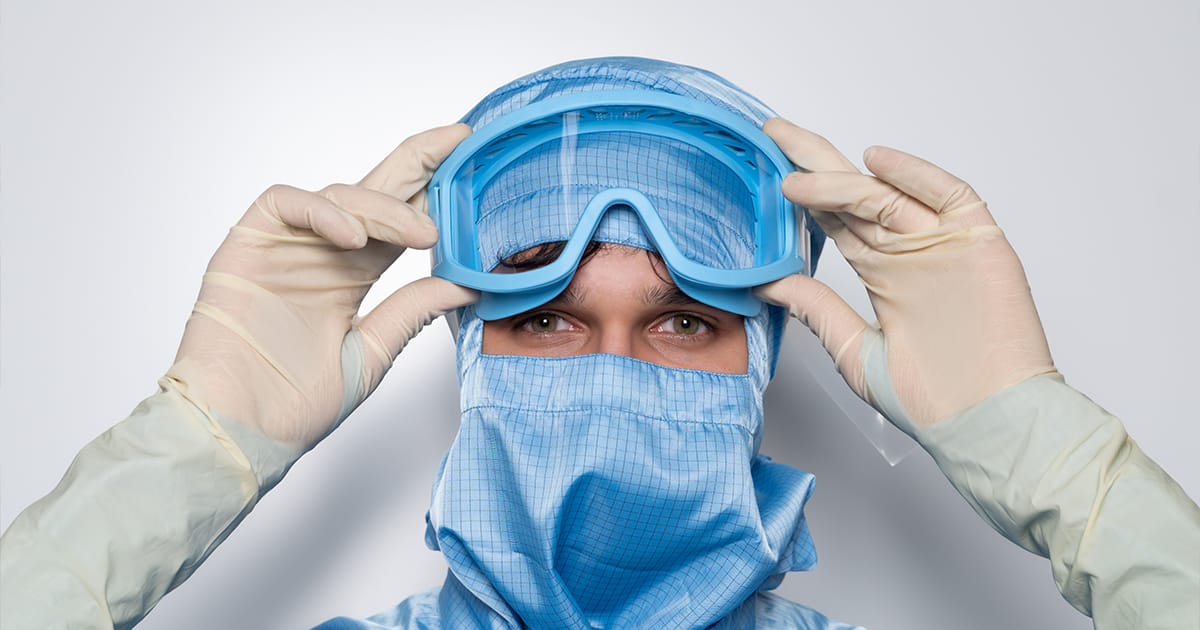
Why are cleanroom gowns critical in semiconductor manufacturing?
In the field of semiconductor manufacturing, maintaining a contaminant-free environment is a top priority. The intricate and delicate nature of semiconductor components means that even the smallest particle can disrupt the manufacturing process, leading to defects and significant financial losses. This is where cleanroom gowns play a critical role. By providing a barrier between the human body and the cleanroom environment, these gowns help to minimise the introduction of contaminants.
Cleanroom gowns are part of a comprehensive sterile gowning procedure designed to maintain high levels of cleanliness. They are specifically engineered to prevent the shedding of skin particles, hair, and other potential contaminants that could compromise the cleanroom environment. In doing so, they protect the integrity of semiconductor components, ensuring that the manufacturing process can proceed without interruption.
How cleanroom gowns protect semiconductor components
The primary function of cleanroom gowns in semiconductor manufacturing is to shield sensitive components from particles, dust, and other contaminants. These components are often manufactured at a microscopic scale, where even a speck of dust can cause failure. Cleanroom gowns are essential in creating a barrier that prevents these contaminants from reaching the delicate surfaces of semiconductors.
In addition to acting as a physical barrier, cleanroom gowning supplies are designed to be low-linting and non-shedding, which means they do not contribute additional particles to the environment. This is crucial in a setting where maintaining ultra-clean conditions is necessary for product quality and reliability. The use of specialized materials in the gowns ensures that they are effective in providing the required level of protection.
The role of ESD protection in cleanroom environments
Electrostatic Discharge (ESD) is a significant concern in cleanroom environments, particularly in semiconductor manufacturing. ESD can damage sensitive electronic components, leading to malfunctions and reduced product yields. Cleanroom gowns help mitigate this risk by incorporating materials and designs that provide ESD protection.
These gowns are often made from conductive or static-dissipative fabrics that prevent the buildup of static electricity. By ensuring that ESD is controlled, cleanroom gowns contribute to the overall safety and integrity of the semiconductor manufacturing process. This protection is vital in preventing costly damage and ensuring that products meet high-quality standards.
Materials and design of cleanroom gowns
The effectiveness of cleanroom gowns in maintaining a sterile environment is largely due to their materials and design. These gowns are typically made from materials that offer a combination of breathability, comfort, and barrier properties. This ensures that workers can perform their tasks comfortably without compromising the cleanroom environment.
Innovative design features such as sealed seams, elastic cuffs, and adjustable closures also contribute to the effectiveness of cleanroom gowns. These features help to create a secure fit that minimises the risk of contaminants escaping from beneath the gown. Additionally, the materials used are often lightweight and breathable, ensuring that workers are comfortable over long periods of wear.
Lindström’s commitment to quality and innovation
Lindström is renowned for its commitment to providing high-quality cleanroom gowns that meet the specific needs of semiconductor manufacturing. Lindström ensures that its products offer the highest levels of protection and comfort by focusing on innovation in design and material selection. The company’s cleanroom service includes the provision of cleanroom garment laundry service, ensuring that gowns are maintained to the highest hygiene standards.
Lindström’s approach is characterized by a focus on sustainability and efficiency, leveraging cutting-edge technology to enhance product performance. The company’s global reach and local focus enable it to understand and meet the unique needs of semiconductor manufacturers across different regions, ensuring that they receive reliable and effective cleanroom solutions.
Regulatory standards and compliance
Regulatory standards play a crucial role in the manufacturing and usage of cleanroom gowns. These standards ensure that gowns meet the necessary requirements for contamination control, ESD protection, and overall safety. Compliance with these regulations is essential for semiconductor manufacturers to maintain product quality and avoid costly recalls or defects.
Cleanroom gowns must adhere to stringent guidelines that govern their design, materials, and performance. Lindström’s commitment to regulatory compliance ensures that its products meet all relevant standards, providing semiconductor manufacturers with the peace of mind that their cleanroom environments are adequately protected. This attention to compliance is a testament to Lindström’s dedication to quality and customer satisfaction.
