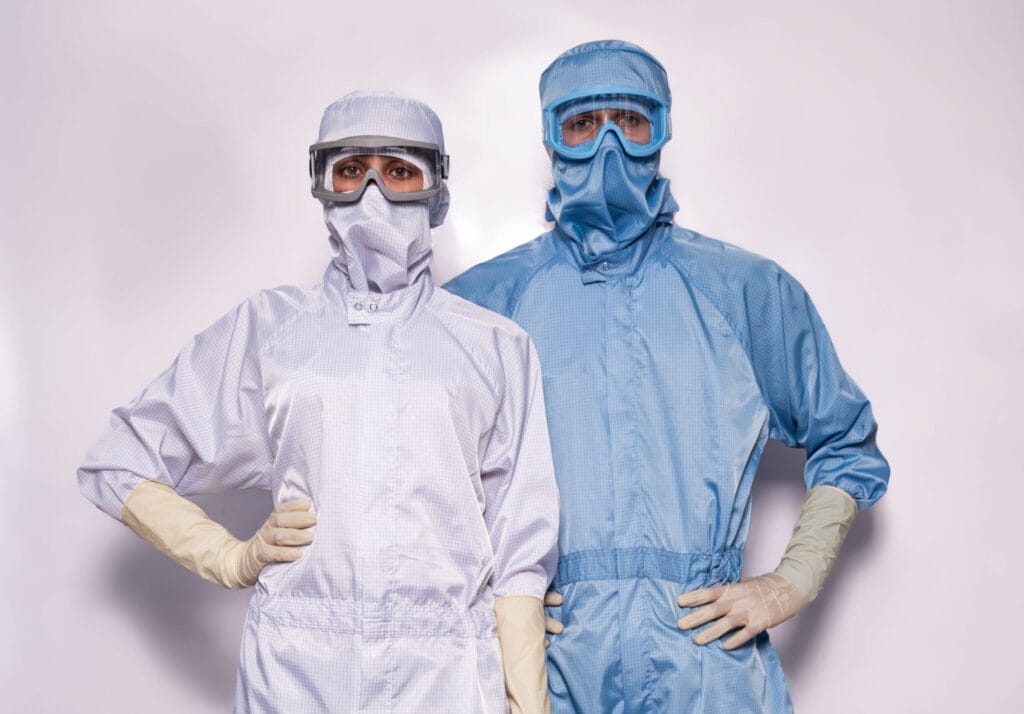
Innovations help streamline processes
One of the latest advancements in cleanroom garment technology is the introduction of specialized undergarments to replace traditional dust-free fabric coveralls or separate shirt and trouser sets. Made from polyester and carbon fiber, these undergarments enhance the filtration performance of outer garments, reducing contamination risks while improving user comfort.
Previously, cleanroom workers had to wear both a primary and a secondary coverall, but now, these cleanroom-compatible undergarments can replace the primary layer. This shift improves user comfort while maintaining cleanroom compliance and protection. “We haven’t limited our offering for only the garments”, Swapnil Pawar points out.
Lindström offers a comprehensive solution for cleanroom needs, going beyond garments to include cleanroom goggles and mops – cleanrooms also need to be cleaned! These additional products help maintain hygiene and compliance in critical areas while reducing the burden on clients who might otherwise need multiple suppliers, thus simplifying operations for clients.
Designing for durability and sustainability
A lot of practices in the pharmaceutical industry use the disposable products, making them a very polluting industry. Most industries are looking to become more sustainable in their operations.
Manas Kumar, Global Director of Pharma at Lindström.
Cleanroom garment design plays a key role in sustainability. Lindström incorporates durability into garment development to extend lifecycle usability. A well-designed garment that lasts 80 cycles instead of 50 significantly reduces environmental impact by minimizing waste from disposable materials. Additionally, by upcycling materials and optimizing garment lifespan, Lindström helps clients achieve a balance between compliance, cost-efficiency, and sustainability.
By providing expert guidance on fabric selection, regulatory compliance, and complete cleanroom solutions, Lindström ensures that clients make the right choices, minimizing risks and maintaining high standards in manufacturing environments.
Key takeaways
The design of cleanroom garments follows established guidelines to ensure quality by design. These standards are followed to ensure the garment meets the intended contamination control requirements before being introduced to the market. The performance of the final garment depends on fabric selection, pattern design, and construction, all carefully considered at an early stage during the development.
Lindström’s expertise in cleanroom fabrics and design is built on industry knowledge, regulatory alignment, and innovative solutions. We bridge the knowledge gap for customers, who may lack a deeper understanding of the standards governing cleanroom garments.
With a deep understanding of industry-specific guidelines, Lindström ensures that cleanroom garments are not just compliant but optimized for real-world manufacturing needs. By continuously innovating and providing expert insights, Lindström helps customers stay ahead of regulatory changes and contamination control challenges, making cleanroom management smoother, safer, and more efficient.
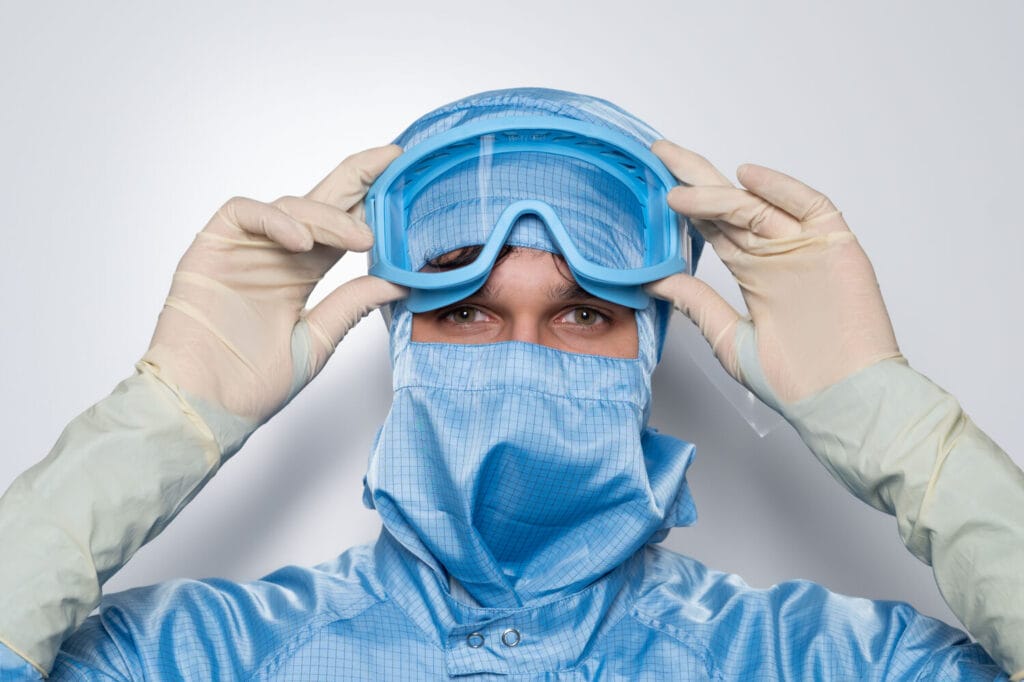