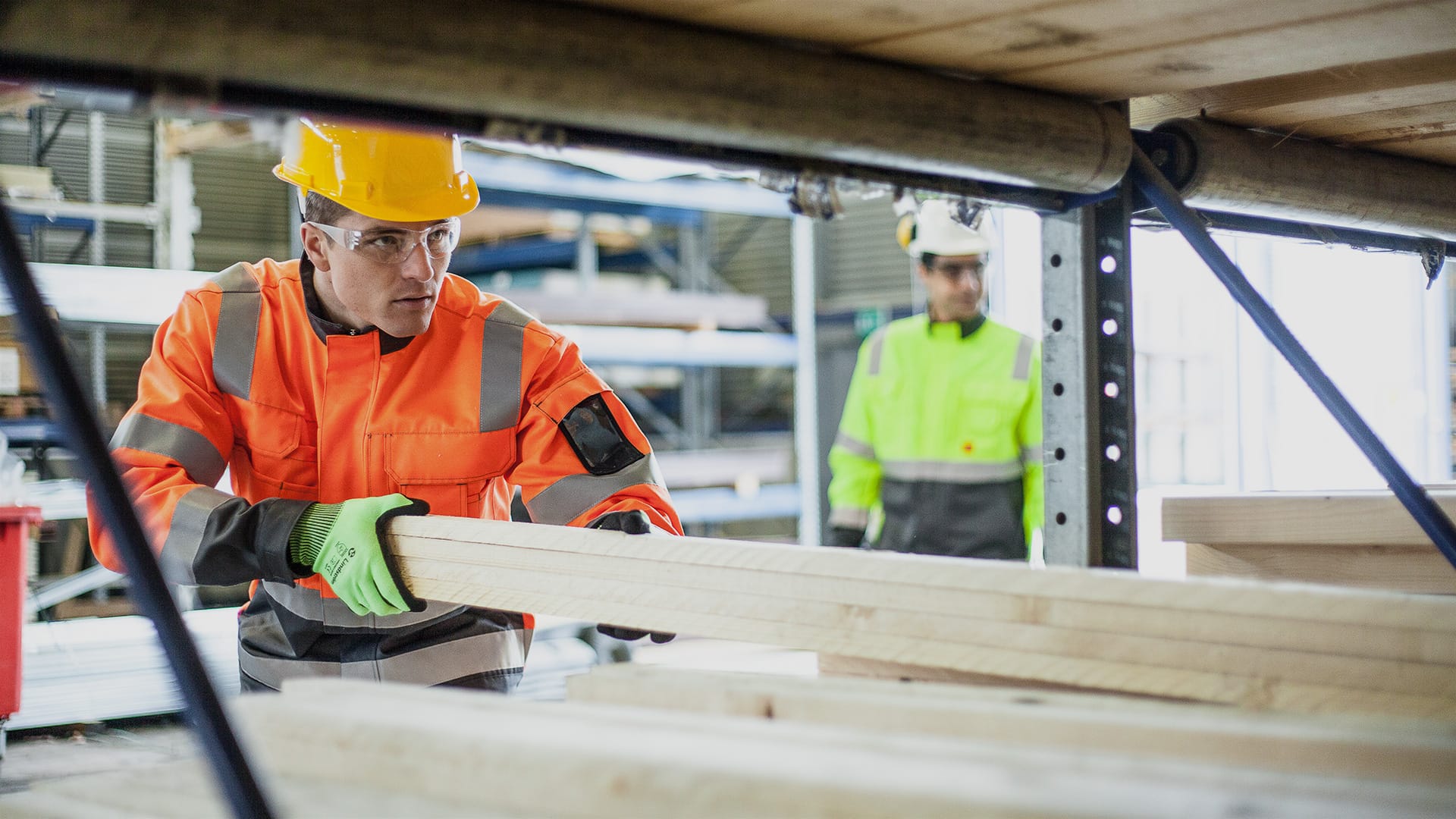
Health and Safety in the Printing Industry: A Guide
Workplace safety is a legal and operational priority in the UK’s fast-moving printing sector.
Whether you run a print shop, manage commercial printing operations, or operate a publishing facility, understanding the core risks and regulations can protect your team and ensure business continuity.
In this guide, we outline essential health and safety measures in printing, the legal duties of employers, and best practices to reduce risks from manual handling, machinery and chemical exposure.
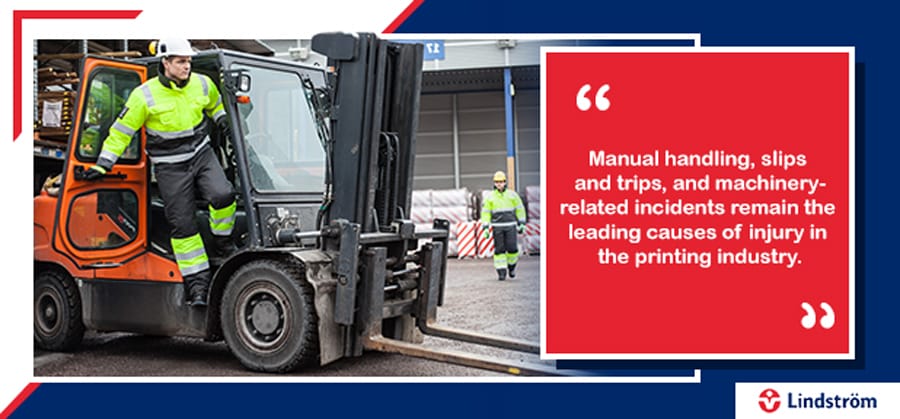
Why Is Safety Important in Print Environments?
The UK printing sector is classified under manufacturing by the Health and Safety Executive (HSE), grouped within SIC 18: Printing and reproduction of recorded media.
According to HSE Manufacturing Statistics 2024:
- 94,000 manufacturing workers reported work-related ill health, with 36% related to musculoskeletal disorders
- Manual handling, slips and trips, and machinery-related incidents remain the leading causes of injury
- The industry sees around 51,000 non-fatal injuries annually, and the fatal injury rate is 1.6 times higher than the all-industry average
These risks directly affect the printing environment, where heavy lifting, fast-moving equipment, and chemical exposure are common. That’s why robust safety protocols are essential to protect staff and maintain productivity.
Accidents not only affect employees but can lead to production delays, reputational damage, legal penalties, and increased costs.
Key Printing Industry Safety Regulations
Here’s a breakdown of the most relevant UK safety regulations for printing operations:
Regulation | Purpose |
Health and Safety at Work Act 1974 | Sets out the general duty of employers to protect the health, safety and welfare of their employees |
Manual Handling Operations Regulations 1992 | Mandates that employers avoid hazardous manual handling where possible, and assess risks where it can’t be avoided |
COSHH 2002 | Requires employers to assess and control exposure to harmful substances such as inks, cleaning solvents, and chemicals used in printing |
PUWER 1998 | Requires all work equipment, including printing presses, to be properly maintained, inspected, and used by trained personnel |
RIDDOR 2013 | Specifies which incidents must be reported to the HSE |
If you’re producing printed materials, booklets, or running commercial printers in an office setting, these rules apply regardless of business size.
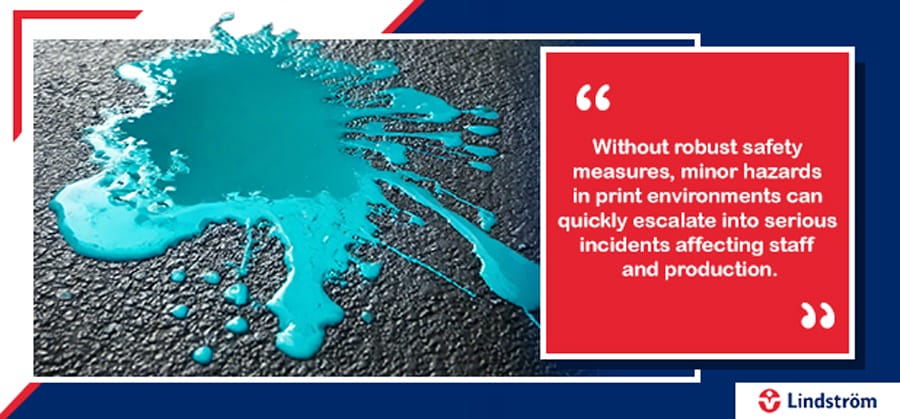
Common Health and Safety Risks in Printing
1. Manual Handling Injuries
Manual handling remains a leading cause of lost workdays in printing. Activities include:
- Lifting heavy paper reels, plates or ink drums
- Moving finished materials to storage
- Loading machinery with materials
How to manage:
- Use lifting aids such as trolleys, hoists or scissor lifts
- Break loads into smaller weights
- Train staff using the HSE’s MAC Tool
2. Slips, Trips, and Falls
Slip and trip incidents are typically caused by:
- Ink or oil spills on floors
- Poorly routed cables or hoses
- Dust or powder from paper processing
How to manage:
- Install non-slip mats
- Use absorbent spill mats
- Keep walkways clear and marked
3. Machinery-Related Accidents
Printing presses, guillotines and finishing equipment can cause severe injuries if not properly guarded or maintained.
Compliance tip:
Under PUWER, all machines must:
- Be fitted with emergency stops and guards
- Be used only by trained personnel
- Be subject to scheduled inspections
4. Exposure to Hazardous Substances
Many printing companies still use solvent-based inks and cleaning agents that emit harmful vapours or fumes.
Under COSHH, employers must:
- Carry out chemical risk assessments
- Provide suitable PPE (gloves, goggles, masks)
- Ensure safe storage and spill control
- Offer staff training and health surveillance
Typical symptoms of overexposure include headaches, dizziness, skin irritation, and respiratory problems.
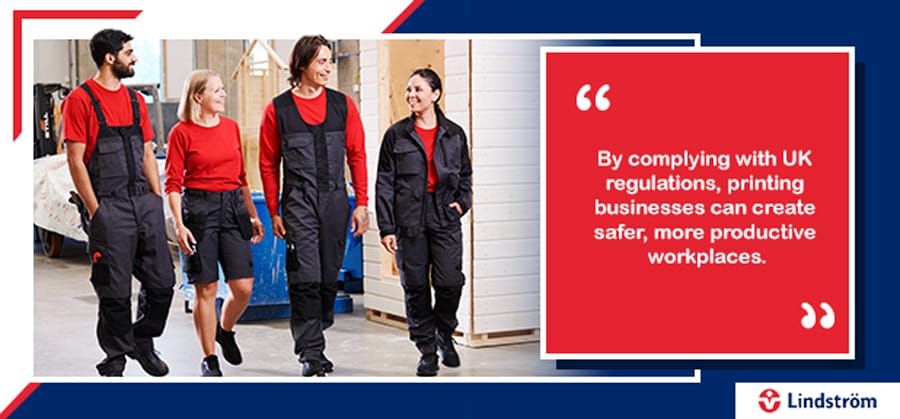
Practical Steps to Reduce Health and Safety Risks
Complete Risk Assessments
Use standardised templates to assess the likelihood and severity of risks across all tasks and areas. These should be updated annually or when processes change.
Provide Proper Training
Employees should receive regular training in:
- Safe lifting techniques
- Fire safety and evacuation
- COSHH controls
- First aid and accident reporting
Improve Facility Layout
Workstations should:
- Have enough space for safe movement
- Allow easy access to emergency exits and first aid stations
- Include ergonomic adjustments to reduce strain
Use Cleaning and Spill Control Products
Workplace hygiene is crucial in preventing slip hazards, contamination, and product defects.
Lindström’s Safety Solutions for the Printing Industry
Lindström supports printing businesses with high-performance print wipers and absorbent spill mat rental services. These solutions improve safety, reduce waste, and ensure compliance with hygiene and environmental standards.
Printer Wiper Rental
Lindstrom is the only UK Provider Transporting Wipers Under UN3175
Lindström is the only UK company that handles the transport of used print wipers classed as UN3175 — a type of hazardous material under UK law. This means you get safe, legal, and fully compliant logistics for your business.
- Made from durable, 100% cotton
- Ideal for cleaning printing plates, machinery, toner and ink
- Washable, reusable and lint-free
- Delivered, laundered and restocked
Absorbent Spill Mats
- Designed to capture ink, solvents and oils
- Prevent workplace slips and equipment damage
- Installed beneath machines and along walkways
- Available in various sizes for different zones
All products are part of our managed rental service, which includes regular pickup, professional laundering and replacement—freeing your team from stock and waste concerns.
Final Thoughts
The printing industry may not appear dangerous on the surface, but the risks are real. From COSHH-regulated chemicals to moving heavy reels and working with high-speed machinery, it’s essential to stay proactive.
By understanding key health and safety risks, implementing best practices, and partnering with trusted providers, print businesses can operate more safely, reduce downtime, and remain compliant with UK law.