
Demystifying workwear regulations in the food industry
Workwear regulations in the food industry are critical to ensuring both safety and hygiene within food production and preparation environments. These regulations are designed to protect not only the employees but also the end consumers by minimising the risk of contamination. The importance of these regulations cannot be overstated, as non-compliance can lead to severe consequences. These may include fines, legal action, and damage to the company’s reputation, not to mention potential public health risks.
Ensuring proper workwear adherence helps maintain a clean and safe environment, which is crucial for preventing foodborne illnesses. The regulations provide a framework that guides food industry businesses in selecting appropriate protective clothing and gear that meet safety standards. This ensures that all personnel are adequately protected and that food is processed under hygienic conditions, ultimately safeguarding consumer health.
Key regulatory bodies and their roles
Several key regulatory bodies are responsible for setting workwear standards in the food industry. In the United States, the Occupational Safety and Health Administration (OSHA) plays a significant role by enforcing health and safety regulations that require appropriate protective clothing for workers in various industries, including food processing.
Another vital organization is the Food and Drug Administration (FDA), which provides guidelines that ensure food safety and hygiene compliance. The FDA’s regulations cover everything from proper hand hygiene to the type of clothing that should be worn in food production areas to prevent contamination. International standards organizations like the International Organization for Standardization (ISO) also contribute by establishing global safety standards that many food industry companies adhere to.
Essential workwear requirements
In the food industry, the type of workwear required can vary significantly depending on the specific role of an employee. However, there are general standards that apply across the board to ensure hygiene and safety. Essential protective clothing includes items such as aprons, gloves, hairnets, and non-slip shoes, all designed to prevent contamination and ensure a safe working environment.
For roles directly involved in food processing, more stringent measures may be required. This might include additional protective gear such as face masks and full-body suits to prevent any risk of contamination. These standards are set to ensure that all personnel contribute to maintaining high hygiene compliance, thereby safeguarding the food products and ultimately, consumer health.
Common challenges in compliance
While the benefits of adhering to workwear regulations are clear, many companies face challenges in maintaining compliance. One common issue is the cost associated with purchasing and maintaining high-quality protective clothing. This can be a significant expense, particularly for smaller businesses.
Additionally, employee training is crucial to ensure that all staff understand the importance of proper workwear usage and compliance. This requires ongoing education and monitoring, which can be resource-intensive. Furthermore, maintaining uniform quality can be challenging, especially in high-turnover environments where employees frequently change.
Best practices for maintaining compliance with workwear regulations
To effectively comply with workwear regulations, companies can implement several best practices. Regular audits are essential to ensure that all workwear meets the necessary safety standards and hygiene compliance. These audits help identify and address any potential issues before they become significant problems.
Employee education is another critical strategy. Providing regular training sessions ensures that staff understand the importance of workwear regulations and how to adhere to them. Additionally, choosing reliable suppliers, such as Lindström, who offer comprehensive textile rental services, can help companies maintain compliance efficiently. These suppliers provide high-quality, sustainable workwear solutions tailored to the specific needs of the food industry.
Future trends in workwear regulations
The future of workwear regulations in the food industry is likely to be influenced by technological advancements and evolving safety standards. Innovations such as IoT-enabled garment tracking and automation are already playing a role in streamlining compliance and improving workwear management.
As safety standards continue to evolve, we can expect stricter regulations and more comprehensive guidelines to emerge. Companies that stay ahead of these trends by adopting new technologies and sustainable practices will be better positioned to maintain compliance and ensure the safety and hygiene of their operations.
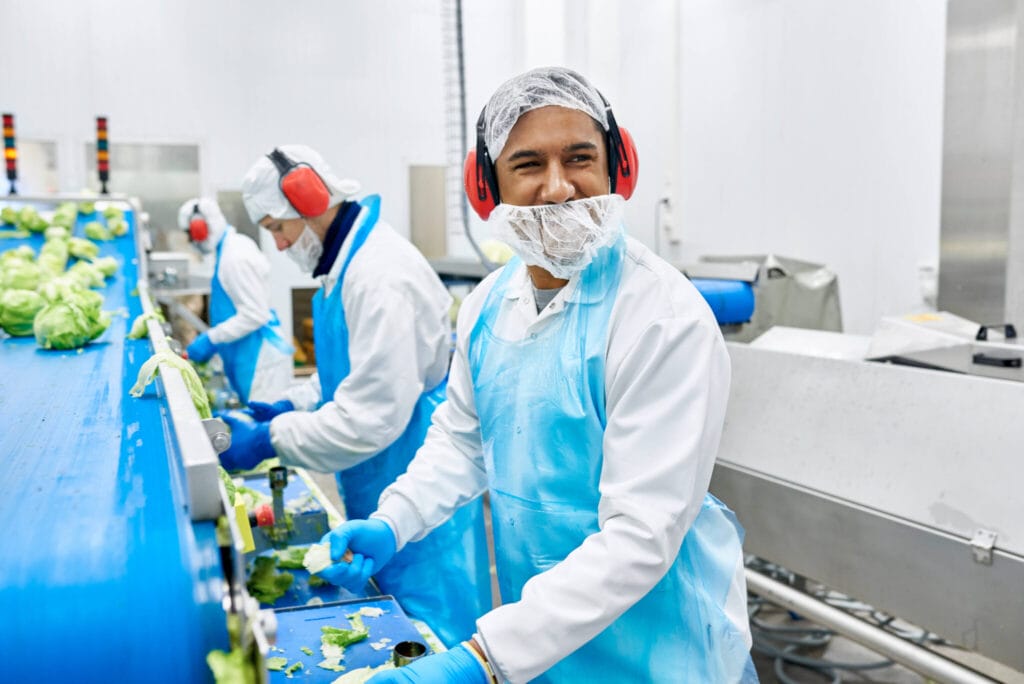