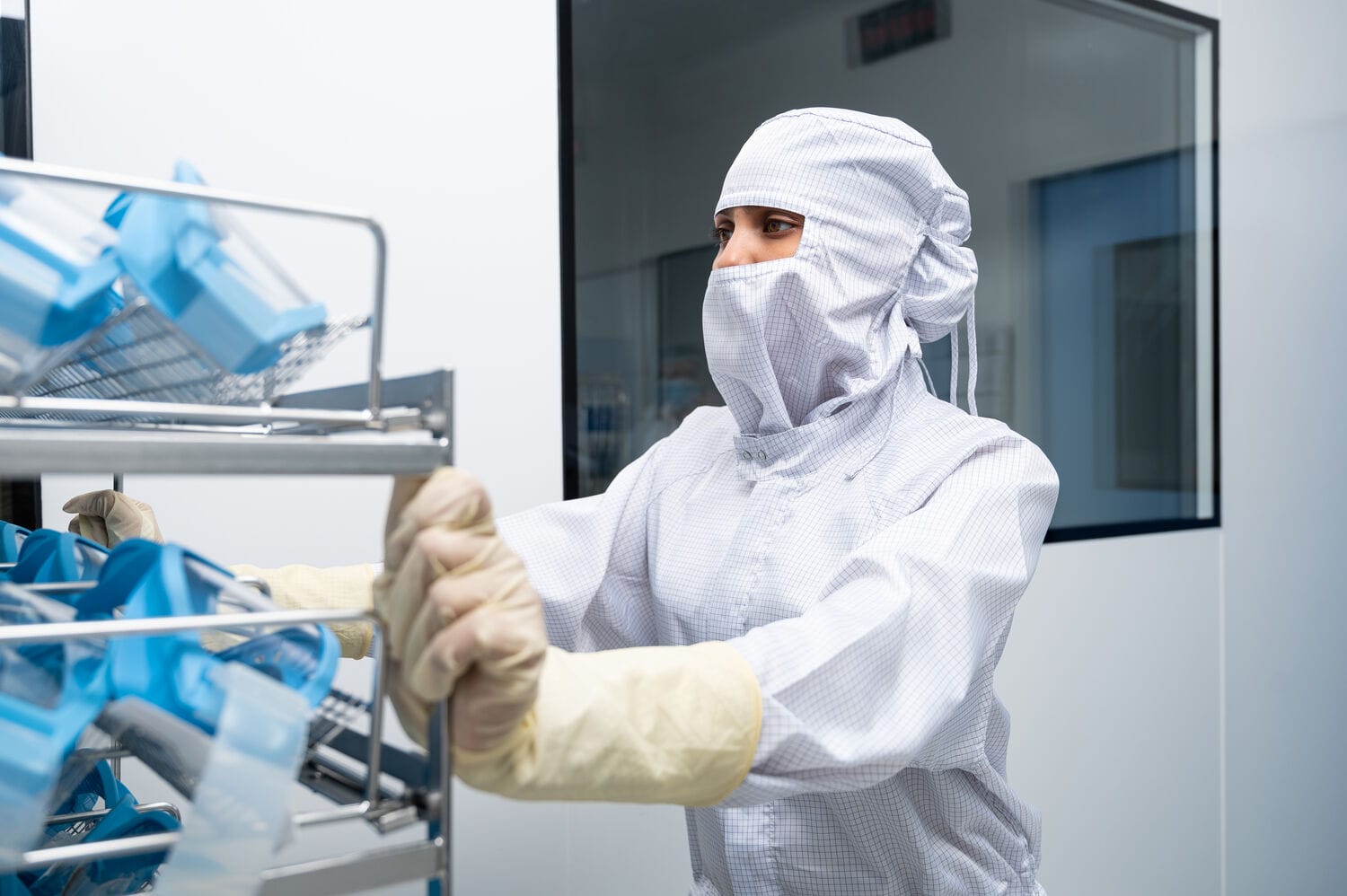
How to ensure compliance with cleanroom standards?
Did you know that up to 80% of cleanroom contamination originates from personnel? Ensuring compliance with cleanroom standards is not just about meeting regulatory requirements—it directly impacts product safety, operational efficiency, and business continuity. Cleanrooms are controlled environments designed to minimize particulates, such as dust, microbes, and chemical vapours, making strict compliance essential.
The fundamental standards that govern cleanroom operations are primarily based on ISO classifications and various regulatory guidelines. ISO 14644 is one of the most widely recognized standards, which classifies cleanrooms according to the number and size of particles permitted per volume of air.
ISO 14644 sets limits on the number and size of airborne particles per cubic metre. The classification levels range from ISO Class 1 (the cleanest) to ISO Class 9 (least strict).
ISO Class | Particle Size Limits (≥0.5 µm per m³) | Typical Industry Usage |
---|---|---|
ISO 5 | 3,520 | Sterile pharmaceutical filling |
ISO 7 | 352,000 | Clean packaging areas |
ISO 8 | 3,520,000 | Support areas |
Additionally, EU GMP Annex 1 emphasizes contamination control strategies, particularly in pharmaceutical manufacturing. It mandates stringent protocols for gowning, air filtration, and microbial control
Why is regular training important for cleanroom compliance?
Regular training is vital for personnel working in cleanrooms to ensure compliance with industry standards and protocols. Cleanroom environments require strict adherence to procedures to prevent contamination, and staff must be well-versed in these protocols. Training programs typically cover areas such as proper gowning procedures, contamination control practices, and equipment handling techniques.
Ongoing training ensures that staff remain aware of the latest industry standards and technological innovations. It also minimizes human error, which is a significant source of contamination risks in cleanroom environments. By investing in regular training, companies can enhance the competency of their workforce, thereby safeguarding product quality and maintaining compliance with regulatory requirements.
How to monitor and maintain cleanroom conditions?
Monitoring and maintaining cleanroom conditions is a critical aspect of ensuring compliance with standards. This involves using various methods and technologies to track air quality, temperature, and humidity levels. Advanced systems, such as IoT-enabled sensors, are increasingly used to provide real-time data on environmental conditions within a cleanroom.
Regular inspections and maintenance are essential to sustaining compliance. These activities help identify potential issues before they escalate into significant problems. For instance, air filters need to be checked and replaced regularly to ensure they are functioning effectively. Consistent monitoring and maintenance not only ensure compliance but also help in optimizing the operational efficiency of cleanroom environments.
What role do cleaning and sanitization play in cleanroom compliance?
Cleaning and sanitization are fundamental components of maintaining a compliant cleanroom. These practices help eliminate contaminants that can compromise the controlled environment. Cleanroom protocols often specify the types of cleaning agents to be used, which are usually non-residue forming and compatible with the materials present in the cleanroom.
Frequency of cleaning operations is also a critical factor. Depending on the class and function of the cleanroom, cleaning may need to be performed multiple times a day. Comprehensive cleaning and sanitization protocols ensure that the cleanroom maintains its integrity and continues to meet the stringent standards required for sensitive manufacturing processes.
What are the consequences of non-compliance with cleanroom standards?
Non-compliance with cleanroom standards can have severe consequences, including product recalls, legal issues, and damage to a company’s reputation. Contaminated products can lead to significant financial losses and pose health risks, particularly in the pharmaceutical and food processing industries. This can result in costly recalls and potential legal liabilities.
Moreover, non-compliance can lead to regulatory penalties and loss of certifications, which are essential for operating in certain industries. The reputational damage from such incidents can be long-lasting, affecting customer trust and business relationships. Therefore, strict adherence to cleanroom standards is not only a regulatory requirement but also a strategic business imperative.
Expert partners help you achieve cleanroom compliance
Maintaining compliance with cleanroom standards is challenging, but you don’t have to do it alone. Lindström’s certified cleanroom garment rental service ensures consistent quality, hygiene, and regulatory compliance. Partner with Lindström for a hassle-free, compliant cleanroom garment solution. Schedule a consultation today to optimise your cleanroom operations.
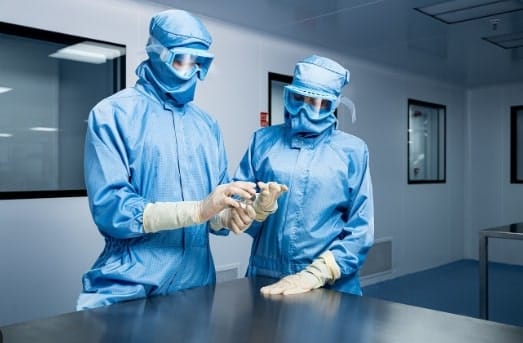