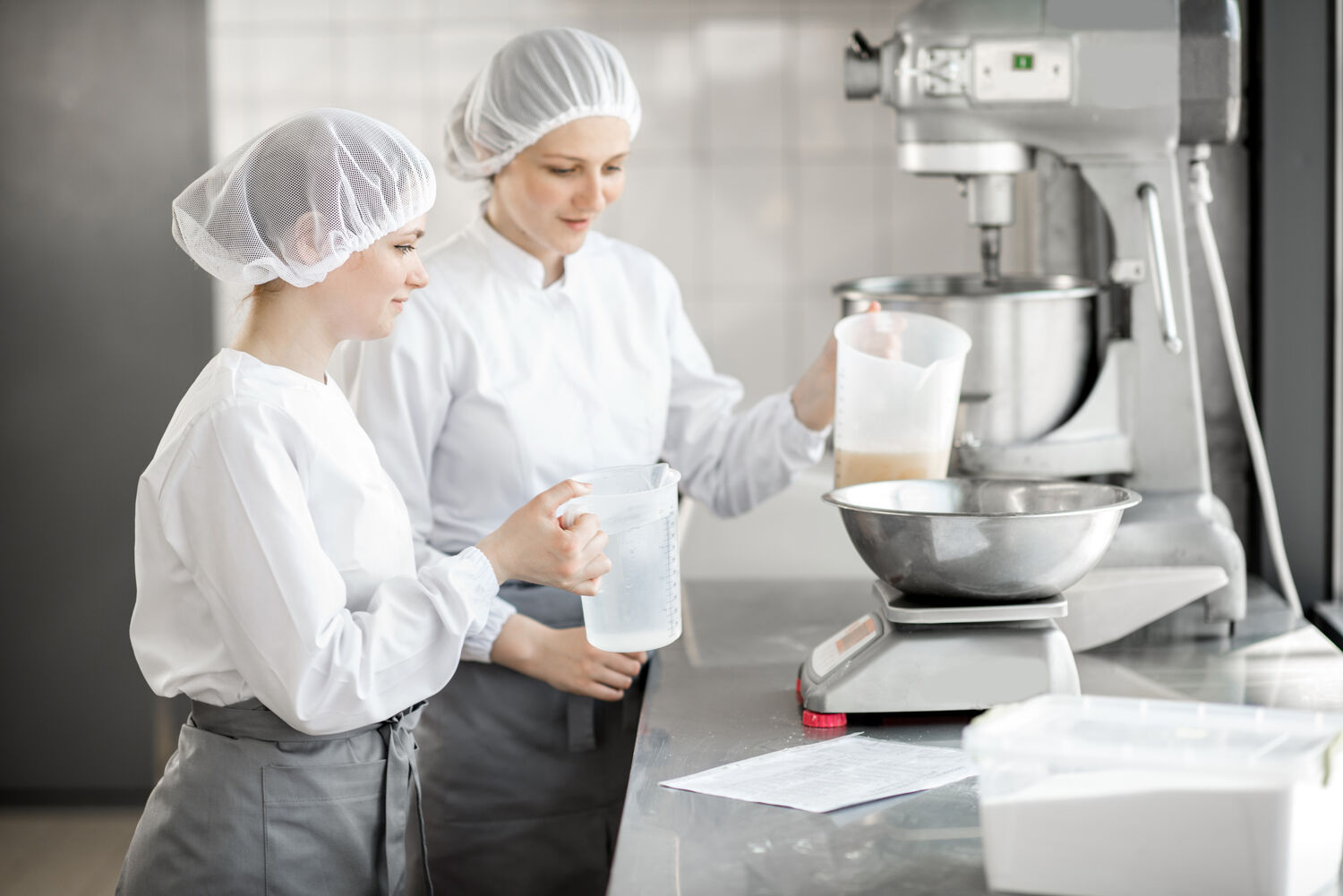
Nestlé use workwear as part of responsible operations
Lindström and Nestlé have been partners for more than 25 years, crafting the stylish Nestlé workwear. We actively promote responsibility together. Healthy food, people and the planet are at the heart of the responsible work of Nestlé, the world’s largest food company.
“At Nestlé, we have defined three commitments for our operations: ‘Individuals & families’, ‘Communities’ and ‘Planet’. These commitments guide all our operations and responsibility work daily at the global level. We have a great responsibility and that is why it is great to have partners like Lindström. They help us operate in a more sustainable way”, notes Sari Miettinen-Rantala, Factory Manager at Nestlé Turku.
Lindström and Nestlé have been partners for over 25 years. At the Turku baby food factory, 130 employees wear Lindström’s workwear every day. The improvement work of the workwear collection, which was completed in the spring of 2021, brought the companies even closer to each other. “Workwear is an essential part of our responsible operations, so cooperation with Lindström is close to our hearts. We cannot act alone, but instead we work together for more responsible business,” shares Miettinen-Rantala.
Nestlé contributes to better well-being at work with sustainable workwear
At Nestlé, employees are considered the company’s most important stakeholder. Promoting decent jobs is one of Nestlé’s most important responsibility goals by 2030. This means speaking out for jobs that are beneficial for health, among other things. “As the world’s largest food company, we have a great responsibility for our personnel and their quality of life. We want to have an impact on the quality of people’s lives with good and healthy food. Quality of life also refers to how we succeed in creating decent jobs that are beneficial for health. When our employees spend eight hours a day in our factory. Supportive workwear, footwear and working conditions become extremely important,” explains Miettinen-Rantala.
As a responsible employer, appreciating, hearing and involving the employees is important for Nestlé and part of their official Code of Conduct. We involved employees in the design process of the new workwear collection. “Designing the workwear was an incredible journey for us. We made that journey together with our employees and Lindström. The idea to renew the collection came from Lindström. We started planning the workwear collection first with a smaller pilot project which we later expanded. During the design process, our employees got a say in the colours and models of the garments, among other things. Finally, we voted on the workwear and democratically chose the garments that got the most votes.
Now we have workwear that truly represents our employees. I am very happy about that”, Miettinen-Rantala says. “The raw materials supply chain is important to us in all respects since we want to produce baby food responsibly. In a way, workwear is a raw material for us, because without clean, safe and hygienic workwear, it would be impossible for us to work in the factory”.
Workwear made from wood raw material is a concrete environmental act
Nestlé’s goal is that its business operations will not have an environmental impact by 2030. The company wants to demonstrate leadership by combating climate change, among other things. “As a big company, environmental issues are really important and meaningful to us. We help the environment by carrying out both small and big actions every day. With all our environmental commitments in mind, we were very happy when Lindström gave us the idea to switch to TENCEL Lyocell fabric, which is made of renewable wood raw material. The fabric is also the product of responsible forestry,” Miettinen-Rantala explains.
“The idea to renew our workwear collection came from the fact that our factory is terribly hot in the summer. We started thinking about how we could improve the working conditions for our employees. Cooling a big factory is very expensive. So the idea to make breathable workwear from wood raw material was brilliant from this point of view as well. I am incredibly proud of our workwear,” says Miettinen-Rantala.
Natural fibres are biodegradable and after their life cycle they end up back in the natural cycle. Fibre production takes place in a closed-cycle process, in which cellulose fibres are produced from wood pulp in an energy-efficient and environmentally friendly manner. The production process consumes less water and energy than the production of cotton, which was considered important for Nestlé’s responsibility goals.
“Our goal is that all our operations will be carbon-neutral globally by 2050. As part of this goal, we are developing regenerative farming and actively looking for ways to reduce water use globally. Cotton farming uses an awful lot of water. Also in that sense, it is great that Lindström provides our workwear made of raw wood material. The workwear is part of our raw material chain and for that reason, it is excellent that we are also saving the world’s water resources for clothing,” notes Miettinen-Rantala.
“In this workwear project, we accomplished many goals. Together with Lindström, we have again carried out concrete responsible actions. We got absolutely lovely, stretchy and breathable clothing for our employees. Garments made from raw wood material support our environmental goals. We also ordered eco-nylon mats from Lindström. They are produced entirely from recycled material, such as fishing nets and industrial waste.”
Cost-effectiveness on the conditions of sustainability
Employees have been particularly pleased that the new workwear at Nestlé is unisex, which means that both men and women wear the same shared clothing and therefore personal clothing is no longer needed. “Cost-efficiency is always really important to us. By moving from personal clothing to shared unisex clothing, we were able to significantly reduce the amount of workwear in circulation, which of course reduced our workwear costs. When there is just the right amount of clothing in circulation, the carbon footprint is smaller than the one that personal clothing would have created, which is great from the point of view of environmental responsibility,” says Miettinen-Rantala.
“At this point, however, I want to emphasise that while cost-effectiveness is really important to us, the clothing itself was much more expensive than cotton clothing would have been. In other words, when it comes to environmental issues and the well-being of our employees, money is not the most important factor. The well-being of our employees is extremely important.”
Recycling as part of Nestlé’s climate commitment
Compared to Nestlé’s other 412 factories in 85 countries, the Turku baby food factory is very advanced in environmental matters. No landfill waste is generated at the factory, as all material can be recycled or reused. Overall, 99% of the packaging materials are recyclable, and recycled material has also been used in the manufacture of all packaging materials. For this reason, Miettinen-Rantala is pleased that Nestlé and Lindström share a passion for recycling.
“At our Turku factory, all our raw materials, such as glass and label materials, are more than 99% recyclable. Recycling is part of our climate commitment. It is great that our workwear will eventually be recycled responsibly by Lindström,” asserts Miettinen-Rantala.
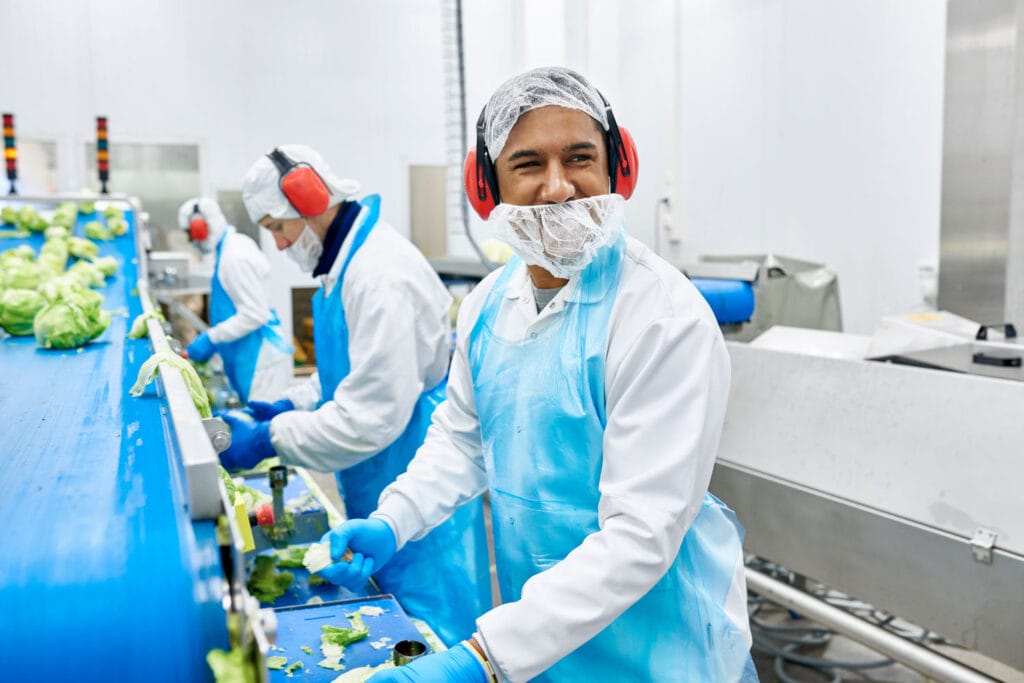