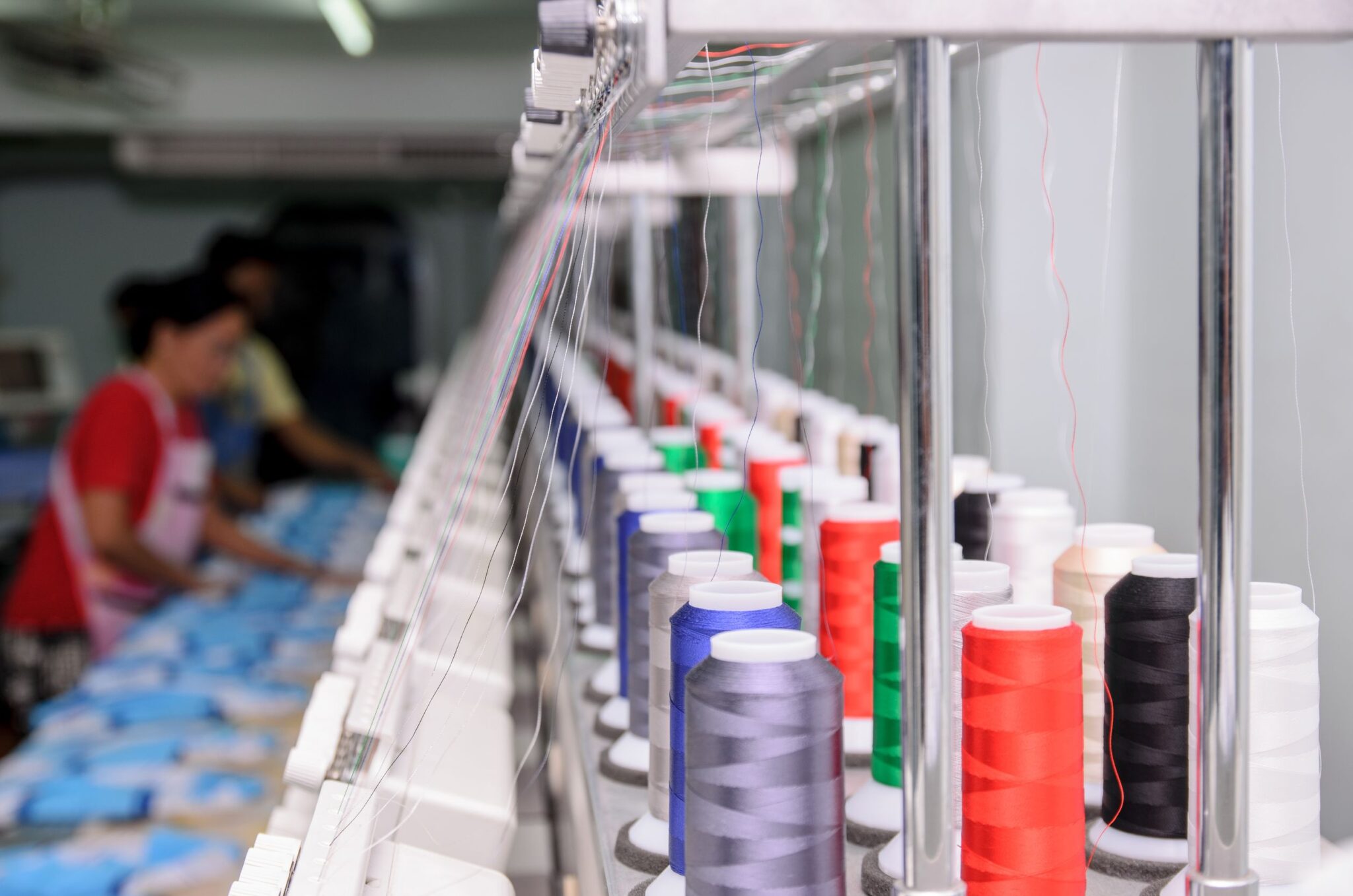
Behind the scenes of our supplier auditing process
Our regular supplier auditing process play a key role in guiding our suppliers towards improved sustainability, social responsibility, and workplace safety. These audits ensure our suppliers align with our ethical principles. They help us reach our goal of net-zero emissions by 2050 across our value chain.
In this article, Lindström’s Director for Sustainable Procurement, Kristiina Tiilikainen, shares more about the auditing process. Why do we conduct audits, what the process entails, and how audits benefit our suppliers, customers, and our organisation?
“Regulations are getting stricter and we at Lindström also have very ambitious sustainability targets. Having joined the Science Based Targets Initiative (SBTi), it’s important that we have sustainable suppliers. That will help us reach our net-zero target,” says Kristiina.
Why we conduct supplier audits?
Lindström is a fair and responsible employer. We require all our suppliers and partners to adhere to the same principles we follow. They are as laid out in our Code of Conduct.
To ensure our suppliers align with our ethical principles and to build strong supplier relationships, Lindström’s procurement teams conduct audits for all large suppliers before entering into a new cooperation. We also audit our largest and most critical suppliers every three years. On average, we conduct over 20 supplier audits a year.
Without our suppliers, offering sustainable solutions to customers across various industries wouldn’t be possible. Kristiina explains: “We want to have responsible, reliable, and sustainable partners. So we need to make sure that they follow international regulations and rules. These are regarding social responsibility, environmental responsibility, health, and employee wellbeing.”
In addition to these comprehensive audits, we carry out annual supplier evaluations. If a supplier’s total score falls below the standard in an audit or evaluation, we work collaboratively on a development plan to improve their performance.
A glimpse into the supplier auditing process
Kristiina walks us through a typical supplier auditing process at Lindström.
Step 1 – sending an audit document
We send an audit document to the supplier at least two weeks before the audit. We give them time to go through the questions and gather responses. The questions can’t be answered by one person alone — individuals from HR, quality departments, production, and management need to be involved.
The audit document addresses topics including:
- Quality system
- Environment
- Security and risk management
- Occupational health and safety
- Social responsibility and employment practices
- Product data and certification
- Order and production process
- Production and claim process
- Quality control
- Storing
- Deliveries and invoices
Our questions are tailored to the specific type of supplier we are auditing. While some aspects, like social responsibility issues, are universal, the details vary based on the supplier’s production facility. For instance, auditing pollution levels might not be pertinent for a sewing facility, but for a fabric manufacturer, we delve into how they manage chemicals and handle wastewater.
Step 2 – visiting the production site
When we audit our main suppliers, we make it a point to personally visit their production site. During these visits, we review the audit document together with the management team. We also ask any follow-up questions we may have.
Kristiina sees these audits as a chance to share information about what we do at Lindström to promote fair and sustainable practices, giving our suppliers inspiration. She explains: “During these audits, we don’t give our suppliers the third degree — it’s more of a discussion.
I use these audits as a benchmarking opportunity. We have important suppliers smaller in size than Lindström. They don’t necessarily have time to think about all the policies or practices they could have. People are really listening and paying attention during these audits. You see their eyes start to sparkle when they get excited about something new they could start doing.”
Step 3 – verifying the information
Following the discussion, we walk through the production units to verify the accuracy of the information they have shared. For example, if they said that safety instructions are always next to the machines, we check whether that is really the case.
During these walkthroughs, we check all aspects of production. We address any health and safety concerns. For instance, ensuring the availability of first-aid kits, unobstructed exits, and access to drinking water for employees.
Step 4 – putting together development proposals
After visiting our supplier, we consolidate the audit findings and put together development proposals. We invite our supplier to review their results and monitor their progress through a user-friendly software platform. This ensures transparency and makes it easy to track improvements.
“A common factor with these audits is realising that you can always do better. This is partly related to changing regulations. Especially if you have a new type of supplier, you notice new things worth paying attention to. Audits are not just about developing our suppliers, but also about developing our own auditing process,” says Kristiina.
How does a supplier auditing process benefit our customers?
Supplier audits benefit our customers in several ways. By auditing our suppliers’ processes, we can guarantee a properly working supply chain. We can ensure our customers get the right products at the right time. Auditing our suppliers’ environmental impact contributes to ongoing improvements, aligning with our commitment to sustainability and supporting our customers in their own sustainability goals.
Auditing social responsibility aspects gives customers assurance that the products they receive are produced by people who are paid fairly, don’t work overtime, are not under forced labour conditions, and work in safe environments.
“When we talk about the supply chain, we can’t forget about social responsibility. You have to make sure that the irresponsible people in this world who do things unethically are not in your supply chain. You can’t doze off and think that there are no problems in the European Union. Because there have been many cases of forced labour in Europe. You have to stay alert and develop practices to fight against unethical behaviours,” emphasises Kristiina.
The supplier auditing process ties into our overall ethical practices
Since we only conduct supplier audits every three years, we recognise that they alone can not ensure our suppliers stay responsible and sustainable. Still, these audits play a crucial role in our ethical practices and help us progress towards our sustainability goals.
“We put a lot of resources into developing our supplier audits. We understand how important they are to develop our supply chain,” says Kristiina.
By staying up to date on our suppliers’ practices, processes, and ways of working, we ensure we operate to the highest standards in everything we do.
Learn more about our sustainability work and our net-zero goal, which are at the heart of everything we do.
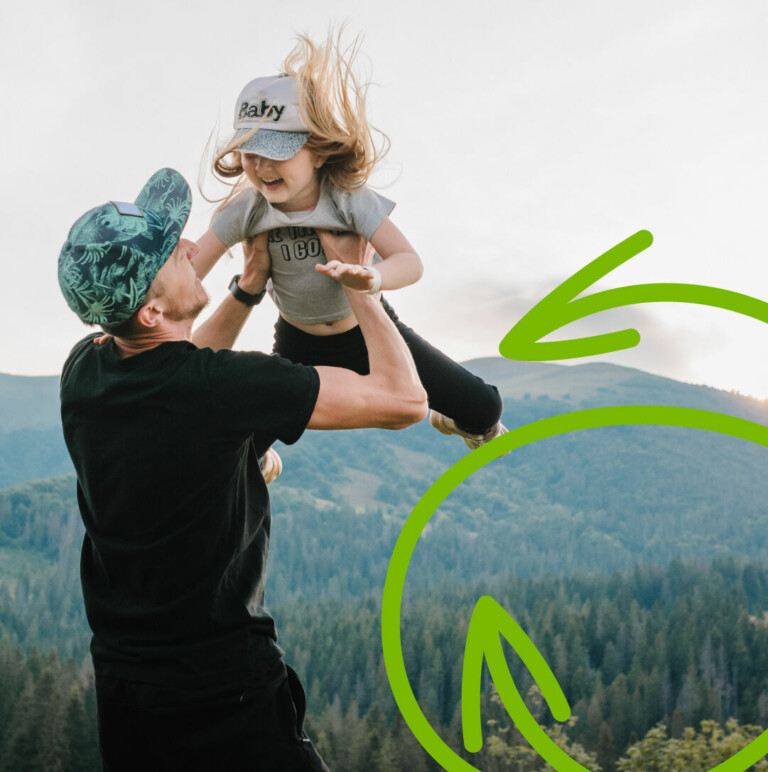