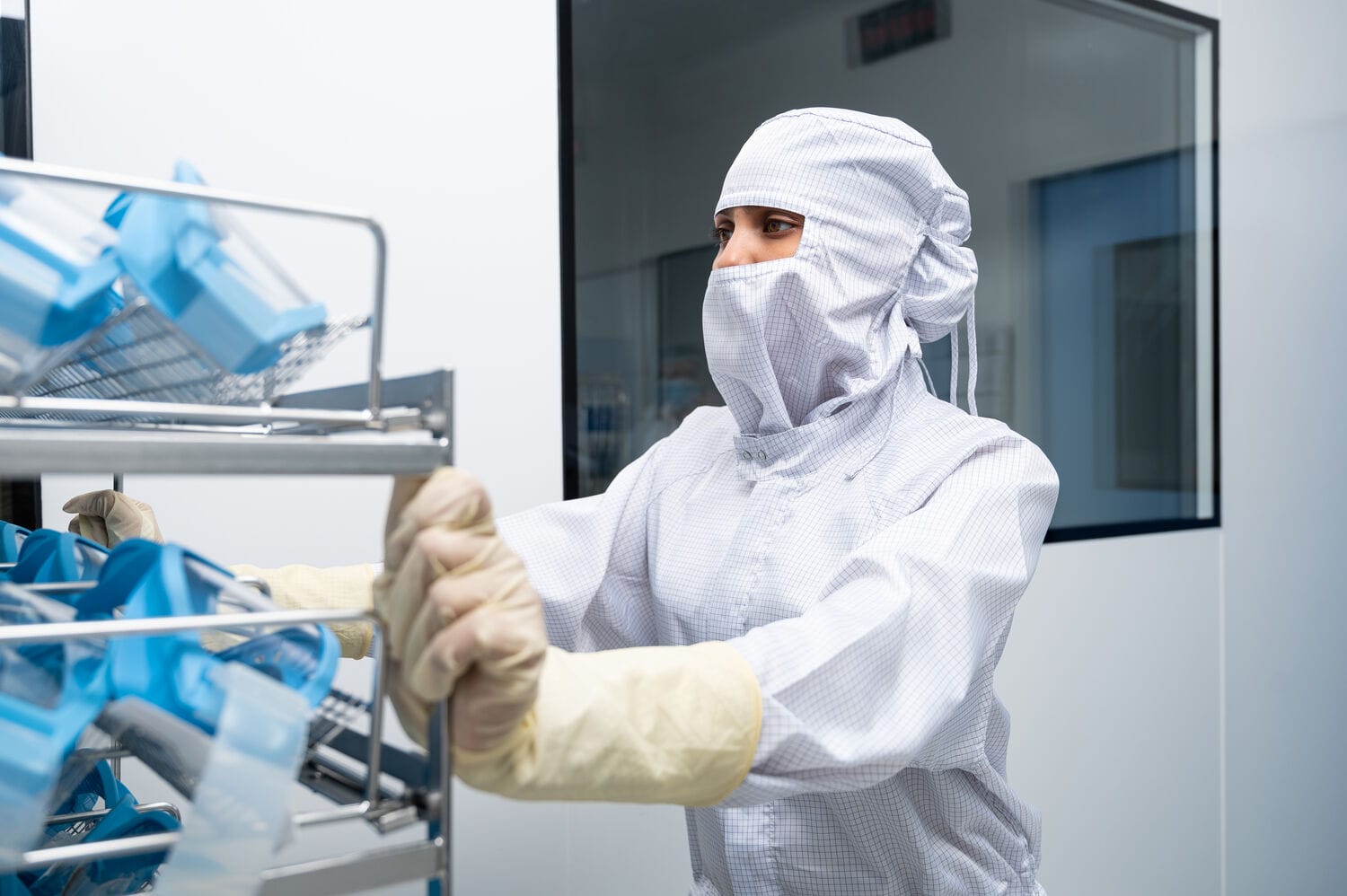
ISO Class 7 cleanroom standards: future-proofing your operations
In high-tech industries where precision and contamination control make or break success, ISO Class 7 cleanrooms play a critical role. From pharmaceuticals and biotechnology to semiconductor manufacturing, these environments are designed to maintain strict cleanliness standards, preventing airborne particles and microorganisms from compromising sensitive processes.
ISO Class 7, as defined by ISO 14644-1, regulates the maximum allowable particle count per cubic meter of air, ensuring contamination is minimized. To meet this classification, an ISO Class 7 cleanroom must not exceed 352,000 particles of 0.5 micrometers per cubic meter, significantly reducing the risk of contamination in critical manufacturing and research settings.
Core principles of ISO Class 7 standards
To maintain an ISO Class 7 environment, organisations must follow strict protocols, including air quality management, contamination control, and personnel protocols. Air change rates range between 30-60 air changes per hour (ACH), ensuring continuous removal of particulate matter. High-Efficiency Particulate Air (HEPA) filters are required to trap contaminants, and positive pressure is maintained to prevent contamination ingress from adjacent areas.
Environmental parameters such as temperature and humidity must be controlled to prevent microbial growth and static buildup. Regular particle monitoring, as per ISO 14644-2, ensures air quality remains within the prescribed limits. Additionally, pharmaceutical cleanrooms must adhere to EU GMP Annex 1, implementing rigorous microbial contamination controls and validated decontamination procedures.
Equally crucial is personnel hygiene and gowning. Individuals entering the cleanroom must follow strict gowning protocols, using garments designed to prevent contamination. These garments undergo rigorous laundering per ISO 14644 and EN 14065 standards, ensuring continued effectiveness. To enhance traceability and compliance, RFID tagging systems support companies in monitoring the lifecycle of cleanroom textiles. For example, this is a system that a reliable textile partner, such as Lindström, have implemented.
Practical Applications of ISO Class 7 Cleanrooms
ISO Class 7 cleanrooms are widely used in industries where contamination control is critical:
- Aerospace & optics: Maintains precision in component assembly for satellites, sensors, and optical instruments.
- Pharmaceutical & biotechnology: Ensures sterility in drug manufacturing, research, and medical device production.
- Semiconductor & electronics: Prevents microscopic contaminants that could cause defects in microchips and circuit boards.
Challenges in Maintaining ISO Class 7 Cleanrooms
One of the greatest challenges in maintaining an ISO Class 7 cleanroom is human-generated contamination, as personnel account for up to 80% of contaminants. Even with proper gowning, improper donning and doffing procedures, or excessive movement inside the cleanroom can introduce unwanted particles. Regular training programs, audits, and gowning validation, such as Helmke Drum and Body Box testing, help mitigate this risk.
Another critical factor is environmental and airflow monitoring. Even minor fluctuations in air pressure or filtration efficiency can compromise the cleanroom classification. Implementing automated monitoring systems allows for real-time tracking of air quality, with alerts for deviations that could jeopardize compliance.
Furthermore, compliance requirements continue to evolve, particularly with EU GMP Annex 1, which imposes stricter microbial contamination controls. Organizations must ensure that cleanroom garments and laundering processes meet ISO 14644 and EN 14065 standards, incorporating tracking systems like RFID to monitor garment lifecycle and compliance.
Future-Proofing Your Operations with ISO Class 7
As industries evolve, organizations must anticipate regulatory changes and technological advancements to stay ahead. One of the key trends is the integration of smart monitoring technologies. AI-driven monitoring systems can track airborne contaminants in real time, while automated filtration and airflow systems adjust ventilation rates dynamically based on contamination levels.
Another major focus is sustainability in cleanroom textile management. Many organizations are shifting toward reusable, high-performance garments that, when properly maintained, provide a more environmentally friendly alternative to disposables. Services like Lindström’s RFID-enabled garment tracking ensure real-time monitoring of cleanliness and garment lifecycle, helping companies prevent overuse and contamination risk.
Additionally, digitalized documentation and compliance assurance are becoming critical in ensuring audit readiness. Electronic compliance tracking minimizes human error in documentation while streamlining regulatory reporting. Lindström’s cleanroom service solutions offer validated laundering and textile management systems that help pharmaceutical manufacturers comply with ISO 14644 and GMP standards.
ISO Class 7 vs Other Cleanroom Standards
ISO Class 7 cleanrooms are often compared with other classifications, such as ISO Class 8 and ISO Class 6. The primary difference lies in particle count limits and air change rates:
Feature | ISO Class 7 | ISO Class 8 | ISO Class 6 |
---|---|---|---|
Particle Limit (0.5µm) | 352,000 | 3,520,000 | 35,200 |
Air Changes Per Hour | 30-60 | 10-25 | 60-90 |
Application Examples | Pharma, Electronics | Less critical pharma areas | High-end semiconductor manufacturing |
Choosing the right classification depends on process sensitivity, regulatory requirements, and contamination control needs.
Ensuring compliance with ISO Class 7 standards requires consistent monitoring, adherence to evolving regulations, and proactive contamination control strategies. Partnering with experienced cleanroom service providers can help ensure regulatory compliance, operational efficiency, and long-term sustainability.
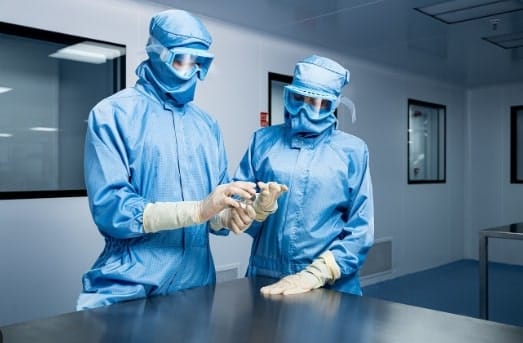