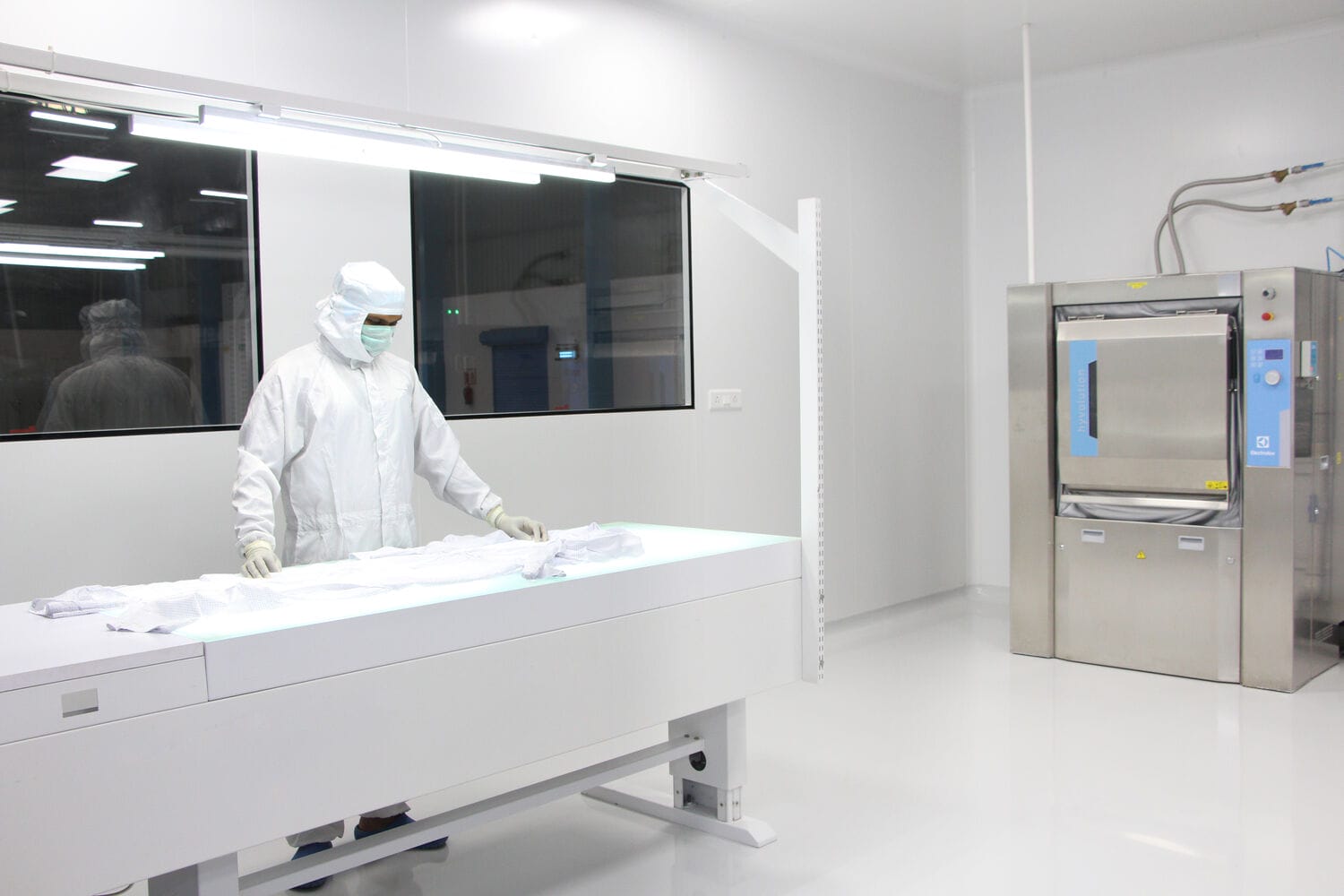
Understanding ISO Class 7 Cleanroom requirements
An ISO Class 7 cleanroom is a controlled environment designed to limit airborne contamination, ensuring product quality and compliance with industry standards. These cleanrooms are essential in pharmaceutical manufacturing, biotechnology, medical device production, and electronics, where even minute contaminants can impact product safety and efficacy.
The ISO 14644-1 standard classifies cleanrooms based on the permissible number of airborne particles per cubic meter. For ISO 7, the maximum allowable concentration is 352,000 particles per cubic meter for particles ≥0.5µm.
Key contamination control features
ISO 7 cleanrooms achieve high cleanliness levels through a combination of:
- HEPA filtration – High-Efficiency Particulate Air (HEPA) filters remove at least 99.97% of particles ≥0.3µm.
- Controlled airflow patterns – Designed to minimize particle accumulation, often utilizing laminar airflow in critical areas.
- Positive air pressure – Ensures unfiltered air does not enter the cleanroom.
- Gowning & hygiene protocols – Personnel must wear appropriate ISO 7 cleanroom garments, including coveralls, hoods, gloves, and shoe covers.
- Environmental monitoring – Continuous particle count, humidity, and temperature control ensure compliance with ISO 14644-1 and GMP guidelines (for pharmaceutical applications). Unlike ISO 14644-1, which focuses on particle control, pharmaceutical manufacturers must also comply with EU GMP Annex 1, which includes microbial contamination limits.
How an ISO 7 cleanroom operates
ISO 7 cleanrooms maintain stringent cleanliness through meticulously engineered HVAC and filtration systems. Key operational aspects include:
Entry & exit protocols – Includes airlocks, air showers, and controlled movement procedures to prevent external contamination.
Air changes per hour (ACPH) – Typically 30-60 air changes per hour, ensuring consistent particulate removal.
Filtration system – Uses HEPA or ULPA (Ultra-Low Penetration Air) filters to trap contaminants.
Gowning procedures – Personnel must wear non-linting, anti-static garments, often laundered in ISO-certified facilities.
Practical applications of ISO Class 7 cleanrooms
ISO 7 cleanrooms are widely used across multiple industries:
- Medical devices – Critical for implant production, surgical tool manufacturing, and sterile packaging.
- Pharmaceuticals & biotechnology – Required for manufacturing sterile drugs, vaccines, and injectable medications, ensuring compliance with EU GMP Annex 1 and FDA cGMP.
- Electronics & semiconductors – Used in microchip fabrication and circuit board assembly to prevent static discharge and contamination.
Common challenges with maintaining ISO 7 cleanrooms
Maintaining an ISO 7 cleanroom presents several challenges, primarily related to contamination control and equipment maintenance. Human activity is a significant source of contamination, and even with strict gowning protocols, particles and microorganisms can still enter the cleanroom environment. Regular training and adherence to ISO class 8 cleanroom gowning requirements are essential to mitigate these risks.
Equipment maintenance is another critical aspect, as any malfunction in the HVAC or filtration systems can compromise the cleanroom’s integrity. Routine inspections and preventive maintenance are necessary to ensure these systems operate efficiently. Additionally, monitoring environmental parameters such as particle counts, temperature, and humidity is crucial for maintaining compliance with ISO 7 cleanroom requirements.
ISO 7 cleanroom vs. other ISO standards
Understanding the differences between ISO Class 7 cleanrooms and other ISO cleanroom standards is vital for selecting the right environment for specific applications. ISO class 8 cleanroom requirements, for example, are less stringent than those for ISO 7, allowing for a higher concentration of particles. This makes ISO 8 cleanrooms suitable for less sensitive processes where contamination is a lower risk.
Comparatively, ISO class 6 cleanrooms have even stricter standards than ISO 7, requiring fewer particles per cubic meter. These environments are often reserved for the most critical operations, such as those in aerospace or advanced microelectronics manufacturing. By understanding these distinctions, businesses can better align their cleanroom standards with their operational needs, ensuring optimal safety and efficiency.
Understanding how ISO 7 compares to other cleanroom classes can help determine the right environment for specific applications.
ISO Classification | Max Particle Count (≥0.5µm per m³) | Common Applications |
---|---|---|
ISO 8 | 3,520,000 | Background zones, less critical processes |
ISO 7 | 352,000 | Sterile pharmaceutical support areas, semiconductor assembly |
ISO 6 | 35,200 | High-precision optics, medical device manufacturing |
ISO 5 | 3,520 | Sterile filling lines, injectable drug production |
Ensuring Hygiene & Compliance with Lindström Cleanroom Garments
ISO 7 cleanrooms demand strict garment control to minimize human contamination. Lindström’s validated cleanroom textile service provides:
- ISO-compliant reusable garments, reducing textile waste and ensuring cost efficiency.
- Laundering in ISO-certified facilities following GMP and EN 14065 hygiene protocols.
- Traceability & monitoring via RFID technology, ensuring garments remain within their validated lifecycle.
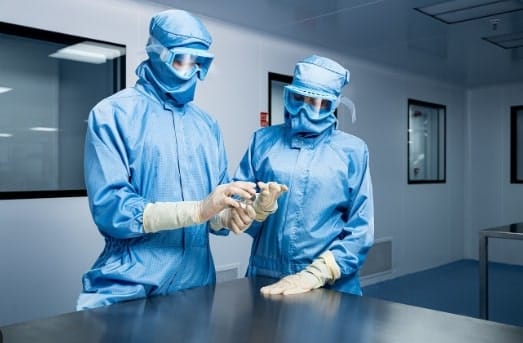
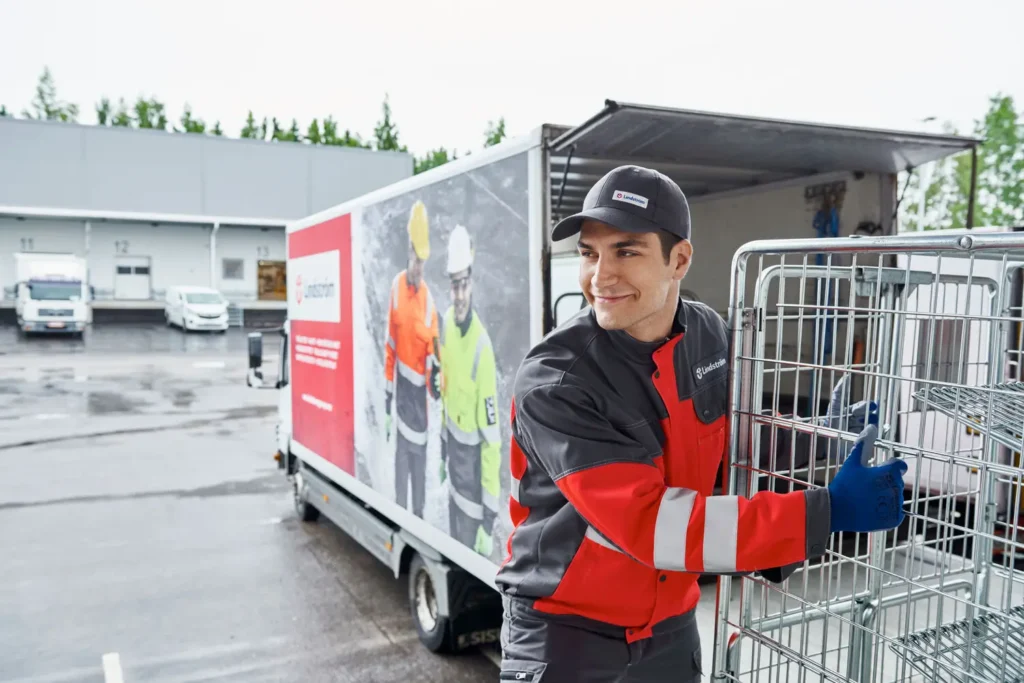