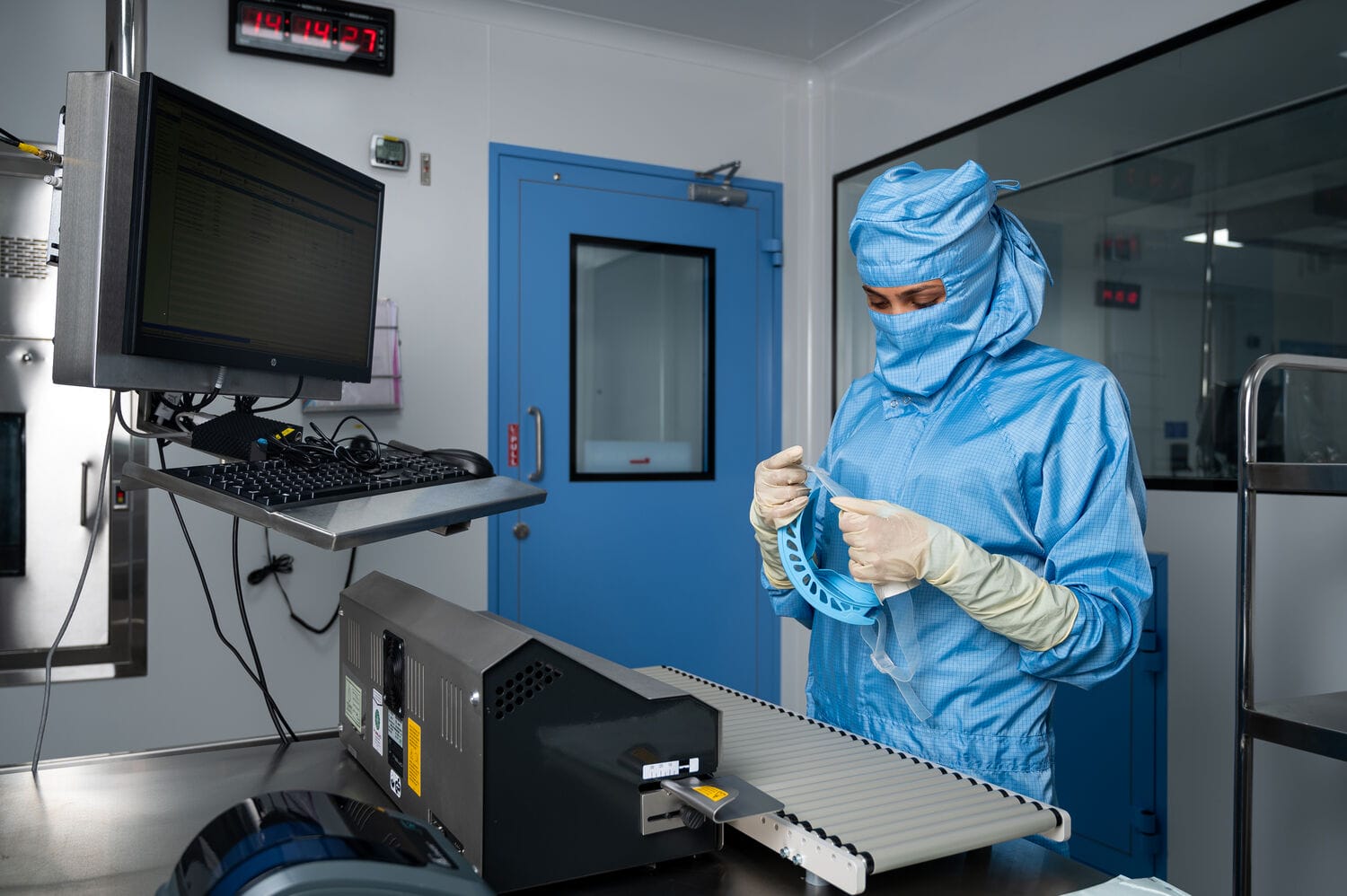
Can improper gowning affect product quality?
In cleanroom environments, what your people wear—and how they wear it—has a huge impact on operations. Improper gowning is one of the most common and preventable causes of contamination in industries like pharmaceuticals, biotechnology, and precision electronics. Yet, it often flies under the radar.
Let’s explore what improper gowning really means, why it compromises product quality, and how companies like Lindström are helping manufacturers mitigate its risks, without adding complexity to daily operations.
What is improper gowning?
Improper gowning refers to any deviation from correct procedures when donning (or doffing) protective clothing in cleanrooms or controlled environments. These garments—coveralls, hoods, gloves, goggles, boots—are designed to act as a barrier between human contaminants (like skin flakes or microbes) and sterile production zones.
Mistakes can happen at multiple points:
- Skipping steps in the gowning sequence
- Wearing garments incorrectly (e.g. exposed wrists or loose zippers)
- Using damaged or unvalidated clothing
- Rushing through dressing routines
- Wearing the wrong garment for the cleanroom class
Improper gowning introduces contamination risks that can jeopardise entire production lines.
Why does it matter?
In cleanrooms, human beings are the largest source of contamination, accounting for up to 80–90% of particulates and microbes. Every touch, breath, or movement creates potential exposure.
When gowning protocols aren’t followed precisely, particles and microorganisms can be introduced into the cleanroom, undermining:
- Sterility assurance in pharmaceutical production
- Product integrity in electronics manufacturing
- Regulatory compliance, especially with EU GMP Annex 1
The consequences? Batch recalls, product waste, supply chain delays, and reputational damage.
What are the consequences of improper gowning for manufacturers?
The ripple effects of gowning failures go far beyond a single error.
Consequence | Business Impact |
---|---|
Product recalls | Financial losses and reputational harm |
Failed audits | Risk of regulatory penalties |
Production downtime | Missed market deadlines |
Loss of trust | Damaged customer relationships |
Staff re-training | Increased overheads |
Repeated non-compliance with gowning procedures in highly regulated industries can trigger stricter inspections or even manufacturing licence suspensions.
What are the best practices for proper gowning?
Preventing gowning errors doesn’t require perfect people—it requires the right systems, training, and support.
Here’s what works:
1. Detailed, role-based training
Train all personnel in the exact gowning steps required for their cleanroom grade. Include visual aids, hands-on sessions, and regular refresher courses.
2. Clear zoning and visual guidance
Use floor markings, mirrors, and posters in gowning areas to guide personnel step-by-step.
3. Validated garments for each cleanroom class
Garments must meet the particle and microbial retention standards required for ISO Class 5–8 zones and should be tested regularly.
4. Regular inspections and audits
Conduct routine observations of gowning practices to identify gaps or drift from protocols.
5. RFID and lifecycle tracking
Track how many times each garment has been washed or sterilised to avoid exceeding its validated lifespan.
We help you get gowning right, every time
At Lindström, we understand the high stakes of cleanroom operations and the challenge of managing gowning compliance consistently across shifts, teams, and facilities.
That’s why our cleanroom service is designed to make proper gowning easier, more reliable, and fully traceable.
Here’s how we support you:
- Validated cleanroom garments tailored for ISO 14644 classifications
- Certified laundering and decontamination in ISO-classified laundries
- RFID-enabled garment tracking through eLindström for lifecycle transparency
- Automated garment rotation to prevent overuse and ensure always-clean availability
- Onboarding and compliance training support for your staff
We also help ensure alignment with EU GMP Annex 1, which places increased emphasis on personnel hygiene, gown qualification, and laundry validation.
A Quick Comparison: Proper vs. Improper Gowning
Element | Proper Gowning | Improper Gowning |
---|---|---|
Garment condition | Tested, intact, within lifecycle | Torn, expired, or incorrect fit |
Donning sequence | Followed step-by-step | Skipped or rushed |
Cleanroom entry | Hands-free, unidirectional flow | Contact with contaminated surfaces |
Tracking | RFID-monitored | Manual or untracked |
Hygiene | Trained and compliant | Untrained or unaware personnel |
Correct gowning as a part of contamination control
Improper gowning can put your cleanroom at risk even if everything else is in place. It should be done as part of a consistent system that helps your team work safely and keeps your products protected.
At Lindström, our cleanroom garment service is built to make that easier. We help you stay compliant, track garment use, and reduce the risk of contamination so you can focus on your core work with confidence.
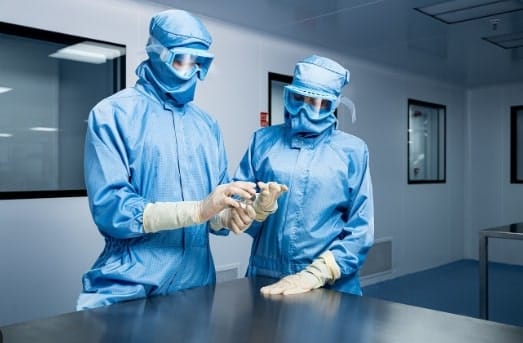