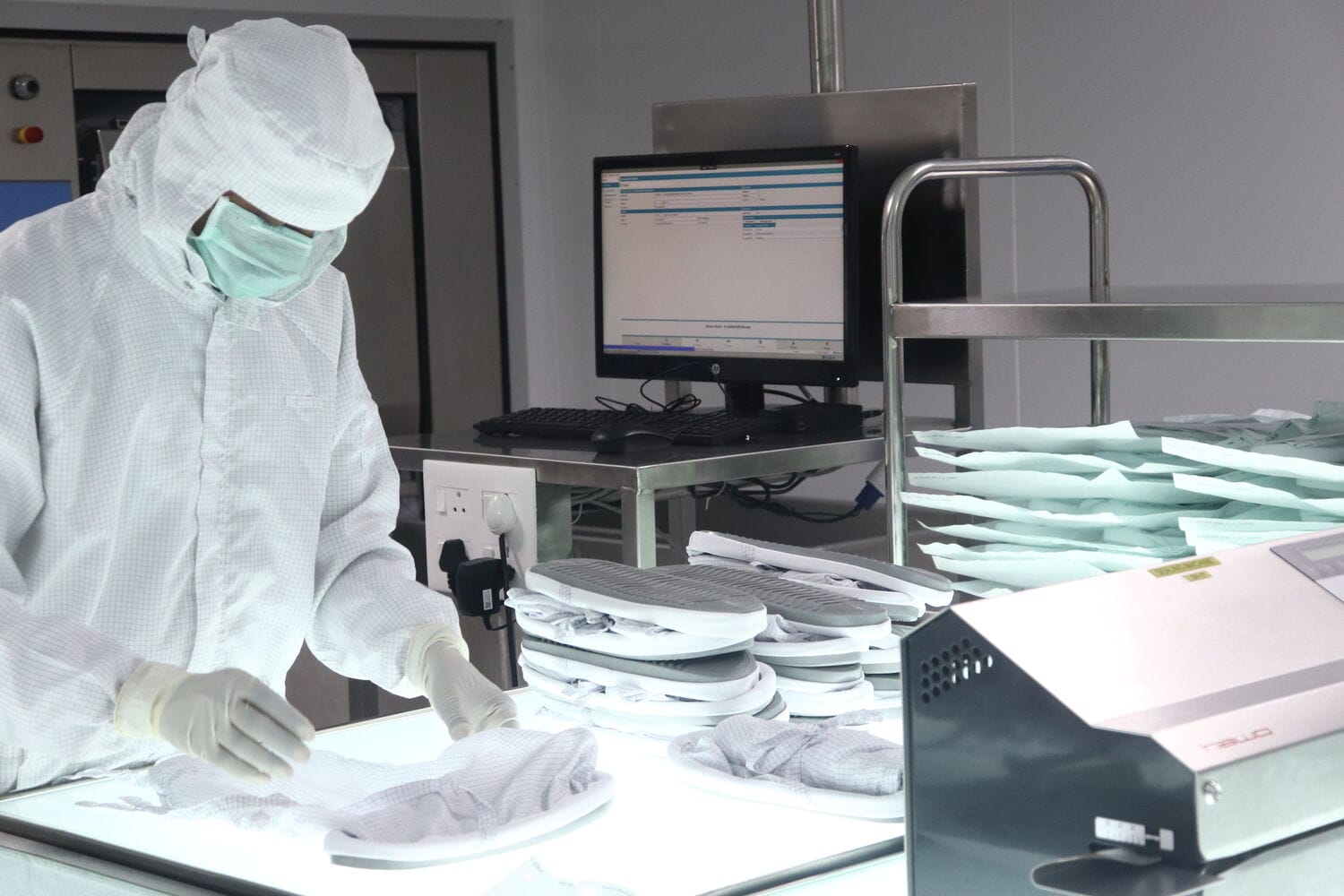
Enhancing safety in the pharma industry: factors associated with drug contamination
Safety is a principle that is very crucial in the field of pharmaceutical products. One small mistake during the drug production process could cause contamination, and this endangers both the patients and the image of the industry. Contamination of drugs compromises the effectiveness of the product, leads to unnecessary recalls, and, in the worst-case scenario, puts the consumers’ health at great risk. Identifying the cause of drug contamination and applying counter-measures is very important because it enables the production of safe and effective pharmaceutical products.
Factors improving safety in the pharmaceutical industry
The drug manufacturing industry is highly regulated. These regulations have been established to protect the patient and the safety of the drug product. Every process in the product cycle, from production to packaging, has to follow safety measures. Safety in pharmaceutical industry in case of drug contamination is not only concerned with preventing further contamination but is also compliant with other principles pertaining to the drug, such as quality, purity, and efficiency of the drug.
There are some aspects that lead to contamination of the drug during the production of pharmaceutical products, and once contamination occurred, it can cause devastating factors such as the company recalling existing drugs in the market, legal issues and suffering of the patients. Hence, a contamination free environment is deemed essential by pharmaceutical industries.
Common reasons behind drug contamination
Drug contamination may happen at any stage of the manufacturing process. Maintaining safety in the pharmaceutical industry requires understanding and managing the primary causes of drug contamination:
- Microbial Contamination: One of the common forms of this kind of contamination is cleansing the wrong way or not at all inner parts of the industry (microbial contamination occurs anytime where buildings and equipment have been used). Invasions into the process can also arise from failure in sanitation, unsatisfactory personal care by employees, and poor conditions in the surrounding environment. For injectables or vaccines, for instance, so much as a very minute percentage of non-sterility has very dangerous implications for the well-being of patients.
- Cross-Contamination: Cross-contamination occurs when drugs of different formulations are produced and kept in contact with one another within the production process. This, too, can arise in the manufacture of multiple products in the same facility, even when there are inter-batch cleaning and decontamination. Cross-contamination may also be a result of the use of improperly gowned and decontaminated personnel who may work on other products as well. Residues of other drugs can result in angioedema and therapeutic failure of drugs, and in certain cases, drugs may be downright poisons.
- Chemical Contamination: Such contamination can occur when chemicals like cleaning agents, solvents even residues of prior manufactured batches are purposely or accidentally allowed to mix with the product during its production. Such practice may alter the formulations of the drug and reasonable probabilities of causing adverse chemical reactions to exist. Sources of contaminants can be equipment that has not been properly cleaned, filters of tissue collated in preparation for air collection, or cartons used to pack the products.
- Particulate Contamination: Particulate contamination is the contamination of drug products with non-drug related artefacts such as dust, fibres, metal shavings or any form of particles. Such particles may be present in the working area, equipment, or primary packaging forms. In the case of sterile medicinal products, the presence of particulates is extremely dangerous, with the possible outcome being infection or inflammation at the site of drug administration.
- Human Error: Human error is the third most preventable cause of drug contamination. Mistakes made while following given procedures and handling of materials, as well as non-combating measures on bacteriological contamination, can be a cause of contamination. Workers who disregard gowning procedures, fail to wash their hands properly, or external contamination sweep through into controlled environments are the same people or procedures that cause contamination in the manufacturing process.
- Cross-Contamination: Drug manufacturing is one of the processes that require the highest level of safety, and thus, an appropriate environment must be created. There should be effective control over some variables, such as temperature, humidity and quality of air, to avoid contamination. Clean rooms serve the purpose of retaining airborne particles and microbes, but if these systems are poorly maintained, some of these contaminants find their way into the production area and infect the drugs undergoing manufacture.
Measures to prevent drug contamination
In order to guarantee anti-drug contamination, firms operating in the pharmaceutical industry should take measures that deal with the root causes of drug contamination. Some of these techniques include the following:
- Strict Gowning and Personal Hygiene Protocols: Employees are expected to comply with proper gowning which includes the wearing of clean room suit, gloves, masks, and hair nets. Employee personal hygiene is also essential as it may involve cleaning one’s hands regularly and using sanitation measures in order to avoid carrying dirt into the clean room.
- Regular Cleaning and Maintenance of Equipment: There is need to ensure that equipment which is used in the manufacture of drugs is always clean and fully operational to avoid chemical and particulates a contamination. There should be cleaning and disinfecting after the end of every production run to remove any residual impurities that may spoil subsequent products.
- Environmental Controls: Environmental control is an important part of drug safety. Area clean rooms MUST have air filtering devices to ensure particles and germs do not penetrate the room. Environmental impact factors including air, temperature and humidity levels are constantly tracked and adjusted so that the environment stays practically free from contamination.
- Training and Education: Employees are required to undergo regular training in order to comprehend the hazards, introduced by contamination, and think through the ways, which will allow these hazards to be avoided Waste treatment and handling staff are trained and educated in a way that they understand why safety controls are important and what is the risk of contamination.
Conclusion
Providing safety in the pharmaceutical industry works through an adequate and complete technology comprehension of the reasons for drug contamination and putting in preventive mechanisms. Each potential risk, be it microbial cystic foul, chemical contamination, human factor mistakes, or cross-contamination, should be contained. The astringent rules of hygiene, clean environments, and positive affirmation towards safety culture will promote the safety of pharmaceutical products and the patients who use them.
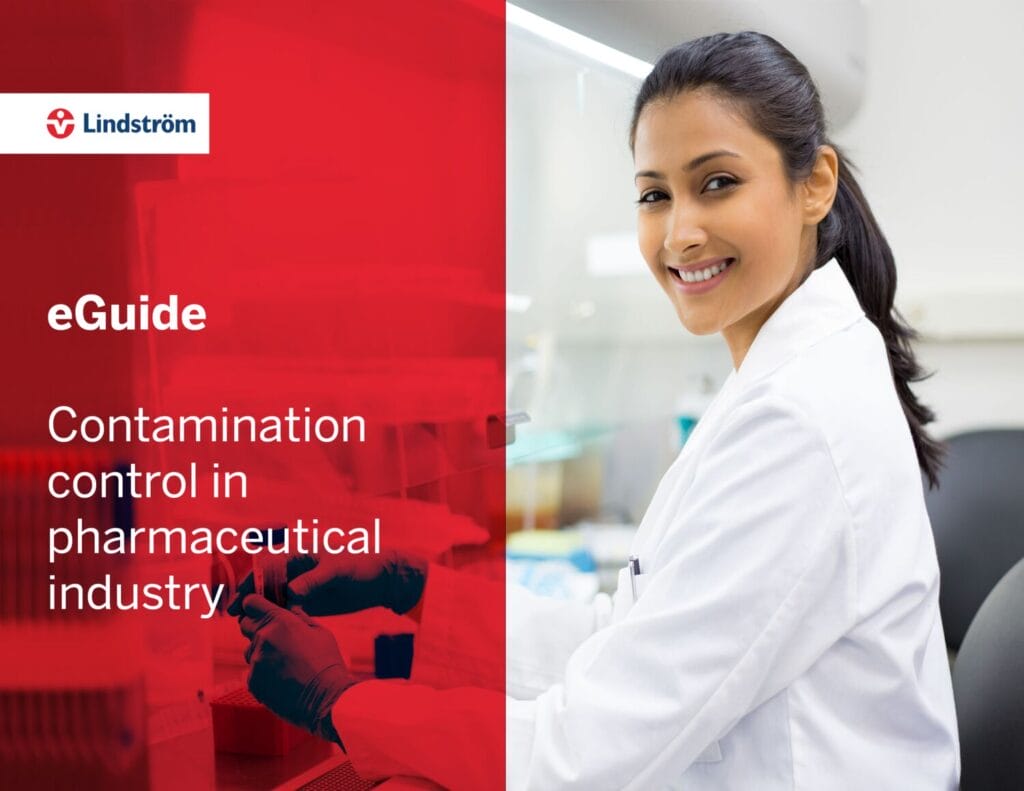