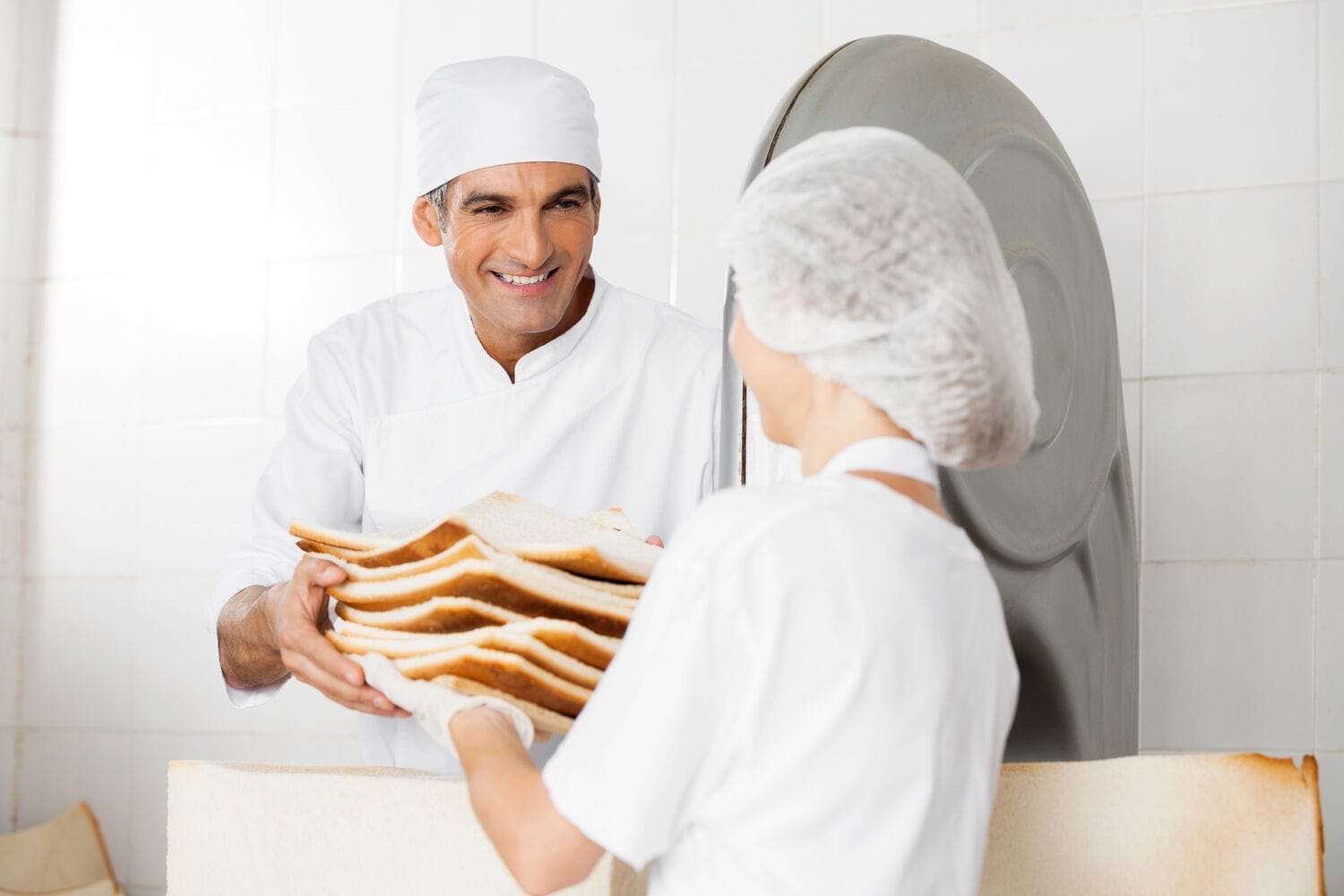
The impact of poor workwear on food safety and compliance
When considering food hygiene and safety, most eyes are on ingredients, machinery, or storage conditions. There’s one hygiene factor that often slips under the radar: food safety apparel. The truth? Poorly chosen or maintained workwear can quietly sabotage your compliance efforts and jeopardise food safety and compliance.
Let’s unpack why that matters, and how to fix it.
Why do design flaws fail audits?
Think of food industry uniforms as the frontline defense against contamination. Well-designed, properly maintained workwear doesn’t just keep staff clean; it acts as a physical barrier that protects your products from pathogens, allergens, and even foreign objects.
When done right, workwear helps reduce cross-contamination, safeguards consumers, and ticks the right boxes during inspections. But when corners are cut, say, uniforms with frayed seams, loose threads, or poor fit, those same garments can become liabilities.
What are auditors’ red flags in workwear?
Ever failed an audit because of uniforms? You wouldn’t be alone. Garment design flaws are a recurring red flag for auditors. Auditors are trained to identify red flags in food service uniforms that could compromise hygiene and safety.
Here’s what they’re looking for:
Auditors aren’t nit-picking, they’re applying standards like DIN 10524, BRCGS, and IFS Food, which demand garments meet strict design and hygiene criteria. In short, your uniforms should support, not undermine, your food safety culture.
How rental textiles can fix food safety and compliance issues
Here’s the good news: You don’t have to shoulder all this responsibility alone. Partnering with a specialised textile rental provider can transform workwear from a headache into a compliance asset.
With rental services like Lindström, you get:
Think of it as food safety insurance for your apparel, without the admin burden.
The ROI of Prevention Through Proper Workwear
Let’s talk numbers. Companies that invest in compliant workwear and hygiene services see fewer product recalls, lower audit failure rates, and reduced downtime.
A single recall can cost tens of thousands of euros, not to mention the damage to your reputation. Compare that to the manageable, predictable cost of renting compliant workwear, and the ROI becomes clear.
Plus, there’s a soft benefit that shouldn’t be overlooked: employee confidence and comfort. Staff who feel protected and professional perform better. And that performance pays dividends across your operation.
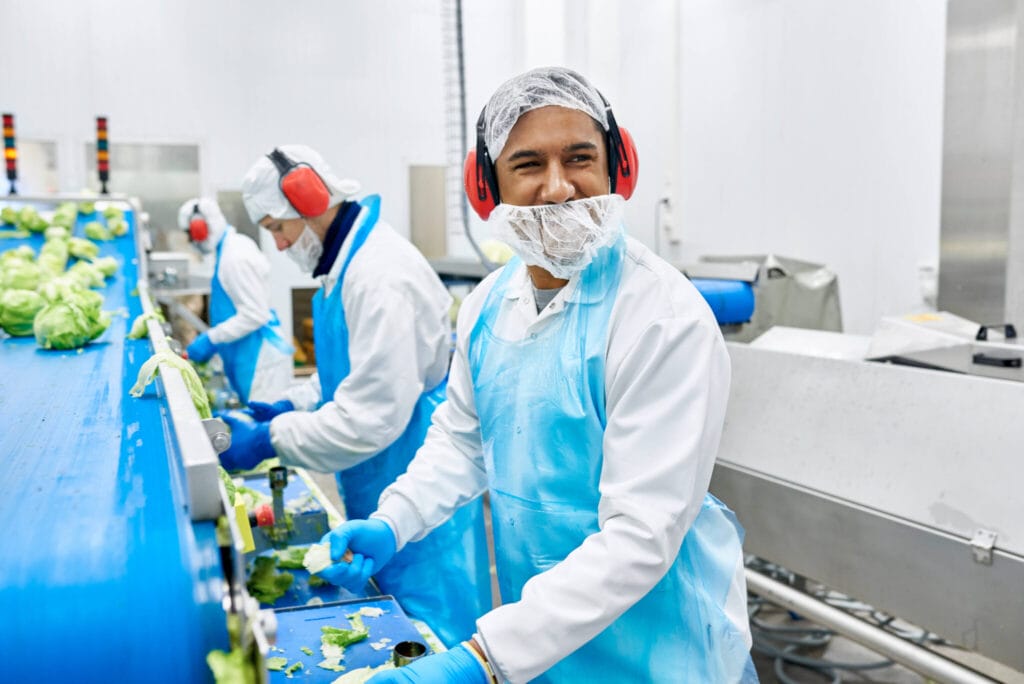