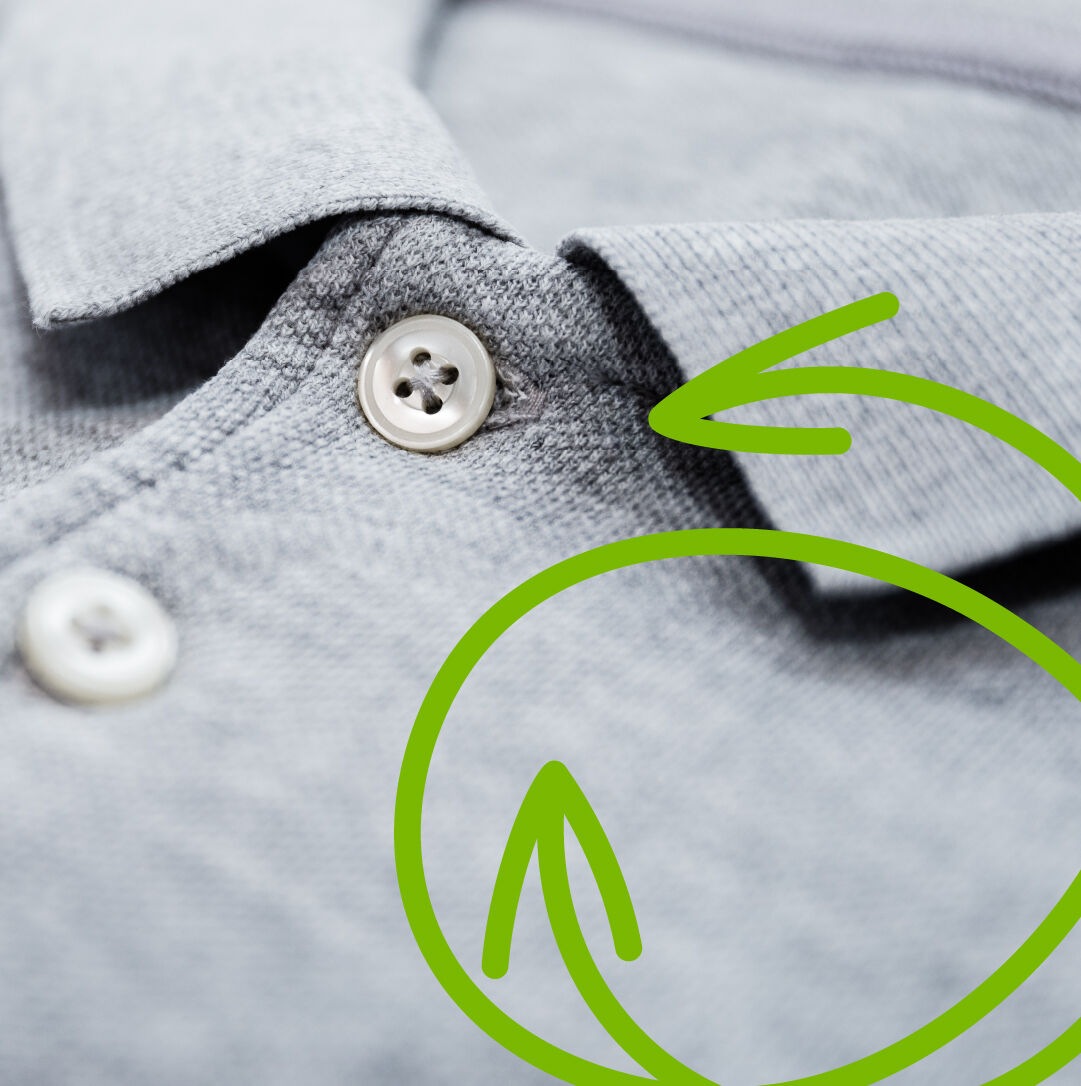
Passionate people forging our way toward net-zero
In this article, we spotlight Seija Forss and how, in her role as Material Manager, she is helping our efforts to reach net zero via the transformation of material sourcing. Forss has a pivotal role in bringing in more recycled and biobased materials into our production processes. With a long-standing passion for sustainability and analysis, she has been at the forefront of data collection and reporting for our organisation’s sustainability initiative.
“I guess you could say I’ve been connected with sustainability for most of my time here. From my early days at the company, assessing the environmental impact of our laundry processes, to leading on the SBTi emissions targets, to the responsibility I now have to consider the big picture as material manager,” explains Forss.
You can’t move forward until you know where you begin
We can’t achieve an ambitious goal without knowing where we begin, which is why data collection is so critical. In 2022, calculations began for purchases of recycled and biobased material, which totalled 10.4% for the entire group. However, for workwear material, this was only 0.31% recycled fabrics and 1.85% bio-based fibres – some way off the target of 30% for 2025.
The good news is that targets will likely be achieved due to progress made with mats and cotton towel rolls alone. Forss states that “for us, sustainability and reaching these goals is such an important issue, we were prepared to make these commitments despite not knowing our starting point.” Forss is proud of the efforts we have made in data collecting and calculations from laundry processes but from a material point of view, there is still a lot of work to do.
It’s important to recognise that in the textile industry generally, there is a lack of both knowledge on CO2 emissions as well as availability of data. Inputs we make in increasing the amount of recycled or biobased materials are not yet visible in our CO2 emissions, as different materials do not yet have their own emissions estimates and our current emissions reporting only calculates textile emissions on a general basis.
The challenge of change and maintaining durability
Another big challenge is in maintaining durability – a core advantage of our product range. As durability is something we are unwilling to compromise on, Forss needs to consider this in sourcing. “Our workwear and other products like bedsheets and towels for the hotel sector must be able to withstand the rigours of industrial washing and tumble-drying,” highlights Forss. A fine balance is needed between the introduction of recycled or biobased fibres and ensuring the garments still meet expectations.
Forss also points to the increased use of recycled polyester such as in the new HoReCa collection. “This is quite a safe option as we see it working in the same way as virgin polyester, meaning we do not lose the long life cycle of garments.” Recycled polyester is a great option for workwear as it offers the durability required. In the HoReCa collection, we used a 50/50 blend of recycled polyester together with the biobased fibre Lyocell, of which 30% was made from recycled cotton.
Forss is quick to play down this potential, however, saying that “we’re not at the stage where we can make garments fit for purpose with high levels of either biobased or textile to textile recycled fabric. However, it’s important to start somewhere.”
Blended fabrics and polyester fibres are more environmentally friendly as they need less water and energy in the washing and finishing stages. Even an organic variety of cotton is highly resource-intensive so recycled polyester blends represent a more sustainable option whilst also providing durability and better colour-fastness properties.
Meeting customer needs on quality and price
We have always been able to provide customers with high-quality products and we are not about to abandon that value. However, could there be room for a shift in customer expectations while we wait for technological solutions to come on the market? “To reach a closed-loop model, would there be a market for garments that don’t use stretchy and comfortable materials, which often prove difficult to recycle?” Forss wonders. Would customers be willing to compromise on comfort for nature?
Price is another major consideration, especially in the current economic climate. Environmentally friendly materials are still more expensive than virgin fibres. “A fast ecological shift would also require some customers to be willing to pay more for an environmentally friendly choice.” New technologies, innovations or product lines often come with a premium in the beginning. “Can we hope to change the world without having to invest?” asks Forss.
Finding solutions through strategic partnerships
As we strive to meet our targets, so much of our success is dependent on what happens outside the walls of our organisation. As much as 70% of our emissions are produced by suppliers and subcontractors. As a forerunner in sustainable practices, we can influence the wider industry through our actions and choices.
Forss highlights this with reference to the partnership work with Klopman, one of our fabric suppliers, and Rester, a provider of textile recycling solutions. In the case of Rester, we have become a significant investor as the company’s second-largest owner. “We are delivering our end-of-life garments to Rester to be mechanically recycled and then our fabric supplier Klopman is developing new fabric from the material. This is currently undergoing testing, with trial uses for the fabric to follow once pilot customers have been identified.”
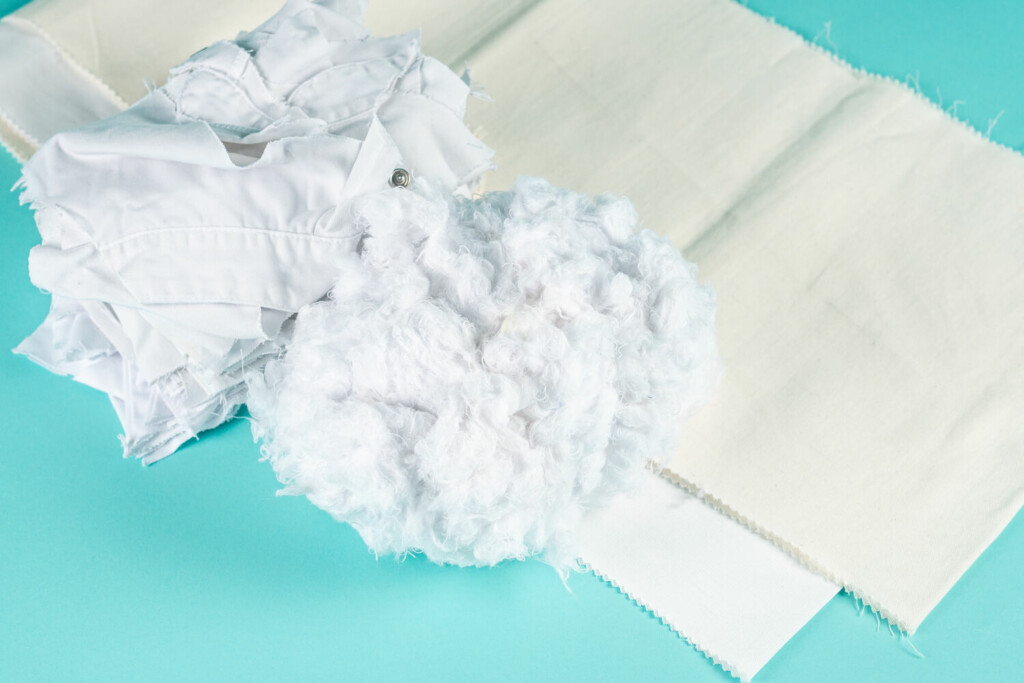
Keeping track of innovations in the wider industry
As well as the pilots with Rester and Klopman, there are many more new innovative companies on the market which we are monitoring closely. “In terms of recycling, there are new technologies born and we hope those can bring new options for utilising textiles for new textiles in the future”.
Forss also brings up the groundbreaking innovations achieved with recycled fibres made using the Ioncell method. “Our cotton towels were used a couple of years ago in experimentation at Aalto University, where the researchers achieved surprisingly good results in tensile strength.”
“We can say the textile industry is experiencing a new revolution. Some companies are utilising biobased materials to create new sustainable textile fibres. In general, we are following the development of these companies with interest and will be very excited if their innovations can impact our work in the future”.
FOUR TIPS TO IMPROVE THE SUSTAINABILITY OF YOUR MATERIALS
1. Don’t sacrifice durability
Choose options with a long life cycle so you maximise the use of each product. Remember that the impact of production is just as significant for the environment as the use of recycled materials.
2. Be willing to choose the more expensive option
It can offer better quality and therefore be used for a longer period.
3. Choose products that can be repaired
Avoid wasting items that are still usable but might require a simple fix or to have some part of their aesthetic condition refreshed.
4. Select partners who can recycle
They can turn end-of-life products into raw materials for similar or alternative products and reduce the usage of virgin materials.
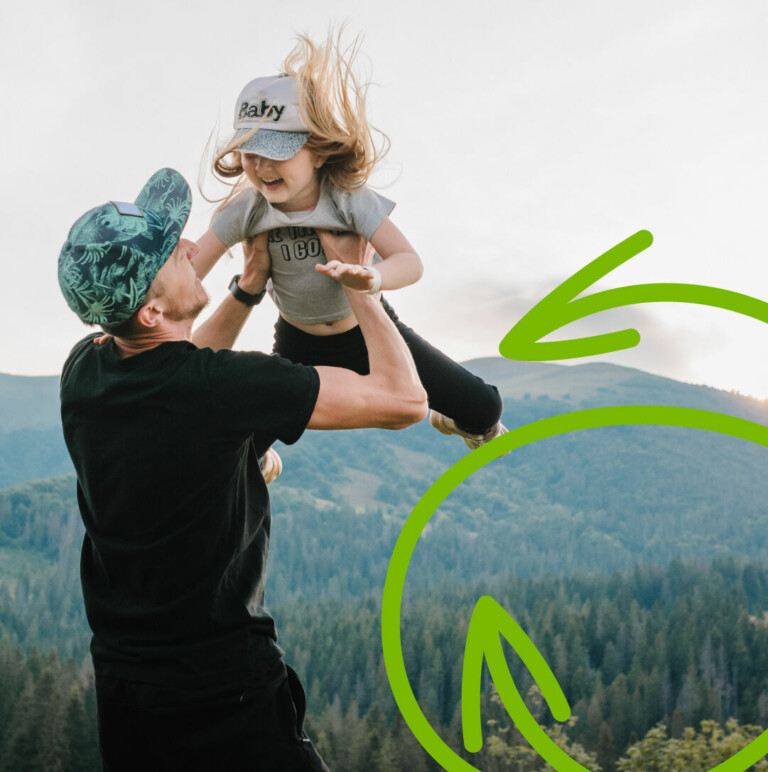