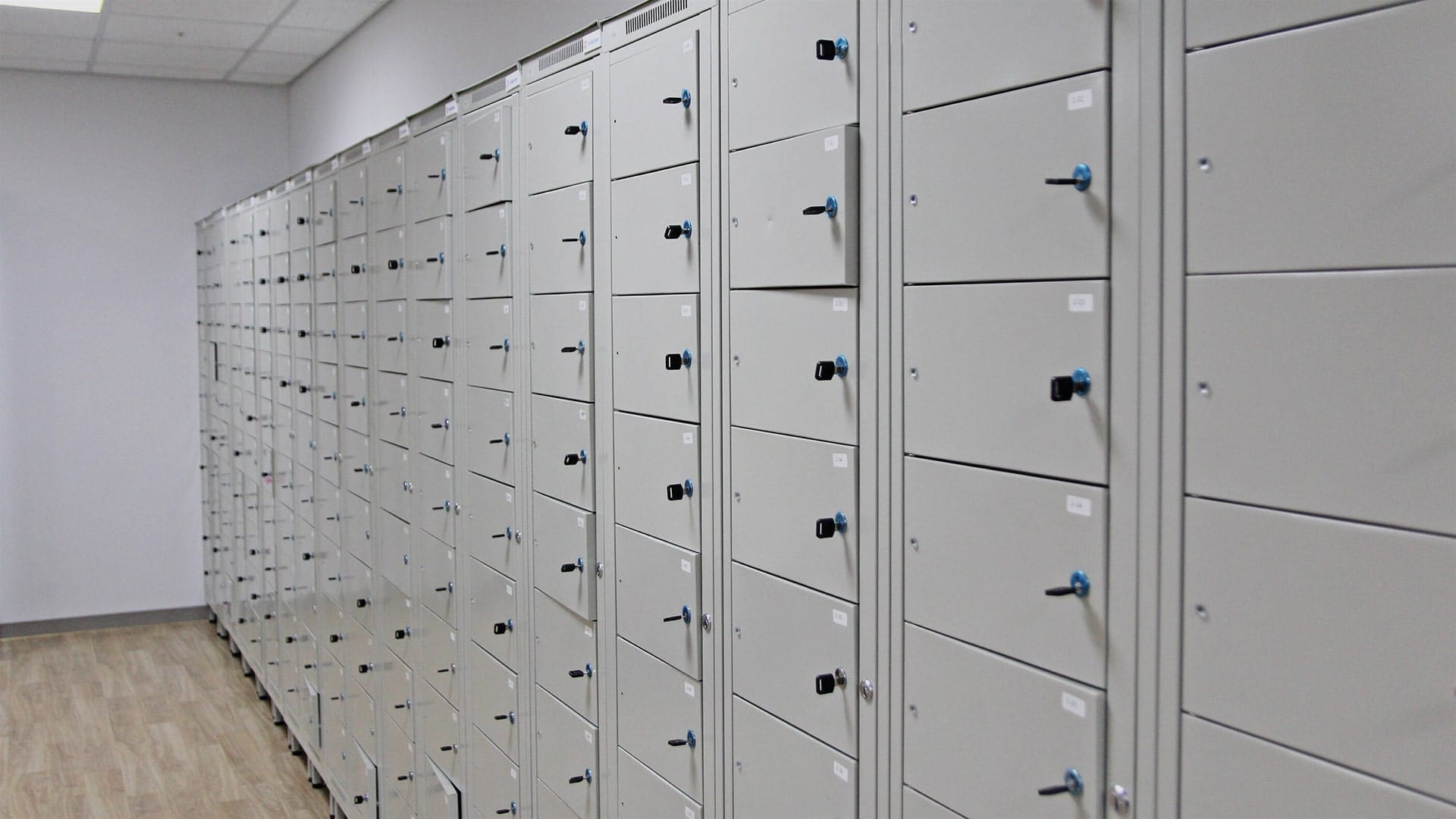
How to Equip Employee Locker Rooms and Changing Rooms: Practical Guide
Providing well-equipped employee locker rooms and changing rooms is essential for safety, hygiene, and employee satisfaction.
These spaces not only help workplaces meet legal obligations but also support smooth operations, especially in environments where workwear is required.
In this guide, you’ll learn what the UK changing room requirements are, what the best locker rooms include, and how to tailor your setup for different industries, including construction, engineering, and mechanical environments.
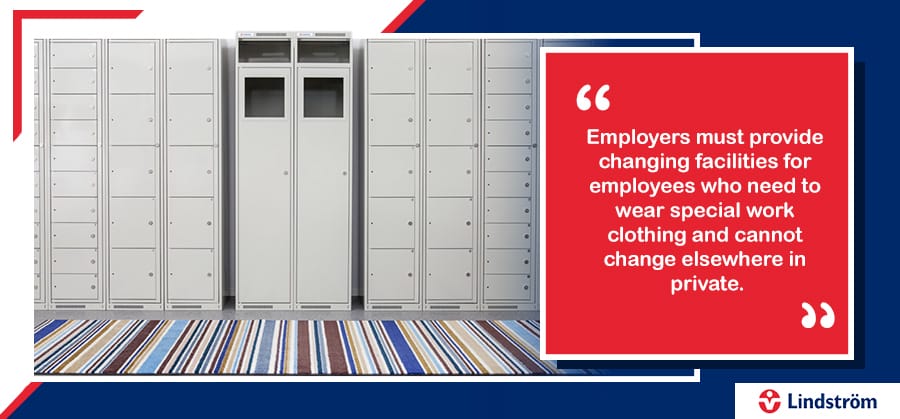
What are the Employee Changing Room Requirements in the UK?
Under the Workplace (Health, Safety and Welfare) Regulations 1992, employers must provide changing facilities for employees who need to wear special work or protective clothing and cannot change elsewhere in private.
Changing room requirements include:
- Adequate space for undressing and dressing without overcrowding
- Privacy between male and female employees (e.g. separate rooms or clearly marked time slots)
- Access to toilets and washing facilities either in or near the changing area
- Secure storage such as lockers or cubbies for personal items
- Reasonable hygiene levels, including regular cleaning and ventilation
- Facilities for drying wet clothing where needed
These apply in industries where workwear or protective gear is legally required or practically necessary for safety and hygiene.
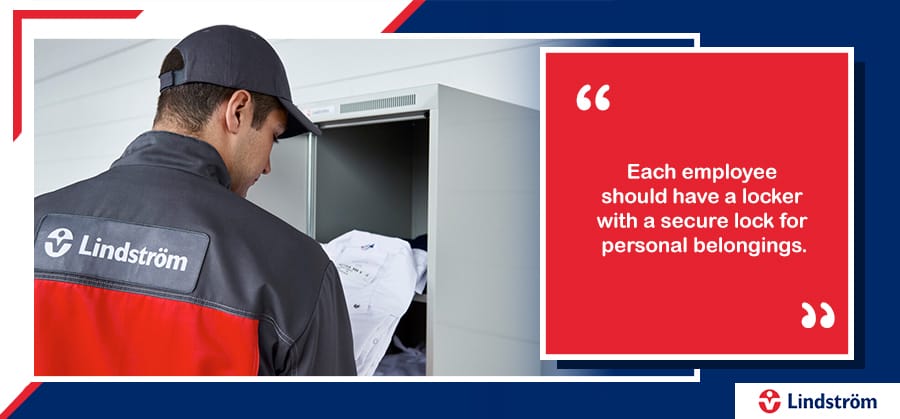
Core Locker Room Requirements for a Well-Equipped Workplace
Whether designing a new locker room or improving an existing one, consider these must-have features:
1. Spacious and Accessible Layout
Locker rooms should allow multiple employees to change at once without crowding. Layouts should support easy movement, with lockers placed away from doorways or traffic routes.
2. Secure Individual Lockers
Each employee should have a locker with a secure lock for personal belongings. Options may include:
- Key locks
- Digital code locks
- Master key systems for supervisory access (e.g. for laundry restocking)
3. Hygiene and Cleanliness
Changing rooms should be kept clean and hygienic, with:
- Non-slip flooring
- Waste bins and laundry bins for used garments
- Handwashing stations, soap dispensers and clean towels
- Ventilation or air purification systems
4. Integrated Workwear Systems
For businesses using a workwear rental service, lockers can double as delivery and collection points. For example, Lindström provides lockers with:
- Personal compartments for each employee
- Central collection units for used garments
- Scheduled restocking of clean workwear
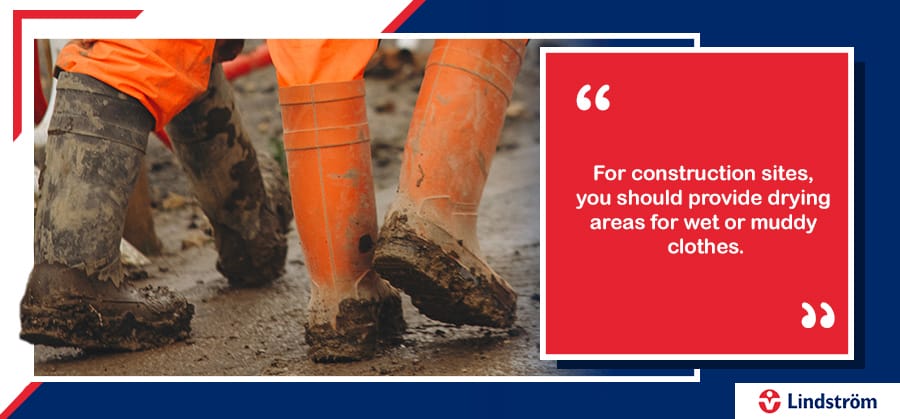
Industry Examples: What to Include in Different Locker Rooms
Construction Sites
Construction workers face variable weather, heavy-duty physical work, and strict safety gear requirements.
Best practices:
- Provide drying areas for wet or muddy clothes
- Flame-retardant workwear and high-visibility clothing must be safely stored
- Space for changing out of PPE like helmets, boots and gloves
- PPE lockers or secure cubbies for larger gear
Engineering Workplaces
Engineers often work in environments where cleanliness, technical precision and safety overlap.
Best practices:
- Secure lockers for storage of tools, gloves and electronics
- Flame-retardant or anti-static garments depending on environment
- Durable benches and hooks for protective gear
- Individual lockers with ventilation for drying sweaty or soiled clothes
Mechanical Workshops
Mechanics deal with grease, oil, heavy equipment and often need multiple clothing changes during a shift.
Best practices:
- Robust locker units that can withstand heavy use
- Absorbent mats outside changing areas to reduce oil tracking
- Used clothing collection points near exits
- Nearby access to handwashing and cleaning supplies
How Lindström Supports Locker Room Compliance
Lindström offers workwear locker services and industrial workwear solutions designed to meet workplace locker room requirements. Our service includes:
- Personalised lockers with individual secure locks, and a master key for supervisors/ team leaders
- Collection units for used garments
- Clean workwear restocked regularly by our team
- No upfront costs and a predictable service schedule
- Laundry processes that meet ISO 9001 and ISO 14001 standards
Frequently Asked Questions
What are the legal employee changing room requirements in the UK?
Employers must provide safe, hygienic, and private changing facilities with secure storage if workers wear special or protective clothing.
What are standard locker room requirements?
Locker rooms should have secure lockers, hygiene stations, non-slip floors, and space for workers to change clothes and store belongings.
Do all employers need to provide changing rooms?
Only if workers need to wear work-specific clothing and cannot change elsewhere in privacy.
How can I integrate workwear services into locker rooms?
Using locker systems with separate units for clean and used clothing allows for seamless integration with workwear rental services like Lindström’s.
Which industries require changing rooms?
Sectors such as construction, healthcare, food production, engineering and mechanical workshops typically require dedicated changing rooms.
Final Thoughts
Meeting employee changing and locker room requirements is about more than compliance—it’s a matter of professionalism, hygiene, and respect for your staff.
Tailoring facilities to the specific needs of your industry improves safety, simplifies workwear management and enhances overall morale.
Lindström UK can support your business with workwear locker services, workwear rental, and industrial laundry solutions designed around your team’s needs. Contact us today to learn how we can help build cleaner, safer, and smarter changing rooms.