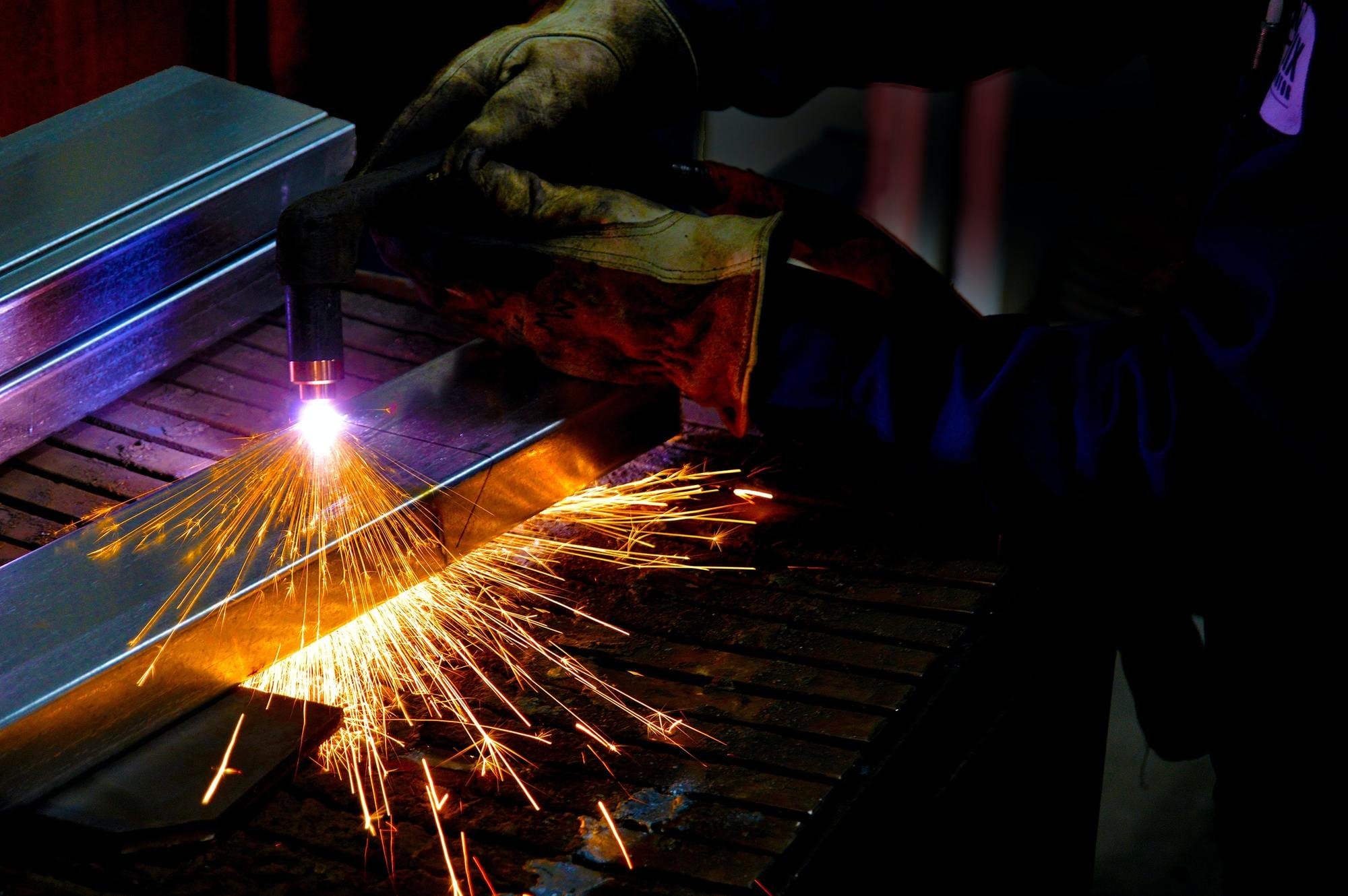
Welding hazards and risk management
All welders should manage welding hazards by carrying our a risk management assessment before beginning welding work. There are several hazards and working situations that welders should be aware of. Paying attention to and planning around these will arm you for protecting yourself from flames, fire, sparks, explosions, molten metal, electric shock, and a lack of oxygen while being aware that working in a confined working space can increase these dangers.
Here we will take a look at four welding hazards that should form the basis of your risk assessment. These include fire and explosions, electrical hazards, low oxygen and welding gases, and stray welding currents.
Before you begin any welding work, you should start with the basics. Ensure you have clean and dry welding overalls and gloves. These should be well-fitting so that they minimise the amount of bare skin exposure, especially for the legs and arms. Welders overalls are the first line of defence for preventing severe burns from high heat sources, heat radiation, fire, and molten metal sparks.
The Lindstrom workwear rental range includes all-in-one flame retardant overalls, flame retardant trousers, and flame retardant jackets. These are made from welder CL 2 420 material, complying with EN ISO 11611: 2015, A1 Class 2, and EN ISO 11612: 2015, A1 B1 C1 E3 F1 protective clothing regulations.
Fire and explosions
You should begin your risk management by removing materials from the worksite that are combustible, including paper, fabric, cardboard, and wood. You should consider that drips of metal and sparks can travel large distances, and possibly into adjacent rooms.
Where flammable materials cannot be removed, you should arrange a fire watch during the work and for 30 minutes afterwards. You can extend the fire watch to 60 minutes when accidental ignition may be hard to spot or slow to develop.
Welders should drain flammable liquids from drums and tanks to be worked on and clean these to prevent the ignition from the remaining residue. Whenever you move acetylene, ensure that the main gas cylinder valve is closed.
High-risk locations for fire include enclosed spaces and inside ships, where smoke cannot dissipate quickly. In all instances, flameproof overalls are essential for protecting welders against fire.
You can find further guidance on this topic in HSE’s Fire and explosion guide.
Electrical hazards
The welder is responsible for conducting daily equipment checks and reporting defects. Arc welding with a live electrical circuit puts welders at a higher risk of electrical hazards than TIG, MIG, and MAG welders, making these checks vital.
Your first step in preventing electrical hazards is to protect your skin from electrical burns and electrical shock by wearing appropriate personal protective equipment (PPE). You should ensure the welding equipment conforms to British standards (BS) and international standards (ISO).
Next, ensure the installation of welding equipment is carried out by a trained professional. Check the insulation of the welding leads, return leads, clamps, and plugs for damage and confirm that the insulation is thick enough to carry the current safely.
Clean all connections, check for damage and ensure these are correctly rated. You should use an insulating mat or dry platform when welding occurs in damp or wet conditions.
Low oxygen levels and welding gases
Even if the workspace is not confined, you should plan for the possibility that the workspace might become confined as your weld. Chemical reactions and inert gasses can lower the amount of oxygen inside tanks, pits, or pipes.
Your risk management should determine if the job can be carried out in a way where you can work without entering the confined space. If there is no option but to weld in a confined space, you should use a safe working system and create an emergency rescue plan. Do not fall into the trap of creating a severe fire risk by using oxygen supplies to improve the air quality.
The risks of welding gases are high because the gases have no smell. You can quickly pass out before you realise what is happening, causing death from asphyxiation. This can happen without producing symptoms such as breathlessness, panting, coughing, or spluttering.
Welding gases cause danger because they can displace oxygenated air with carbon dioxide, argon, helium, and nitrogen through their accumulation. Carbon dioxide and argon are heavy gasses, which encourages them to pool in spaces where you would not expect to encounter a problem, such as in vehicle inspection and maintenance pits.
Always watch out for partial gas replacement symptoms such as tiredness, confusion, and weakness. You can find more information in the Confined spaces: A brief guide to working safely.
Stray welding currents
Stray welding currents can cause burns and electric shock. To lessen the risks, clamp the current return cable close to the welding area and ensure the clamp is fitted to clean metal and not a rusty surface. Do not clamp onto handrails, framework, or pipes of large structures, unless they are part of the workpiece.
So, welding hazards and risk management is not as much of a headache as you might think. Wear flameproof overalls, ensure equipment is well-maintained, and plan a response in preparedness for any incident.