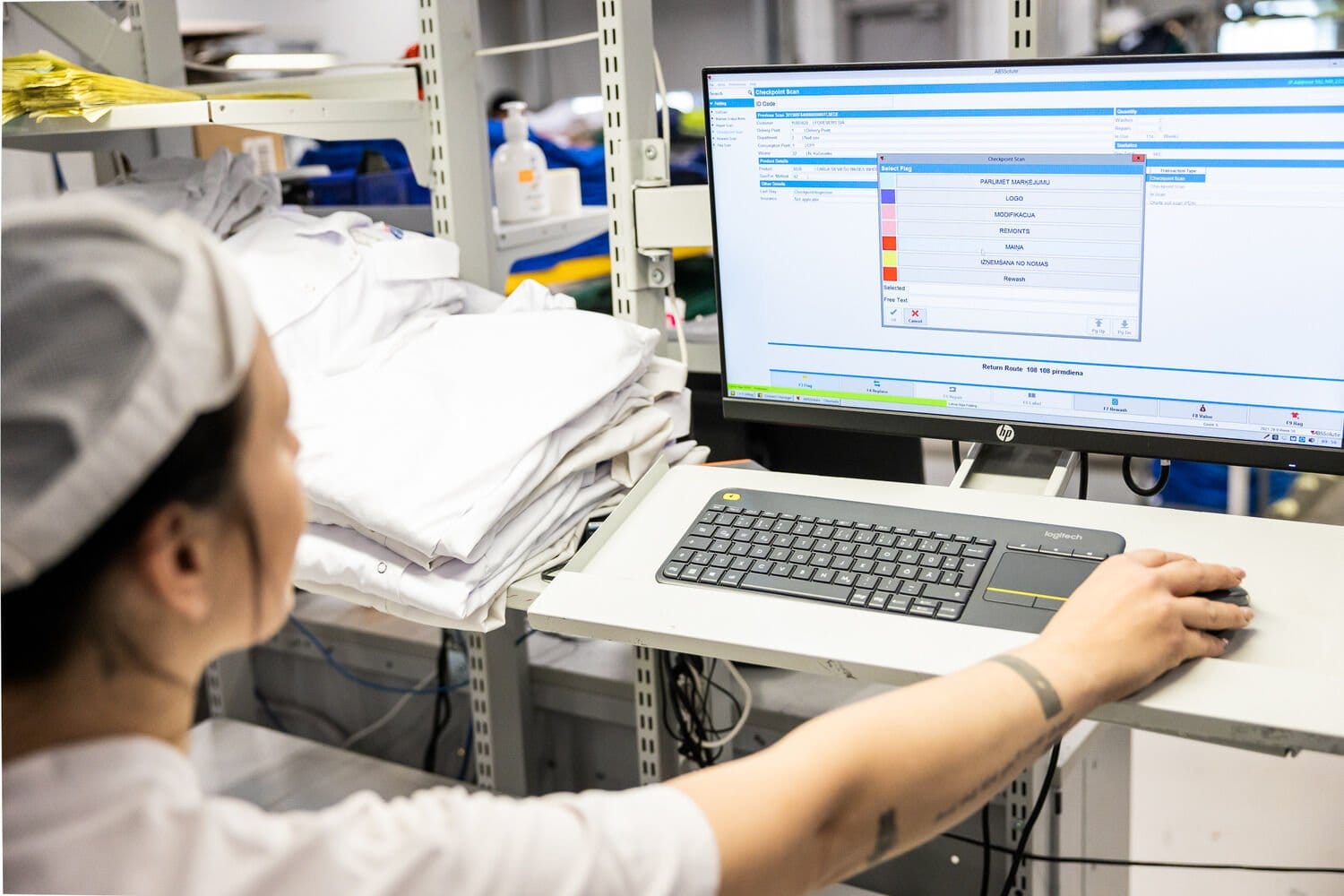
Using RFID Chip Technology In Workwear To Optimise Workplace Processes
Digitisation facilitates a number of processes for companies, thereby saving time, human resources and finances. In addition, it increases the reliability and safety of work procedures. An example is the RFID chip technology used in Lindström work clothes.
By using RFID chip technology to monitor rental clothing, you have access to multitudes of information to help improve workplace processes.
What Is RFID Chip Technology?
RFID stands for Radio-Frequency Identification. It is a technology that uses wireless communication to identify and track objects, animals, or people. RFID works by using radio waves to transmit data between a chip and an RFID scanner. Each chip has a unique ID transmitted via the radio waves allowing you to manage items easily without contact.
RFID technology is used in various industries and applications, including supply chain management, inventory tracking, access control, and transportation.
When used in clothing, RFID chips can be embedded for a range of purposes, including:
- Inventory Management: Retailers can use RFID to track the movement of clothing items in stores or warehouses. This helps optimise stock levels, reduce theft, and improve the efficiency of restocking and replenishing shelves.
- Authentication: High-end or luxury clothing brands may use RFID to verify the authenticity of their products. Customers can use RFID readers or smartphone apps to verify that a product is genuine.
- Product Lifecycle Tracking: Manufacturers can use RFID to track production and distribution of garments, allowing quality control and accountability.
- Wash and Care Instructions: RFID tags can store care and washing instructions for clothing items that consumers can access.
- Sustainable Fashion: RFID can be used to track the lifecycle of garments and provide information on the materials used, allowing consumers to make more informed choices based on sustainability and ethical considerations.
What are the components of RFID systems?
RFID Tags or Chips:
These are the small electronic devices that store and transmit data via radio waves when prompted by an RFID reader. Tags can be passive (powered by the reader’s signal) or active (with their own power source), depending on the application.
RFID Readers:
These are devices that use radio frequency to communicate with RFID tags. Readers emit signals to activate tags, receive the data transmitted by tags, and relay this information to a central system.
RFID Middleware:
Middleware software is used to manage the data collected from RFID readers and integrate it into existing systems or applications.
What is the RFID tag used for in Lindström clothing?
RFID chips are used to digitise the cycle of work clothes rented through Lindström.
Each item has a unique chip that employees scan to register the garment’s movement in the online system. This means there is always an assigned status to show the location of each item.
Thanks to this smart technology, all employees:
- Have optimal number of items of clothing.
- Can prevent clothes from getting lost.
- Ensure nothing is missing, nothing remains.
The RFID chips can be used to register necessary orders for repairs or the need for new items of clothing. Digitising the circulation of work clothes allows you to keep a detailed record of each piece of clothing and the data gathered is easy to download.
How reporting works in the eLindström customer application
Our digital app, ‘eLindström’ allows our customers to scan the RFID chips that are placed in the clothing and accessories with the in-built app RFID reader.
Reporting is intuitive in our eLindström application, simply select a time period to see an overview of all the garments you have rented within it. For each item of clothing, you can see who it’s assigned to, where it is, how many times it’s been laundered, and how many repairs it has undergone. From this data, you can generate reports directly in the application to then be downloaded into an Excel format.
While the reporting respects the protection of personal data and does not reveal anything personal about employees, it can offer valuable information about how employees use work clothes and what their requirements are.
Using the eLindström application, there are 5 individual types of reports that are generated in just a few clicks:
- Invoicing statement: An overview of the products billed for in the rental period (only the products that are billed are listed).
- Products by employee: Overview of clothing used by employee. The model, size and number of pieces are indicated.
- Residual values: Overview of clothes given to the customer for replacement.
- Orders: Overview of orders according to the selected period.
- Products: Overview of all products in the rental period (all products are listed).
Watch this short video to see how our eLindström app e-service makes it possible for customers to browse through the product range, make an order, and manage the workwear service 24 hours a day, seven days a week.
Modification of the work environment with regard to work safety and ergonomics.
If you record unusually high numbers of repairs for an employee, it is possible that their work environment needs improvements. With this, the company can focus on the safety and ergonomics of that workplace and asses the hazards that may be contributing to the damage of the workwear.
Potential hazards to consider include sharp edges catching on clothing causing tears, incorrect tools and implements, and inappropriately laid out work areas which can result in paint or chemical spills on clothing.
Problems that are identified can then be eliminated, increasing safety, efficiency and preventing more serious injuries from occurring.