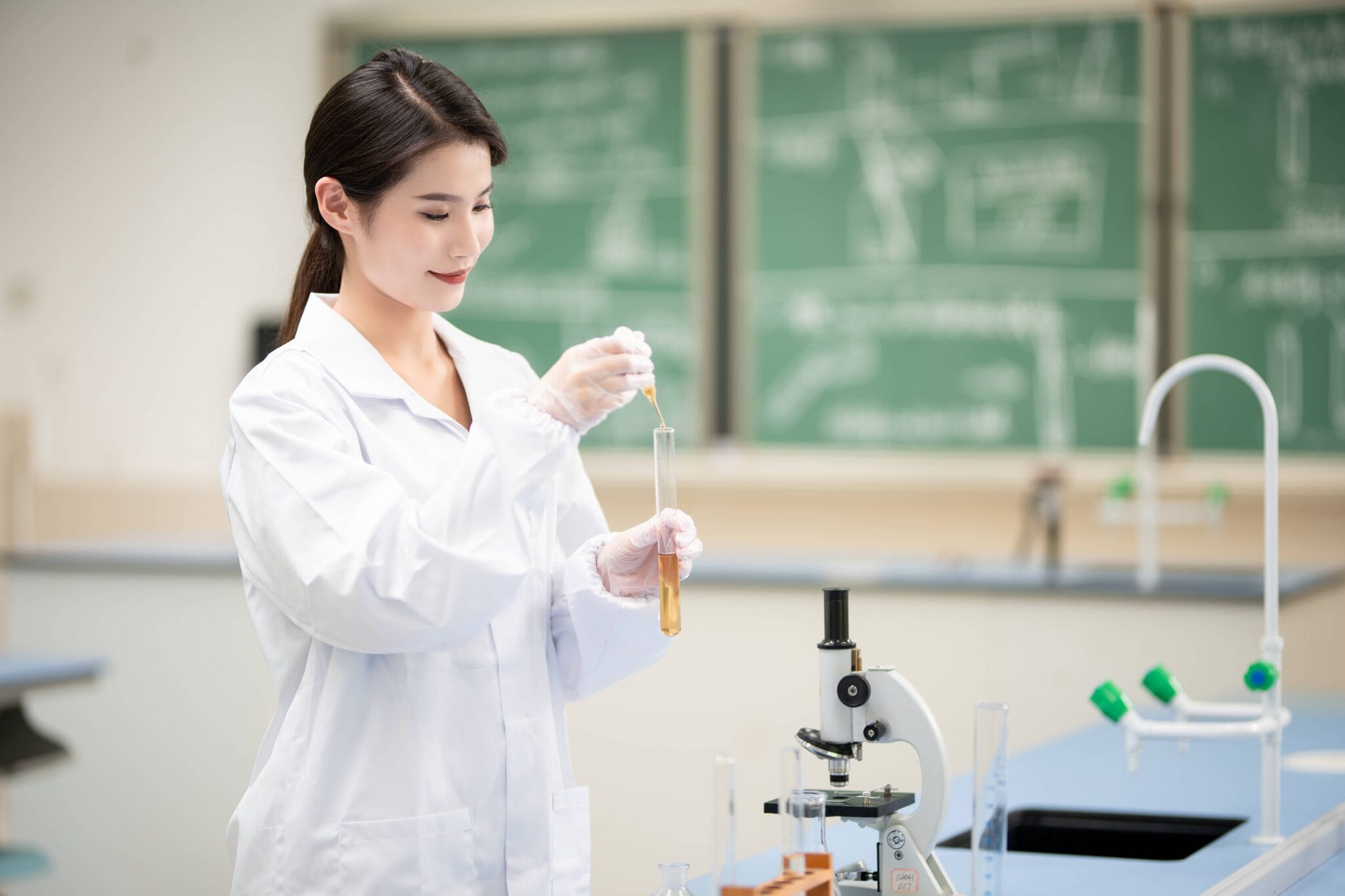
Upholding health and safety in the pharmaceutical sector
Health and safety are vital for workforce longevity and productivity enhancement in the pharmaceutical industry. Employees, donned in their pharma uniforms, frequently encounter biological and chemical risks threatening their health. Moreover, inadequate safety standards and non-compliance negatively impact workplace efficiency and pose serious business continuity issues in the future.
Hence, it becomes critical to maintain peerless health and safety practices and ensure all employees adhere to such standards. Here, we discuss strategies for maintaining superior health and safety standards in the pharmaceutical industry.
Risk Assessment:
Conducting a thorough risk assessment is paramount in identifying potential workplace hazards and safeguarding employees. In the pharma sector, health and safety risk assessment is an absolute legal necessity. This involves examining the workplace to pinpoint dangers and their origins.
Health and safety risk assessment generally includes the following steps:
- Examine the facility grounds to uncover potential risks and scrutinize the accident logs.
- Once the threats are identified, determine which employees are most prone to these hazards.
- Evaluate how you can mitigate workplace dangers; formulate a concrete action plan. The aim should be to minimize or eliminate the hazard to improve health and safety.
- Document the identified risks and actions taken to demonstrate that issues have been recognized and addressed.
- Revisit the risk assessment report annually to ensure efficient implementation of health and safety measures in the workplace.
Primary Laboratory Safety:
In the pharmaceutical sector, adhering to fundamental lab safety norms is obligatory. The Occupational Safety and Health Administration (OSHA) offers detailed guidelines on practicing lab safety. It is essential that all employees are informed about key health and safety practices and take precautions when working in high-risk environments.
Following OSHA guidelines, these steps can be taken to maintain health and safety in the laboratory:
- Regularly clean, especially if employees are exposed to chemical hazards or particles. Cleaning tools and surfaces are integral, as are employees wearing a laboratory uniform that is regularly cleaned.
- Wash hands routinely and thoroughly to prevent the spread of bacteria, viruses, or hazardous chemicals.
- Prohibit eating, drinking, or smoking inside the laboratory.
- Enforce wearing appropriate Personal Protective Equipment (PPE) inside the laboratory. A medical laboratory uniform, including coveralls, eye protection, headgear, shoe covers, etc., is essential.
- Correctly label containers.
- Ensure all equipment is functioning safely and correctly.
- Maintain clean and sanitized corridors.
- Perform daily risk evaluations.
Occupational Injury Prevention:
Employees are the most significant asset of any pharmaceutical company. To safeguard their health and well-being and maintain a productive work environment, you must strive to establish an “injury-free” environment. Implement safety measures that eradicate injuries and minimize incidents.
Key strategies include:
- Exhibit and inspire an injury-free work culture via leadership commitment.
- Educate employees about their role in maintaining their own safety and those around them.
- Implement effective management strategies to identify, control, and reduce hazards to an acceptable limit.
- Prevent incident recurrence through effective inquiry and proactive strategy formation.
- Implement and enforce company-wide safety standards across all pharmaceutical facilities, offices, and laboratories.
- Conduct “injury-free” surveys as appropriate to uncover improvement opportunities.
Chemical Handling Health & Safety Standards:
Transporting and managing hazardous chemicals can be perilous. If executed improperly by untrained personnel, it can lead to chemical leaks, explosions, and fires. The use of the Classification of Chemicals can assist in handling hazardous chemicals and mitigating associated risks.
The Classification of Chemicals helps determine how chemicals can cause adverse effects and how they should be accurately labelled and handled to avoid health risks or accidents. High temperature, pressure, or oxidation often cause chemicals to explode or discharge. By moderating the oxidation display and understanding the correct flammable limits, pharmaceutical organizations can reduce risks.
Implementing emergency showers can also prove instrumental when chemicals directly contact users. It can help wash away chemicals from the PPE, including the medical laboratory uniform and skin, averting health hazards. Consider setting up eye wash stations within the facility to mitigate major damage risks.
Conclusion:
Upholding employee health and safety at the workplace is a prime obligation of employers. Instituting optimal safety practices and ensuring employees’ adherence to them can improve health and safety standards within the workplace.
To learn more about contamination control in the pharmaceutical industry, download the below eGuide’
Frequently Asked Questions (FAQ)
Because of all the risks that exist when handling chemical and biological substances, health and safety in the pharmaceutical sector are of great importance. Employees are often exposed to these hazards compromising well-being and productivity. Staff are endangered by safety deficits. These measures can also pose a threat to product integrity and business continuity. Lindström stresses stringent safety protocols, along with proper attire, to reduce risks. These actions maintain a secure working environment.
Begin with risk assessment because that action is important. This assists you to identify as well as to reduce potential hazards within pharmaceutical facilities. Organizations can develop targeted strategies to minimize risks by examining employee exposure levels, accident logs, and workplace conditions. Lindström advocates for the need for regular risk evaluations along with the implementation of appropriate safety measures that will include the use of specialized uniforms to ensure a workplace that is safe and compliant.
Lindström underscores several necessary laboratory safety practices: cleanliness must be maintained, strict hand hygiene must be enforced, food as well as drink are prohibited in lab areas, and appropriate Personal Protective Equipment (PPE) must be ensured. The proper labeling of the containers is quite vital. Vital equipment checks are also done regularly. These steps safeguard staff and items also stop pollutants in drug labs.
Pharmaceutical uniforms critically act as a barrier against hazardous substances and contamination exposure. Lindström offers clothing tailored to satisfy industry requirements. This attire protects employees, also it maintains product integrity. Regularly laundering as well as maintaining these uniforms are important to uphold hygiene together with complying within pharmaceutical operations.
Proper chemical handling can prevent fires, explosions, and leaks. For ensuring accurate labelling as well as handling, Lindström recommends use of the Classification of Chemicals so you can understand potential hazards. Risks linked to chemical exposure can also be reduced by implementing emergency showers and eye wash stations.
Creating an injury-free workplace involves leadership commitment, employee education, effective hazard management, and the enforcement of company-wide safety standards. Lindström emphasizes the importance of conducting regular “injury-free” surveys to identify improvement opportunities and reinforce a culture of safety.
Lindström offers complete textile solutions, fulfilling an important function designed for the pharmaceutical sector. High-quality uniforms are included within their solutions, hygienic maintenance is ensured, and organizations are supported as they implement safety protocols. Pharmaceutical companies can improve health and safety standards through partnering with Lindström, because they will ensure a secure environment for both employees and products.